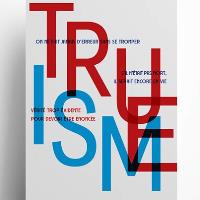
Wednesday, April 06, 2022 6:35:46 AM
03/16/22

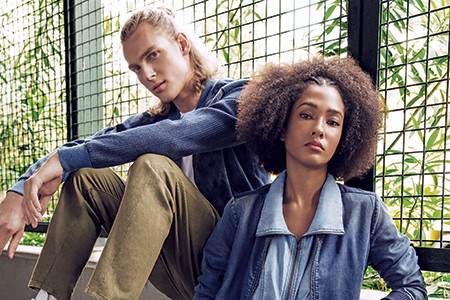
Processing cotton waste to reprieve its cellulose content is one of the more advanced chemical recycling processes in development. The companies in this field are optimising their technologies and securing feedstock to keep operations going as they begin to scale up.
Of all the waste that the apparel industry generates, cotton waste could be considered one of the more valuable resources to keep out of landfills and incinerators. Demand is high for cotton-rich fabric scraps, deadstock, unsold goods and whatever post-consumer clothes and other materials can be culled from the mounting piles of discarded household textiles. These can be shredded and mechanically recycled into new cotton fibres, or they can be liquified into pulp to make regenerated cellulose fibres, such as viscose or lyocell.
While mechanical recycling tends to break down cotton fibres, the process of regenerating cellulose creates a new fibre whose properties are akin to ‘virgin’, manmade cellulosic materials. As the companies investing in these technologies begin to scale up, industrial volumes of the regenerated materials are becoming available.
A telling sign of a promising future for this new crop of fibres is the launch by Levi’s of its Original 501s in a blend of organic cotton and Circulose, a regenerated cellulose fibre made from cotton pulp by start-up Renewcell. This marks a true breakthrough for the Swedish company, as “it is truly an iconic product,” says Nora Eslander, Renewcell’s head of communications. With this symbolic achievement, it hopes to convince other major brands to envision replacing cotton, or polyester for that matter, with its circular regenerated cellulose solution.
Renewcell, which was set up in 2012, is far from the only company in this emerging field of textile-to-textile recycling. Austrian manmade cellulose fibre producer Lenzing launched Tencel x Refibra fibres made from textile waste in 2017. Infinited Fiber Company was established in 2018 when it retrieved a carbamate cellulose regeneration process originally developed by VTT, the Technical Research Institute of Finland.
Evrnu, founded in 2014 in Seattle, is yet another company developing a similar technology. It recently raised $15 million to meet surging demand for its fibre regeneration platform called NuCycl. The company says it will use these funds to expand its operations in South Carolina.
New facilities in the works
In Sundsvall, in the north of Sweden, Renewcell is in the final stages of setting up an industrial scale plant in a former paper pulp processing mill that closed in 2020. It will bring both the building and the onsite water treatment plant back into use. “The infrastructure is there; we do not need to build a new factory and we have hired staff, experienced workers, who were laid off when the paper mill closed,” says Ms Eslander.
In another eco-responsible move, it has acquired a second-hand drying line. This should allow the company to scale up in a relatively short two-year period. Its existing facility, located in a former Akzo-Nobel factory in Kristinehamn, Sweden, produces up to 4,000 tonnes of Circulose pulp per year. The new plant will have a total capacity of 60,000 tonnes and will begin operations this spring, according to the company.
Because no start-up is an island, Renewcell has also formed partnerships with traditional manmade cellulose producers to transform its Circulose pulp into fibre. “Sanyou in China is our biggest partner; it processes two-thirds of our production, representing 40,000 tonnes,” says Ms Eslander. It has also signed a letter of intent with German viscose maker Kelheim.
Production of Circulose has not yet begun at Kelheim, as Dr Marina Crnoja-Cosic, business development director tells WSA. “We are in the phase of technical feasibility and optimisation of production,” she explains. Kelheim could be one of the first Europe-based companies to turn post-consumer waste into new fibres when operations begin. Lenzing’s Tencel x Refibra fibres can include post-consumer waste, but its main feedstock is post-industrial cotton.
Chinese viscose manufacturer Yibin has recently achieved a breakthrough of its own by producing a recycled viscose filament made from 100% Circulose. Renewcell’s partners most often blend 30% to 50% Circulose with conventional wood pulp. “It is not a technical issue, but a matter of volumes, as we have not been able to supply the quantities our partners need,” says Ms Eslander.
Infinited Fiber Company is also in the process of building a large-scale facility. It currently produces its regenerated Infinna-branded fibre from post-consumer textile waste at two pilot facilities, located in two different cities in Finland. “This allows us to produce enough fibre to send sample batches and small commercial batches to our customers, and we are finetuning the processes at our pilots so that we can boost output this year and next.
