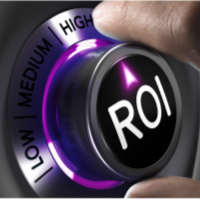
Thursday, May 22, 2008 9:46:31 AM
Operating Plan and Oil and Gas Properties
During June 2007, district managers met with the Company’s operations manager and field supervisor to develop a plan to restore production on various wells. Four fields were identified for potential improvements with a relatively small capital requirement and an acceptable return on investment. Management determined to set aside funds from a tax refund that was received in June 2007, totaling approximately $500,000 for the completion of recommended work in Texas and $300,000 for the completion of recommended work in Wyoming.
Talco/Trix-Liz – It was determined that approximately $90,000 could be spent on sixteen wells resulting in a potential increase in revenue of approximately $195,000 per month. The work includes the perforation and completion of three wells. Two were completed resulting in increased production of approximately 18 bbls per day. The Company determined that gas lock-proof packers were needed on six wells. Packers were purchased and installed on two wells, but the work was unsuccessful because the tubing in these wells is old and the condition of the tubing damages the pliable material of which the packers are made. The additional cost to rework these wells to restore production is estimated at approximately $30,000 per well. Production needs to be restored in legally permitted zones on five wells and production needs to be established from a deeper zone on one well. Tank maintenance on one well was completed, but the well is producing water. Due to electrical problems the well has not been able to produce consistently. The Company is resolving the electrical issues in order to establish consistent production and determine if the water production will decline and the well will produce oil. Due to these issues, the Company has determined that the monthly increase in revenues is more likely approximately $100,000.
Redwater – The Redwater Field poses substantial safety risks due to the hazardous noxious chemical content in the oil and gas. Safety is the highest priority and safety equipment must be maintained and replaced regularly. Approximately $11,000 was spent in the third quarter of 2007 to replace fresh air packs, escape packs and personal monitors. Additionally, approximately $170,000 of repairs on eight wells were identified which could potentially increase revenue by approximately $275,000 per month. Work on five of the eight wells was prioritized for completion, subject to availability of capital at an approximate cost of $100,000 with a one month return on investment. Wireline work on two wells and hot oiling the flow line was attempted but the result was too much water containing H2S. In order to resolve this problem additional work to drain the water below the perforations will be necessary at a cost of approximately $30,000 per well. Additional tanks are needed for one well.
Additionally, water disposal needs to be addressed on one well and a wireline cleanout and chemicals are needed for a water injection well. Two of the remaining three wells need gas lift systems and the third will require a workover to re-establish production. Due to higher costs to complete this work, management wants to evaluate the potential return on investment more thoroughly on these three wells, before proceeding.
Sulphur Bluff – Six wells were identified for work costing approximately $25,000. Hot oil treatment has been completed on two wells as well as the workover of one additional well. The Company still needs to workover two wells and the purchase a packer on one. Rods and tubing and a pump need to be pulled on the final two wells. Upon the completion of the hot oil treatment and workover, a disposal well went down which limited the production available. Repairs on the disposal well are estimated to cost an additional $20,000. The field is currently producing approximately 18 to 20 bbls per day. Once the disposal well is repaired, the production should increase to approximately 100 bbls per day. The timing of repairs on the disposal well is dependent upon availability of capital. The Company believes the Sulphur Bluff property can become a significant source of revenue after this work is performed.
13
--------------------------------------------------------------------------------
Table of Contents
Como – Management prioritized nine wells in the Como Fields for repairs and workovers totaling approximately $66,000. Two of three pumping units and an electric motor have been repaired. One additional pumping unit still requires maintenance. A rod job was completed on one well but new rods or rod jobs are needed on two additional wells and one well requires the replacement of a tail bearing. Coated tubing on an additional well was completed. Since this work was completed production has increased an average of 50 bbls per day to approximately 200 bbls per day. However, as work has been completed additional areas have been identified that requires additional capital beyond the ability of the Company at this time. Energytec has entered into a non-binding letter of intent with an unrelated third party to serve as the basis for selling its interest in the Como oil field as described under Property Divestitures below.
Wyoming – In July 2007, Energytec paid $76,778 for lease rentals on 39,030 acres in Wyoming. The Company set aside $125,000 to plug back, re-perforate, and recomplete the Cinnamon Bear 2-4 utilizing a surfactant and new technology known as sonication. The chemical has been successfully tested at the Rocky Mounting Oil Field Testing Center in Wyoming. The sonic treatment concept is to apply high intensity sound waves to help dissolve and break-up scale that forms at the perforations or the sand face, as well as reduce viscosity, and thereby improve fluid flow. Sonication has successfully been used in heavy oil production in California. Management believes that the combination of sonication and surfactant will result in a greater potential for non-thermally induced production. In addition, the Company has engaged a regulatory consultant to unitize certain of its private and federal leases. Management believes that unitization of some of the federal leases will result in obtaining a two year extension of certain leases otherwise due to expire July 31, 2008.
In June 2007, the Company also agreed to plug the Cole Federal in compliance with an order issued by the Bureau of Land Management (BLM.) Further, the Company is obligated to remediate the site to the satisfaction of the BLM. Remediation work was concluded by the end of August 2007 in compliance with the plugging order.
