Followers | 20 |
Posts | 6647 |
Boards Moderated | 1 |
Alias Born | 06/18/2018 |
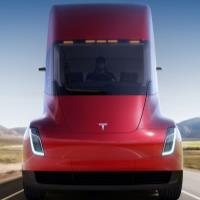
Tuesday, September 22, 2020 8:03:53 PM
- Current Tech: 135 Giga Nevada's, $2T investment, 2.8M people needed for this goal => drastic improvement in efficiency needed
- Plan to halve the cost per kWh (!)
- not dependent on a single innovation => no single point of failure
?
- Tabless cell => improved charge rate vs. cell diameter curve
- 5x shorter electrical path
- 20% higher power density due to tabless
- 16% higher range from form factor alone
- 14% $/kWh reduction from form factor+tabless?
- 4680 cell
- Kato Road pilot plant has 10GWh design capacity, to be reached in about a year
- Production plants to be ~20GWh/y
- Dry electrode process
- 10x footprint reduction
- 10x energy reduction
- "close to working" => does work, currrently poor yield?
- 20GWh/y per line, 7x increase per line
- "Tesla is aiming to be the best at manufacturing of any company on earth", manufacturing as long term competitive advantage
- Formation 25% of CAPEX
- 86% CAPEX reduction
- 75% footprint reduction?
- 10x production density increase *across plant*
- 75% CAPEX reduction *across plant*
- Tesla goals:
- 200Gwh/y in 2022, 100GWh internal
- 3TWh/y in 2030?
- Formation+dry electrode: 18% $/kWh reduction
- Raw Silicon anode
- Ion polymer coating, integrate with binder
- design for expansion, don't fight it?
- 20% range increase
- 5% $/kWh reduction?
- Zero Cobalt
- 15% $/kWh reduction on cathode level?
- 3 battery cathode tiers:
- LFP, NMx (33% Manganese, 66% Nickel), Nickel, depending on application?
- Cathode production *very* complicated, in part due to organic process/supply chain growth => potential
- metallic Nickel, no sulfate
- 66% less CAPEX
- 76% less process cost
- no wastewater
- simpler recycling
- 80% less miles travelled
- 12% $/kWh reduction?
- 33% reduction in lithium cost
- Tesla to use Lithium clays in Nevada (rights secured by Tesla), acid free saline extraction
- TWh scale supply secured
- (No Lithium coup in Bolivia?! I'm shocked I tell you, shocked!)?
- 100% cell recycling *today* by third parties, in house recycling starting to ramp up next quarter at Giga Nevada
- Front and rear of the car single-piece cast, connected by a structural battery pack
- no modules
- non cell portion of pack "has negative mass" because of mass savings in other parts of the vehicle
- pack is a "honeycomb stucture between face sheets" => exremely high stiffness, higher than normal car
- better volumetric efficiency => cells more in the center of the vehicle => less chance of cell puncture during side impact
- 10% mass reduction (of pack or vehicle?)
- 14% range improvement opportunity
- much simpler vehicle production?
- Grand Total (POTENTIAL, not currently realized):
- 54% range increase
- 56% less $/kWh
- 69% less CAPEX per GWh
- start seeing benefits in 12-18 months
- full potential probably achieved in about 3 years?
- Long term: 20M car sales per year
- 3 years from compelling $25k car *at a profit*
- PLAID:
- <2 sec 0-60, <9 sec quarter mile, >1100hp
- "best track time of any production car ever"
- preoders open now, available end of 2021
- 520+mi range, 200mph
- 140k?