Unfortunately, even with this additional production, we can’t serve everyone,” says Kirsi Terho, Infinited Fiber Company key account director. The new plant will begin operations in 2024 and will have a capacity of 30,000 tonnes per year. The company has a short-list of possible locations, and plans to finalise its decision in the first quarter of 2022.
The Finnish company also intends to license its technology. “We are first and foremost a technology company, and licensing our technology is a key part of our strategy,” says Ms Terho. This will enable other fibre producers, such as existing viscose manufacturers, to add Infinna to their product portfolios.
“We want Infinna to become a mainstream material as quickly as possible so that it can really make a positive global impact by reducing textile waste and the burden on virgin resources from creating new textile fibres. We can’t do this on our own,” she adds.
In its main plant based in Mörrum, Sweden, Södra, a cooperative wood pulp producer, has been developing a textile waste recycling process since 2019, to make a regenerated cellulose fibre it calls OnceMore. Initial research goes back to 2016, with the first lab tests beginning in 2018, says Angeline Elfström, OnceMore’s business development manager.
The cooperative structure, with its 52,000 members, may be slower to develop new processes compared to single-focused start-ups, but it has the advantage of an operational mill running 24/7. “We are a small team at OnceMore, but we are backed by a very large organisation,” she says. In its first iterations, OnceMore contained only 3% textile waste, but it now incorporates 20% certified recycled content. “Our target is to reach 50%, and we are moving forward progressively as we want to maintain the same attributes. The material needs to align with industry expectations,” she says. Production capacity is growing steadily, and has increased tenfold since summer 2021 to reach 6,000 tonnes, she says.
A well-established wood pulp producer, Södra is a long-standing supplier to “all major manmade cellulosic fibre manufacturers. We are seeing a lot of interest for alternatives to cotton; we feel a real market pull,” says Ms Elfström. Södra and Lenzing came to an agreement last June to work together to increase the use of post-consumer textile waste in their processes. The cooperation involves the transfer of knowledge between the two companies with the goal to recycle 25,000 tonnes of textile waste per year by 2025.
Lenzing has been steadily increasing the proportion of recycled content in its Tencel x Refibra fibres, going from 20% to 30%, with plans to reach 40% in 2023, and 50% by 2025. The cooperation with Södra will enable Lenzing to broaden the range of suitable materials used to make Tencel x Refibra fibres. “We can currently add white cotton or polyester to our sources of raw material with a further increase of the raw material base to come,” says Caroline Ledl, head of product management at Lenzing.
Expanding waste resources
Most of the cotton-to-cellulose pulp makers can only process waste materials, whether pre- or post-consumer, that have a high proportion of cotton, ideally as close to 100% as possible. Södra is an exception as its technology separates cotton from cotton-polyester blends. “The polyester is incinerated and used to power the process,” says Ms Elfström.
Until recently Södra’s process could only accept white or light-coloured waste that it retrieved from hotels, restaurants and laundries serving the hospitality industry. It has partnered with hotels in the UK through the Textile Services Association (TSA), a trade association for the textile care services industry. “We need volumes, not just 100 kg here and another 100 kg there,” says Ms Elfström. “If we were to use household waste, we would need a partner that collects and sorts it, like paper.”
Södra has recently begun to accept coloured textile waste, and announced a collaboration with Swedish grocery retailer ICA to recycle its used workwear, which uses black and green fabric. Instead of being incinerated, 56,000 garments will be the raw material for as many as 28,000 new ones. “This is the first time that coloured workwear from blended polycotton materials will be recycled and used for new textile fibres on a commercial scale in Sweden, and possibly the world,” says Ms Elfström.
Renewcell is seeking to lower the threshold of suitable feedstock to 90% cotton content, which would allow it to accommodate the presence of elastane. It has formed partnerships with used garment collectors, including Bank and Vogue, one of its largest suppliers, and says it has secured 50,000 tonnes of used clothing annually.
Meanwhile, Lenzing says it is working with customers and partners to develop customer-specific take-back systems. Infinited Fiber Company is working with suppliers in Finland and abroad to secure its supply of textile waste. It recently announced an agreement with Lounais-Suomen Jätehuolto (LSJH), a Finnish municipal waste collection company, which, says Ms Terho, is currently building a processing plant for discarded textiles.
All are counting on the implementation, within the countries of the European Union, of a separate collection of used household textiles by 2025 at the latest as part of the EU’s Green Deal. In Finland, legislation has already been passed and separate collection of household textile waste will begin in 2023. The EU lets each country decide how to manage this waste, whether it is the responsibility of municipalities or specially formed organisations.
