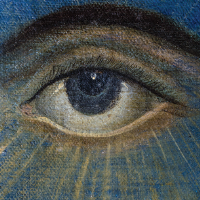
Wednesday, September 23, 2020 8:58:54 PM
Chemistry, Manufacturing, and Control (CMC) Information for Human Gene Therapy Investigational New Drug Applications (INDs)
Guidance for Industry JANUARY 2020
https://www.fda.gov/media/113760/download
Some relevant sections here:
It may be crucial to establish CQAs as early as possible particularly when you plan to make manufacturing changes during product development because well-established CQAs are generally necessary for demonstrating product comparability by analytical methods. For additional information regarding establishing CQAs, please see FDA’s Guidance for Industry: “Q8(R2) Pharmaceutical Development” (Ref. 6), and “Q11 Development and Manufacture of Drug Substances” (Ref. 8). Information to support a CQA and results from specific studies or published literature may be included in Module 3 of the CTD in the “Manufacturing Process Development (3.2.S.2.6)” section or the “Pharmaceutical Development (3.2.P.2)” section (see Ref. 1) depending on whether the attribute pertains to a DS or a DP. Information may also be linked to the relevant nonclinical or clinical sections of the application in the CTD.
f. Manufacturing Process Development (3.2.S.2.6)
You should provide a description and discussion of the developmental history of the manufacturing process as described in the “Description of Manufacturing Process and Process Controls (3.2.S.2.2)” section of the CTD.
For early stage INDs, there may be differences between the manufacturing and testing of the toxicology lots and the material you plan to use in the clinical studies. For later stage INDs, there may be changes to the manufacturing process as part of process development, optimization, or under certain conditions there may be reprocessing step(s). In both situations, we recommend that you describe how manufacturing differences are expected to impact product safety and activity and to provide batch analysis information in the “Batch Analysis (3.2.S.4.4)” section of the CTD.
If you make significant manufacturing changes, then comparability studies may be necessary to determine the impact of these changes on the identity, purity, potency, and safety of the product. The extent of comparability testing would depend on the manufacturing change, the ability of analytical methods to detect changes in the product, and the stage of clinical development. For first-in-human studies, any differences between toxicology lots and clinical lots should be assessed for their impact on product safety. For later phase studies, especially those designed to measure product efficacy, differences in clinical lots should be assessed for their impact on product safety and activity.
Please note that it is important to retain samples of the DS and manufacturing intermediates, when possible, in the event that comparability studies are requested during future product development or after licensure of the investigational DP.
d. Batch Analysis (3.2.S.4.4)
You should include a table with test results for batches (or lots) of the DS that you have manufactured. For early stage INDs, this may include toxicology lots, developmental batches, engineering runs, or a single manufacturing run for clinical grade material. We recommend that you gain adequate experience with a new clinical manufacturing processes prior to making clinical material. This is especially critical following technology transfer to a new manufacturing facility, when manufacturing changes occur during development, and when multiple manufacturing facilities will be utilized. Please note that batches manufactured in different ways should be clearly identified in the submission. Information regarding process development of these materials should be outlined in the “Manufacturing Process Development (3.2.S.2.6)” section of the CTD. We recommend that you annually update this section of your IND as new batches are produced. You should indicate any batches that fail to meet release specifications and any action taken to investigate the failure according to your Quality Unit procedures (for Quality Unit information please see section V.C.1., “Appendices – Facilities and Equipment (3.2.A.1),” of this guidance). We recommend that you retain samples of production lots for use in future assay development, validation, or comparability studies.
Recent NWBO News
- Biophma Announces Exclusive In License for Dendritic Cell Technology, Sending Shares Higher • AllPennyStocks.com • 06/17/2024 04:40:00 PM
- Form 8-K - Current report • Edgar (US Regulatory) • 06/04/2024 09:11:16 PM
- Form DEF 14A - Other definitive proxy statements • Edgar (US Regulatory) • 06/03/2024 09:22:55 PM
- Form PRE 14A - Other preliminary proxy statements • Edgar (US Regulatory) • 05/22/2024 08:13:36 PM
- Form 10-Q - Quarterly report [Sections 13 or 15(d)] • Edgar (US Regulatory) • 05/10/2024 09:04:57 PM
- Form NT 10-K - Notification of inability to timely file Form 10-K 405, 10-K, 10-KSB 405, 10-KSB, 10-KT, or 10-KT405 • Edgar (US Regulatory) • 03/01/2024 10:04:38 PM
- Form 4 - Statement of changes in beneficial ownership of securities • Edgar (US Regulatory) • 12/02/2023 01:31:35 AM
- Form 8-K - Current report • Edgar (US Regulatory) • 11/16/2023 10:11:54 PM
- Epazz, Inc. (OTC Pink: EPAZ) ZenaDrone Demonstration to Defense Departments of UAE and Saudi Arabia • InvestorsHub NewsWire • 11/15/2023 12:19:31 PM
- Form 10-Q - Quarterly report [Sections 13 or 15(d)] • Edgar (US Regulatory) • 11/09/2023 09:30:39 PM
- Epazz, Inc. (OTC Pink: EPAZ) US Navy Collaboration ZenaDrone 1000 • InvestorsHub NewsWire • 11/09/2023 01:00:34 PM
- Epazz, Inc. (OTC Pink: EPAZ) US Navy Collaboration ZenaDrone 1000 Extreme Weather Demo • InvestorsHub NewsWire • 11/07/2023 12:29:43 PM
- Form 10-Q - Quarterly report [Sections 13 or 15(d)] • Edgar (US Regulatory) • 08/09/2023 08:36:14 PM
Southern Silver Files NI43-101 Technical Report for its Updated Preliminary Economic Assessment for the Cerro Las Minitas Project • SSV • Jul 25, 2024 8:00 AM
Greenlite Ventures Completes Agreement with No Limit Technology • GRNL • Jul 19, 2024 10:00 AM
VAYK Expects Revenue from First Airbnb Property Starting from August • VAYK • Jul 18, 2024 9:00 AM
North Bay Resources Acquires Mt. Vernon Gold Mine, Sierra County, California, with Assays up to 4.8 oz. Au per Ton • NBRI • Jul 18, 2024 9:00 AM
Nightfood Holdings Signs Letter of Intent for All-Stock Acquisition of CarryOutSupplies.com • NGTF • Jul 17, 2024 1:00 PM
Kona Gold Beverages Reaches Out to Largest Debt Holder for Debt Purchase Negotiation • KGKG • Jul 17, 2024 9:00 AM