- No mention of energy density on cell or pack level, only range increase potential, likely to keep OEMs guessing as to where the range improvements come from exactly (eg cell vs pack level)
Recent TSLA News
- Form 144 - Report of proposed sale of securities • Edgar (US Regulatory) • 09/23/2024 08:27:57 PM
- Apollo Eyes $5 Billion Investment in Intel; TSMC and Samsung Explore UAE Chip Projects, and More • IH Market News • 09/23/2024 10:32:25 AM
- Nike Shares Surge 7% Pre-Market as Elliott Hill Becomes CEO; FedEx Shares Tumble 13% After Profit Miss • IH Market News • 09/20/2024 10:02:58 AM
- AIG names new CFO; Progyny Drops 24% After Losing Key 2025 Contract; Exicure Jumps 190% With Nasdaq Extension • IH Market News • 09/19/2024 10:26:48 AM
- Microsoft Boosts Share Buyback, Raises Dividends by 10%, Intel Secures Chip Deal with Amazon • IH Market News • 09/17/2024 10:40:35 AM
- Form 4 - Statement of changes in beneficial ownership of securities • Edgar (US Regulatory) • 09/10/2024 12:02:19 AM
- Dell, Palantir, and Erie Will Be Added to the S&P 500; Boeing Avoids Strike; Apple Event Takes Place Today • IH Market News • 09/09/2024 10:05:35 AM
- Broadcom Down 10% Post-Earnings, UiPath Up 8%; Qualcomm Eyes Intel Assets; Salesforce Acquires Own Company • IH Market News • 09/06/2024 11:59:00 AM
- Travala Now Available on Skyscanner, Siemens Issues New Digital Bond on Blockchain, Bitcoin Volatility on Thursday • IH Market News • 09/05/2024 06:09:29 PM
- Qualcomm Develops Mixed Reality Glasses; Verizon to Boost Dividend, Eyes Acquisition; Samsonite Plans US Dual Listing • IH Market News • 09/05/2024 10:11:35 AM
- Nvidia Subpoenaed by DOJ, Athira Pharma Shares Plunge 71% After Study Fails, Zscaler Falls 15% Post-Earnings • IH Market News • 09/04/2024 09:50:25 AM
- Intuitive Machines Soars 18% on NASA Contract, Intel Considers Splitting Operations, Dell Reassesses Selling SecureWorks • IH Market News • 08/30/2024 10:00:08 AM
- Big Lots Falls 27%, Considers Bankruptcy; DraftKings Acquires Simplebet, Berkshire Hits $1 Trillion • IH Market News • 08/29/2024 10:06:50 AM
- High Volatility Expected in Nvidia Report, Ambarella Soars 20%, Hertz Strengthens Board, Apple Cuts Jobs • IH Market News • 08/28/2024 09:50:36 AM
- Apple Names New CFO, Sony Hikes PS5 Price in Japan, Santander Launches Share Buyback • IH Market News • 08/27/2024 09:35:22 AM
- Cruise and Uber Join Forces for Robotaxis, Alibaba Shifts Primary Listing to Hong Kong, Altria Hikes Dividend 4.1% • IH Market News • 08/23/2024 12:20:26 PM
- Schwab and Snowflake Retreat in Premarket, WeRide Postpones IPO, Halliburton Cyberattack, McDonald’s Instagram Hack • IH Market News • 08/22/2024 09:37:42 AM
- Walmart Sells JD.com Stake, Microchip Suffers Cyberattack, Union Pacific Warns of Strike in Canada, and Latest News • IH Market News • 08/21/2024 12:12:11 PM
- Berkshire Reduces Stake in BofA, Hawaiian Airlines Soars 10%, Paramount Receives $4.3B Offer, and More • IH Market News • 08/20/2024 09:56:02 AM
- FuboTV Soars 12% After Venu Sports Block, Goldman Sachs Lowers U.S. Recession Odds, BHP Ends Chile Strike • IH Market News • 08/19/2024 09:28:19 AM
- Deutsche Bank Faces Shareholder Backlash, Bank of America Sponsors 2026 World Cup, Quanterix CEO Buys More Shares • IH Market News • 08/16/2024 10:03:21 AM
- Google Mandated to Modify Play Store, Apple Innovates, Victoria’s Secret Hires CEO, Mars Buys Kellanova • IH Market News • 08/15/2024 10:05:46 AM
- Google Forced to Modify Play Store, Apple Innovates, Victoria’s Secret Hires CEO, Mars Buys Kellanova • IH Market News • 08/15/2024 10:05:46 AM
- UBS Beats Earnings Forecasts, Intel Divests Arm Holdings, Flutter Surges 9% in Premarket Trading, and More • IH Market News • 08/14/2024 09:56:35 AM
- Dell Stock Slide Offers Opportunities; Trump and Musk hold talks on X; GM Restructures China Operations, and More • IH Market News • 08/13/2024 09:43:49 AM
VHAI - Vocodia Partners with Leading Political Super PACs to Revolutionize Fundraising Efforts • VHAI • Sep 19, 2024 11:48 AM
Dear Cashmere Group Holding Co. AKA Swifty Global Signs Binding Letter of Intent to be Acquired by Signing Day Sports • DRCR • Sep 19, 2024 10:26 AM
HealthLynked Launches Virtual Urgent Care Through Partnership with Lyric Health. • HLYK • Sep 19, 2024 8:00 AM
Element79 Gold Corp. Appoints Kevin Arias as Advisor to the Board of Directors, Strengthening Strategic Leadership • ELMGF • Sep 18, 2024 10:29 AM
Mawson Finland Limited Further Expands the Known Mineralized Zones at Rajapalot: Palokas step-out drills 7 metres @ 9.1 g/t gold & 706 ppm cobalt • MFL • Sep 17, 2024 9:02 AM
PickleJar Announces Integration With OptCulture to Deliver Holistic Fan Experiences at Venue Point of Sale • PKLE • Sep 17, 2024 8:00 AM