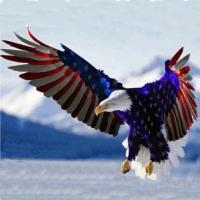
Tuesday, May 26, 2015 1:59:28 PM
It's interesting to me that the CEO dogged the quality issues of the former mfgr. but can't stake a claim to quality for a part to functional design....
.....as compared to a part that has to be designed right (to go with the technology) according to the CEO. If he were talking about the molds it might be one thing, but he refers to the "part design."
So, what I am hearing you say is this:
1) To replace existing parts in the marketplace which are made from different technologies, these parts must be re-designed in order to not only accommodate the function and design of the existing part, but to accomodate the manufacturing methodology required by the liquidmetal injection molding process. Without the re-design, the liquidmetal process will not be able to make the existing part.
This is very true. Further, the redesign of the part must also include, of course, interfacing with the other parts to which it is associated, which might involve re-engineering the other parts to accomodate the LQMT process.
This is precisely why LQMT started out manufacturing the knife, as there was no re-design involved. All of the parts are made, obviously, according to the liquidmetal process, from SQUARE ONE, and were ORIGINALLY designed to accomodate the interfunctionality of every other part.
So, you see, this design is relatively easy, because it does not intefere with other pre-existing parts made from other technologies (other than the metal clip, which is immaterial to our discussion...since it also was designed originally.
2) So from a pure engineering viewpoint, unless you are starting out from SQUARE ONE with a new product with a design already made to accomodate the parts mfr of the liquidmetal IM process, making a part to replace an existing technology is not as simple as one thinks, in that one unique lqmt part will create an engineering disruption for all of the other parts which interface with the lqmt part because, for various and sundry other reasons, (size limitations, material limitations, functional limitations) those parts, too, may have to be redesigned (though not in every case, but some cases) to accommodate the lqmt part.
3) So, the reality may be, that all or some of the other parts which may have to be made by other materials or technologies, but which must be interfaced with the LQMT part, will still require CNC and all the finishing equipment to produce the WHOLE ASSEMBLY which includes a lqmt part.
This means that there is no net capital investment savings, but rather a capital investment INCREASE for the new technology rather than a net decrease, for most IN HOUSE MANUFACTURERS, one market which LQMT is still pursuing. The same could be said of a contract manufacturer.
So, this forced lqmt to go back to where the company already was, essentially, a fully integrated manufacturer.
This flopping around for 5 years with the business strategy is what has unnerved most of the investors on this board. It's like, why wasn't this all anticipated by people with sound planning who knew what they were doing?
This is why, while I certainly can put my faith in a machine produced by Engel, and I certainly can put my faith in a material made by Materion (made to spec, reliably so), I certainly cannot put my trust in the management which has brought us to this point, and has retained all of the dead wood from the management which brought liquidmetal to the point of virtual extinction in 2007 thru 2009.
Now, that being said, if LQMT can design a rocker arm for combustion engines requiring such which will not required redesigning the whole engine, then I will be convinced...
IAW, supplanting existing technologies in the market place will be the proof of the technology.
Recent LQMT News
- Form 10-Q - Quarterly report [Sections 13 or 15(d)] • Edgar (US Regulatory) • 05/20/2024 08:11:00 PM
- Form NT 10-Q - Notification of inability to timely file Form 10-Q or 10-QSB • Edgar (US Regulatory) • 05/15/2024 08:49:57 PM
- Form 8-K - Current report • Edgar (US Regulatory) • 05/09/2024 09:05:11 PM
- Form 4 - Statement of changes in beneficial ownership of securities • Edgar (US Regulatory) • 11/21/2023 10:15:45 PM
- Form 4 - Statement of changes in beneficial ownership of securities • Edgar (US Regulatory) • 08/21/2023 10:26:27 PM
- Form 10-Q - Quarterly report [Sections 13 or 15(d)] • Edgar (US Regulatory) • 08/10/2023 08:37:18 PM
Glidelogic Corp. Becomes TikTok Shop Partner, Opening a New Chapter in E-commerce Services • GDLG • Jul 5, 2024 7:09 AM
Freedom Holdings Corporate Update; Announces Management Has Signed Letter of Intent • FHLD • Jul 3, 2024 9:00 AM
EWRC's 21 Moves Gaming Studios Moves to SONY Pictures Studios and Green Lights Development of a Third Upcoming Game • EWRC • Jul 2, 2024 8:00 AM
BNCM and DELEX Healthcare Group Announce Strategic Merger to Drive Expansion and Growth • BNCM • Jul 2, 2024 7:19 AM
NUBURU Announces Upcoming TV Interview Featuring CEO Brian Knaley on Fox Business, Bloomberg TV, and Newsmax TV as Sponsored Programming • BURU • Jul 1, 2024 1:57 PM
Mass Megawatts Announces $220,500 Debt Cancellation Agreement to Improve Financing and Sales of a New Product to be Announced on July 11 • MMMW • Jun 28, 2024 7:30 AM