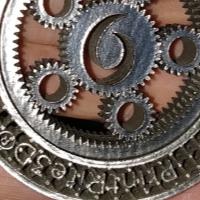
Wednesday, February 03, 2021 1:50:25 AM
This study with DARPA was an ongoing project completed and run by various stringently operated government agencies.
These studies are completed by the highest level of scientists in the country, and adhere to very strict standards and scientific processes.
An objective third party made very clear observations about the ability for Sigma Labs technology to certify and verify the parts and processes associated with an AM print.
That being said, it could be easily deduced that in the future, as these government agencies make AM an ongoing operation and standard procedure, the government entities would more than likely reference this study when determining what type of technology should be used in the AM processes for the DoD, DoE, and all government run agencies.
Similar to the impact on the valuation of Tesla when the government promised to use Electric Vehicles, or EV, very recently, a similar impact could be felt if the government decides to use Sigma Labs technology or one like Printrite3D to qualify government run AM printers and printers and parts made for the government.
considering this study proves the technology is capable of certifying not only parts, but the AM process, this could easily happen for a company like Sigma Labs and Printrite3D technologies.
This requirement could lead private end users to find a software like Printrite3D in order to properly print parts for the government.
A very profitable market that largest companies in the world participate in, government contracts, like Boeing, Airbus, Lockheed Martin, Honeywell, Aerojet Rocketdyne, GE, Woodward, and many others... most of which happen to also hold a contract with Sigma Labs.
Funny,in my opinion, how it takes some 8 frantic posts to try to explain a simple thought, that is then challenged and proven incorrect by about four others who all agree it makes no sense. its fun to see day after day.
it takes one post of facts without speculation and incorrect pps guesses to stand on profitable grounds.
https://sigmalabsinc.com/darpa-study-opt-in/
Summary and Conclusions
Qualification and/or certification is a process through which compliance to a set of requirements is demonstrated.
The purpose of the qualification framework presented is to show that compliance can be demonstrated via numerical simulations
supported by experiments for validation and calibration.
The reason this approach is necessary is lack of experience and design rules for LPBF process.
The qualification platform
was developed to facilitate gaining insight into how the manufacturing process works and hence avoid pitfalls.
The software capabilities to analyze the melting of the powder was used to ensure that the selected process conditions (speed,
power, hatch spacing, and layer thickness) yields very low levels of porosity in the as-build condition.
The distortion capabilities were used to confirm that the component meets
dimensional requirements and furthermore that the build process will not experience any stoppages due to re-coater collisions with the workpiece.
Simulations were also used to evaluate potential hot and cold crack susceptibility of the material
and the component via thermal gradients of the melt pool and the residual stress and strains, respectively.
Experiments are presented which help ascertain the accuracy of the numerical predictions. The porosity predictions were compared to those of specimens built at different conditions.
The porosity was measured via metallographic cross sections as well as Archimedes method. The same trends and values wereobserved as those predicted.
The melt pool temperature and melt
pool size were compared to images gathered via a two-wavelength digital camera.
The melt pool temperature comparison is within a 100 K at temperatures at the boiling point of the metal (~ 3000 K).
The melt pool size, width and length, was more difficult to compare and further work is needed to understand the comparisons.
Sensors were used to develop an IPQM™ that can be used to monitor the quality of the component, with respect to porosity, as it is being built.
A photodetector was used to collect light emitted by the process and the electrical response analyzed and its statistics computed and used to
develop process control limits.
Specimens were built at optimum and off optimum process conditions and process data collected and plotted against the quality metric (TED™), the response of the rocket nozzle was plotted against those of the specimens and showed that the level of porosity of the component is well within the acceptable range and which was also verified experimentally.
This work has demonstrated that a combination of physics based modeling and experimental verification and validation can enable early stage identification and elimination of potential problems.
The build was directly successful and component testing confirmed achievement of the targeted porosity, geometric accuracy, and mechanical strength of the printed material.
***It has shown that the qualification framework presented here can be used as the compliance means for certifications and/or certification of components.***
Authors’ Contributions All authors contributed to the effort described in
this article.
Funding Information
This study is financially supported by the DARPA Open Manufacturing program, USA.
Would love to respond more but currently on the west coast completing a new merger and acquisition contract as part of a due diligence analysis.
Sigma inside
Do DD
Glta.
Sigma Inside
Do DD
Glta
FEATURED Cannabix Technologies and Omega Laboratories Inc. Advance Marijuana Breathalyzer Technology - Dr. Bruce Goldberger to Present at Society of Forensic Toxicologists Conference • Sep 24, 2024 8:50 AM
FEATURED Integrated Ventures, Inc Announces Strategic Partnership For GLP-1 (Semaglutide) Procurement Through MedWell USA, LLC. • Sep 24, 2024 8:45 AM
Avant Technologies Accelerates Creation of AI-Powered Platform to Revolutionize Patient Care • AVAI • Sep 24, 2024 8:00 AM
VHAI - Vocodia Partners with Leading Political Super PACs to Revolutionize Fundraising Efforts • VHAI • Sep 19, 2024 11:48 AM
Dear Cashmere Group Holding Co. AKA Swifty Global Signs Binding Letter of Intent to be Acquired by Signing Day Sports • DRCR • Sep 19, 2024 10:26 AM
HealthLynked Launches Virtual Urgent Care Through Partnership with Lyric Health. • HLYK • Sep 19, 2024 8:00 AM