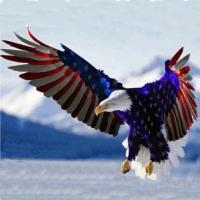
Monday, May 28, 2012 8:04:21 PM
http://www.themoldingblog.com/2012/04/20/liquid-metal-in-the-iphone5/
Liquid Metal in the iPhone5?
Posted on April 20, 2012 by Doug Smock 0
Several factors are converging to indicate that Apple believes its liquid metal injection molding technology is ready for prime time.
Liquid metal was invented at Cal Tech in 1993, but the commercialization process has been a struggle because of the tremendous innovations needed to process the material in a system close to plastic injection molding.
The exotic metal brews concocted by Cal Tech are amorphous structures that don’t have the inherent weaknesses found in crystalline structures. The zirconium-titanium alloys are approximately 250% stronger than commonly used titanium alloys such as Ti-6Al-4V. Certain combinations of metals can be formed into amorphous shapes through a rapid quenching process.
That’s the heart of the invention—and also the dilemma. How do you do that?
Apple believed enough in the potential of the high-tech process to acquire exclusive licensing rights for consumer electronics. The cash payments are providing a much needed financial lifeline for Liquidmetal Technologies (Rancho Santa Margarita, CA), which is commercializing the technology in fits and starts.
The big breakthrough, in my opinion came when Engel, a major injection molding technology powerhouse based in Austria, agreed to help develop process technology for Liquidmetal.
At NPE2012 in Orlando, FL earlier this month, Mark Sankovitch, president of Engel North America, told me that there has been significant progress in recent months in building commercial, mass production liquid metal injection molding processes. Sankovitch discussed Engel’s work very carefully because of corporate sensitivities involved and the highly proprietary nature of the work.
Needless to say the liquid metal molding machines that are now in place are like no injection molding machines ever seen before. The metal composition is prepared in a vacuum chamber — not in a screw with a plasticizing barrel as is the case with plastics. Engel has worked on the interface between the vacuum chamber and the injection unit as well as the process control, an Engel forte.
Want more details? Forget about it.
Engel is just one of the key partners that Liquidmetal has lined up. In a March 30 earnings release, Tom Steipp, president and CEO, commented, “Liquidmetal Technologies has reached an important milestone enabling it to realize the benefits of its partner relationships. By the end of 2011, we are now able to source alloy feedstock from Materion, process our alloys using next generation molding machines from Engel and manufacture commercial parts at our contract manufacturer, Visser Precision Cast.” Visser Precision Cast has a “coming soon” Web site. Materion (Mayfield Heights, OH) is a publicly held advanced materials company.
In another important development, Liquidmetal Technologies announced March 6 that it had begun shipping "commercial parts" ("prototypes", not commercial purchase orders, later affixed to this by Steipp on May 15) to customers world-wide in December, 2011.
It’s possible that Apple may use Liquidmetal for the antenna in its next iPhone release – the iPhone 5. Success in the injection molding process would allow integration of the antenna into the phone housing and allow other molded features that would enhance the design, improve reliability and reduce costs. The new iPhone could make its debut at the Apple Worldwide Developers Conference in San Francisco in June.
Recent LQMT News
- Form 10-Q - Quarterly report [Sections 13 or 15(d)] • Edgar (US Regulatory) • 05/20/2024 08:11:00 PM
- Form NT 10-Q - Notification of inability to timely file Form 10-Q or 10-QSB • Edgar (US Regulatory) • 05/15/2024 08:49:57 PM
- Form 8-K - Current report • Edgar (US Regulatory) • 05/09/2024 09:05:11 PM
- Form 4 - Statement of changes in beneficial ownership of securities • Edgar (US Regulatory) • 11/21/2023 10:15:45 PM
- Form 4 - Statement of changes in beneficial ownership of securities • Edgar (US Regulatory) • 08/21/2023 10:26:27 PM
- Form 10-Q - Quarterly report [Sections 13 or 15(d)] • Edgar (US Regulatory) • 08/10/2023 08:37:18 PM
North Bay Resources Announces Mt. Vernon Gold Mine Startup, Sierra County, California • NBRI • Aug 5, 2024 9:00 AM
Fifty 1 Labs, Inc. and All-In-Extracts Announce Joint Venture to Develop and Release New Testosterone Boosting Supplement • BLEG • Aug 5, 2024 8:30 AM
Kona Gold Beverages, Inc. Announces Strategic Initiatives and Corporate Direction Changes • KGKG • Aug 2, 2024 2:00 PM
POET and Luxshare Tech Expand Product Offerings for Artificial Intelligence Networks • POET • Aug 1, 2024 9:28 AM
Management Discusses Financial Filings of Global Arena Holding Inc., for 10-K 2023 and 10-Q, 1st Quarter 2024 • GAHC • Aug 1, 2024 9:14 AM
VAYK Announces LOI to Acquire $1 Million Home Service Company to Support Airbnb Business • VAYK • Aug 1, 2024 9:00 AM