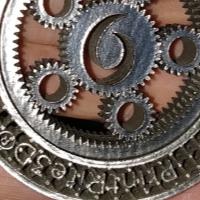
Friday, April 20, 2018 2:54:23 PM
The sensor types comprised non-contact, non-imaging optical sensors as well as non-contact thermal
sensors. One (1) sensor was a photodetector placed in a fixed, or Eulerian frame of reference and
positioned above the build plate. Its field of view (FOV) was of the entire build plate. A second
photodetector was placed in a moving, or Lagrangian frame of reference within the optics train. Its FOV
was restricted to a narrow region immediately surrounding the melt pool. The third sensor was a high-
speed, single wavelength pyrometer with a 6µs response time, placed in a fixed frame of reference above
the build plate and focused onto a 10mm, right circular cylinder (aka, a Process Control Specimen [PCS]).
Its FOV was approximately 1mm. The fourth sensor collected X and Y command signals from the scan
head controller and was used to visualize in-situ dependent data (aka, In-Process Quality Metric™
[IPQM®] data) in a 3D thermal point cloud. All in-situ sensor data was collected by a high-speed data
acquisition system running at 50 kHz per channel (aka PrintRite3D SENSORPAK®) and was
subsequently analyzed by Sigma’s proprietary analytics engine (aka, PrintRite3D INSPECT® software).
Stratonics-
Direct Metal Laser Sintering
Sensor Setup for High Speed Acquisition
ThermaViz melt pool sensor
Fast exposure, freezes melt pool motion
High magnification, resolves melt pool
Field of view/Frame rate
Full window: 1000 x 1000 pixels, 20 x 20 mm, 150 Hz
1D window: 100 x 1000 pixels, 2 x 20 mm, 1500 Hz
2D window: 100 x 100 pixels, 2 x 2 mm, 15,000 Hz
Data (movies) recorded during each layer
Data archived for post analysis
Global heat flow sensor
Fixed exposure,
Frame Rate, 30 Hz
Field of view, entire powder bed
Resolution, 2 pixels/mm
Data recorded throughout deposit
Post Processing
Exports imagery and data in standard formats: .bmp, .emf, .avi, .cvs
Samples regions of interest for data extraction, Hot Spot Tracking
ThermaViz melt pool sensor
Thermal images computed from 2 wavelength calibration
Measures melt pool temperature, size, heating and cooling rates
Global heat flow sensor
Thermal images computed from 1 wavelength calibration
0bserves long term heat flow in deposits and powder bed, (residual stress)
Data extraction
thermal, dimensional and gradient
thermal images, large files, csv
client analysis, Mat Lab
In summary.
Sigma Labs technology is capable of examining the entire build plate and comparing it to proper process parameters and material characteristics of the entire powder bed.
Stratonics focuses entirely on the Melt pool and does not have the capabilities of examining the entire part geometry as a whole in real time. Their hardware and software solution cannot provide a 3D map as Sigma Labs does, to show in real-time the thermal emissions of the Melt pool to show a sample of the build.
Stratonics can show real time emissions from the Melt pool, but does not scan the entire build as Sigma Labs does, including the capabilities to monitor multiple builds simultaneously.
This is where Sigma Labs capabilities to Monitor and qualify both powder and parts separates them from any current inspection technology available.
Sigma labs can show a 3D mapping of the entire build plate, while ensuring the geometric data of each part, thermal emissions of the melt pool, and process parameters of the entire metal AM Machine.
PR3D is the entire solution for IPQM, not just one faction like stratonics.
Recent SASI News
- Form D - Notice of Exempt Offering of Securities • Edgar (US Regulatory) • 03/06/2024 02:09:28 PM
- Form 8-K - Current report • Edgar (US Regulatory) • 02/22/2024 09:20:29 PM
- Form 8-K - Current report • Edgar (US Regulatory) • 02/12/2024 10:11:48 PM
- Form DEFA14A - Additional definitive proxy soliciting materials and Rule 14(a)(12) material • Edgar (US Regulatory) • 02/12/2024 02:01:27 PM
- Form DEF 14A - Other definitive proxy statements • Edgar (US Regulatory) • 02/09/2024 10:30:29 PM
- Form 4 - Statement of changes in beneficial ownership of securities • Edgar (US Regulatory) • 02/05/2024 01:25:51 PM
- Form PRE 14A - Other preliminary proxy statements • Edgar (US Regulatory) • 01/30/2024 11:12:15 PM
- Form 8-K - Current report • Edgar (US Regulatory) • 01/30/2024 09:45:39 PM
- Form 4 - Statement of changes in beneficial ownership of securities • Edgar (US Regulatory) • 01/23/2024 09:15:49 PM
- Form 8-K/A - Current report: [Amend] • Edgar (US Regulatory) • 01/16/2024 09:30:35 PM
- Form 8-K - Current report • Edgar (US Regulatory) • 01/16/2024 01:32:12 PM
- Form 8-K/A - Current report: [Amend] • Edgar (US Regulatory) • 01/10/2024 09:30:17 PM
- Form 8-K - Current report • Edgar (US Regulatory) • 01/09/2024 10:00:16 PM
- Form 4 - Statement of changes in beneficial ownership of securities • Edgar (US Regulatory) • 01/04/2024 01:39:21 AM
- Form 4 - Statement of changes in beneficial ownership of securities • Edgar (US Regulatory) • 01/04/2024 01:38:26 AM
- Form 8-K - Current report • Edgar (US Regulatory) • 01/03/2024 01:30:17 PM
- Form 8-K - Current report • Edgar (US Regulatory) • 01/02/2024 10:20:32 PM
- Form DEFA14A - Additional definitive proxy soliciting materials and Rule 14(a)(12) material • Edgar (US Regulatory) • 12/07/2023 01:35:07 PM
- Sigma Additive Solutions Announces Filing of Definitive Proxy Statement Relating to Proposed Acquisition and Shareholder Vote • Business Wire • 12/07/2023 01:31:00 PM
- Form DEF 14A - Other definitive proxy statements • Edgar (US Regulatory) • 12/01/2023 11:03:17 AM
- Form 8-K - Current report • Edgar (US Regulatory) • 11/24/2023 09:05:37 PM
Avant Technologies Equipping AI-Managed Data Center with High Performance Computing Systems • AVAI • May 10, 2024 8:00 AM
VAYK Discloses Strategic Conversation on Potential Acquisition of $4 Million Home Service Business • VAYK • May 9, 2024 9:00 AM
Bantec's Howco Awarded $4.19 Million Dollar U.S. Department of Defense Contract • BANT • May 8, 2024 10:00 AM
Element79 Gold Corp Successfully Closes Maverick Springs Option Agreement • ELEM • May 8, 2024 9:05 AM
Kona Gold Beverages, Inc. Achieves April Revenues Exceeding $586,000 • KGKG • May 8, 2024 8:30 AM
Epazz plans to spin off Galaxy Batteries Inc. • EPAZ • May 8, 2024 7:05 AM