However, in light of the new operational plan for additional work on the Cinnamon Bear 2-4, the Company has retained the right to reenter the Cole Federal at a later date. The Company expended $50,000 in July 2007 to accomplish the plugging operations. As a result of compliance with the BLM’s plugging order, the Company has the right to receive up to $77,000 in refunds of cash bonds established for the reclamation. During the three months ended September 30, 2007, the Company identified and recognized impairment charges to earnings of $1,191,558, relating the Cole Federal
During June 2007, district managers met with the Company’s operations manager and field supervisor to develop a plan to restore production on various wells. Four fields were identified for potential improvements with a relatively small capital requirement and an acceptable return on investment. Management determined to set aside funds from a tax refund that was received in June 2007, totaling approximately $500,000 for the completion of recommended work in Texas and $300,000 for the completion of recommended work in Wyoming.
Talco/Trix-Liz – It was determined that approximately $90,000 could be spent on sixteen wells resulting in a potential increase in revenue of approximately $195,000 per month. The work includes the perforation and completion of three wells. Two were completed resulting in increased production of approximately 18 bbls per day. The Company determined that gas lock-proof packers were needed on six wells. Packers were purchased and installed on two wells, but the work was unsuccessful because the tubing in these wells is old and the condition of the tubing damages the pliable material of which the packers are made. The additional cost to rework these wells to restore production is estimated at approximately $30,000 per well. Production needs to be restored in legally permitted zones on five wells and production needs to be established from a deeper zone on one well. Tank maintenance on one well was completed, but the well is producing water. Due to electrical problems the well has not been able to produce consistently. The Company is resolving the electrical issues in order to establish consistent production and determine if the water production will decline and the well will produce oil. Due to these issues, the Company has determined that the monthly increase in revenues is more likely approximately $100,000.
Redwater – The Redwater Field poses substantial safety risks due to the hazardous noxious chemical content in the oil and gas. Safety is the highest priority and safety equipment must be maintained and replaced regularly. Approximately $11,000 was spent in the third quarter of 2007 to replace fresh air packs, escape packs and personal monitors. Additionally, approximately $170,000 of repairs on eight wells were identified which could potentially increase revenue by approximately $275,000 per month. Work on five of the eight wells was prioritized for completion, subject to availability of capital at an approximate cost of $100,000 with a one month return on investment. Wireline work on two wells and hot oiling the flow line was attempted but the result was too much water containing H2S. In order to resolve this problem additional work to drain the water below the perforations will be necessary at a cost of approximately $30,000 per well. Additional tanks are needed for one well.
Additionally, water disposal needs to be addressed on one well and a wireline cleanout and chemicals are needed for a water injection well. Two of the remaining three wells need gas lift systems and the third will require a workover to re-establish production. Due to higher costs to complete this work, management wants to evaluate the potential return on investment more thoroughly on these three wells, before proceeding.
Sulphur Bluff – Six wells were identified for work costing approximately $25,000. Hot oil treatment has been completed on two wells as well as the workover of one additional well. The Company still needs to workover two wells and the purchase a packer on one. Rods and tubing and a pump need to be pulled on the final two wells. Upon the completion of the hot oil treatment and workover, a disposal well went down which limited the production available. Repairs on the disposal well are estimated to cost an additional $20,000. The field is currently producing approximately 18 to 20 bbls per day. Once the disposal well is repaired, the production should increase to approximately 100 bbls per day. The timing of repairs on the disposal well is dependent upon availability of capital. The Company believes the Sulphur Bluff property can become a significant source of revenue after this work is performed.
13
--------------------------------------------------------------------------------
Table of Contents
Como – Management prioritized nine wells in the Como Fields for repairs and workovers totaling approximately $66,000. Two of three pumping units and an electric motor have been repaired. One additional pumping unit still requires maintenance. A rod job was completed on one well but new rods or rod jobs are needed on two additional wells and one well requires the replacement of a tail bearing. Coated tubing on an additional well was completed. Since this work was completed production has increased an average of 50 bbls per day to approximately 200 bbls per day. However, as work has been completed additional areas have been identified that requires additional capital beyond the ability of the Company at this time. Energytec has entered into a non-binding letter of intent with an unrelated third party to serve as the basis for selling its interest in the Como oil field as described under Property Divestitures below.
Wyoming – In July 2007, Energytec paid $76,778 for lease rentals on 39,030 acres in Wyoming. The Company set aside $125,000 to plug back, re-perforate, and recomplete the Cinnamon Bear 2-4 utilizing a surfactant and new technology known as sonication. The chemical has been successfully tested at the Rocky Mounting Oil Field Testing Center in Wyoming. The sonic treatment concept is to apply high intensity sound waves to help dissolve and break-up scale that forms at the perforations or the sand face, as well as reduce viscosity, and thereby improve fluid flow. Sonication has successfully been used in heavy oil production in California. Management believes that the combination of sonication and surfactant will result in a greater potential for non-thermally induced production. In addition, the Company has engaged a regulatory consultant to unitize certain of its private and federal leases. Management believes that unitization of some of the federal leases will result in obtaining a two year extension of certain leases otherwise due to expire July 31, 2008.
In June 2007, the Company also agreed to plug the Cole Federal in compliance with an order issued by the Bureau of Land Management (BLM.) Further, the Company is obligated to remediate the site to the satisfaction of the BLM. Remediation work was concluded by the end of August 2007 in compliance with the plugging order.
However, in light of the new operational plan for additional work on the Cinnamon Bear 2-4, the Company has retained the right to reenter the Cole Federal at a later date. The Company expended $50,000 in July 2007 to accomplish the plugging operations. As a result of compliance with the BLM’s plugging order, the Company has the right to receive up to $77,000 in refunds of cash bonds established for the reclamation. During the three months ended September 30, 2007, the Company identified and recognized impairment charges to earnings of $1,191,558, relating the Cole Federal
Join the InvestorsHub Community
Register for free to join our community of investors and share your ideas. You will also get access to streaming quotes, interactive charts, trades, portfolio, live options flow and more tools.