In France, Refashion (formerly known as Eco-TLC) levies a tax on all companies that sell apparel, footwear or home linens in the country. These funds are used to increase waste collection and its recycling. In 2020, the latest figures available, it collected 204,000 tonnes of used goods and received €34.5 million in ‘eco-fees’. Part of these funds are used to finance research into recycling processes. Refashion has distributed €5 million to some 55 projects since its inception 11 years ago.
Further research
Amsterdam-based sustainability organisation Fashion For Good launched a new research programme known as The New Cotton Project in October 2020. It has rounded up a consortium of 12 companies, from all stages of the recycling supply chain, and focuses exclusively on post-consumer textile waste.
The project is making good progress, says Paula Sarsama, New Cotton Project coordinator and Infinited Fiber Company product manager. Dutch used clothing collector Frankenhuis and REvolve waste, which tracks waste materials, have mapped the textile waste flows within the EU, and have evaluated available textile streams to identify which are best suited to Infinited Fiber Company’s process. Xamk, the South-Eastern Finland University of Applied Sciences, has refined the pre-treatment process. Spinning partners, Turkey-based Kipas, Slovenia-based Tekstina and Portugal-based Inovafil, have made yarns from regenerated Infinna fibres.
These, she says, have been made into fabrics for quality review and dyeing and printing tests. Brand partners adidas and H&M have meanwhile finalised designs, conducted consumer research, and run fabric tests to compare the qualities of Infinna to virgin cotton. The positive results from these tests now enable the consortium to move on to the next step, which is to carry out the process on a larger scale. If all goes as planned, adidas and H&M will be presenting finished products made from regenerated Infinna fibre by the end of the project in 2023.
By that time, Renewcell’s Circulose and Lenzing’s Tencel x Refibra fibres will no doubt be available in greater quantities and partnerships with brands and retailers will bring these novel, regenerated cellulose fibres to market. The prospect for this type of chemical recycling is positive, though narrow, as it requires cotton-rich waste materials.
It also remains to be seen whether these lyocell or viscose fibres can themselves be recycled. Research is under way here, but remains at lab-scale. Extracting cellulose from used cotton clothing has proved its potential; it is time to identify and optimise cost-efficient methods of extracting cotton-rich items from the mountains of used textiles that are discarded every day across the world.
Lenzing’s Tencel x Refibra fibre is now a part of the company’s carbon-zero platform. Tencel x Refibra fibres have a carbon footprint of 2.5 CO2e/kg (cradle to gate), and refers to the fibre itself, not to the recycling technology. This data will be added to the Higg MSI, the company says.
Credit: Lenzing
KBLB is blending with cotton.
TE
I've never claimed to have all the answers but feel i'm beginning to corner the market in questions worthy of them.
Recent KBLB News
- Form 424B3 - Prospectus [Rule 424(b)(3)] • Edgar (US Regulatory) • 06/10/2024 08:30:30 PM
- Form EFFECT - Notice of Effectiveness • Edgar (US Regulatory) • 06/04/2024 04:15:03 AM
- Form S-1/A - General form for registration of securities under the Securities Act of 1933: [Amend] • Edgar (US Regulatory) • 11/22/2023 09:31:54 PM
- Form 424B3 - Prospectus [Rule 424(b)(3)] • Edgar (US Regulatory) • 11/16/2023 09:30:34 PM
- Form 10-Q - Quarterly report [Sections 13 or 15(d)] • Edgar (US Regulatory) • 11/13/2023 09:43:51 PM
- Form 424B3 - Prospectus [Rule 424(b)(3)] • Edgar (US Regulatory) • 09/11/2023 08:30:50 PM
- Form POS AM - Post-Effective amendments for registration statement • Edgar (US Regulatory) • 09/01/2023 08:30:52 PM
- Form 10-Q - Quarterly report [Sections 13 or 15(d)] • Edgar (US Regulatory) • 08/14/2023 08:35:05 PM
Bantec's Howco Short Term Department of Defense Contract Wins Will Exceed $1,100,000 for the current Quarter • BANT • Jun 25, 2024 10:00 AM
ECGI Holdings Targets $9.7 Billion Equestrian Apparel Market with Allon Brand Launch • ECGI • Jun 25, 2024 8:36 AM
Avant Technologies Addresses Progress on AI Supercomputer-Driven Data Centers • AVAI • Jun 25, 2024 8:00 AM
Green Leaf Innovations, Inc. Expands International Presence with New Partnership in Dubai • GRLF • Jun 24, 2024 8:30 AM
Bemax Inc. Positions to Capitalize on Industry Growth with New Improved Quality of Mother's Touch® Disposable Diapers • BMXC • Jun 24, 2024 8:00 AM
Last Shot Hydration Drink Announced as Official Sponsor of Red River Athletic Conference • EQLB • Jun 20, 2024 2:38 PM