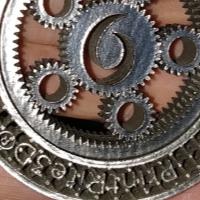
Thursday, April 05, 2018 4:46:27 PM
Also the industry as a whole, is unsure and still doing research and development on how to mass-produce additive manufactured parts while maintaining quality.
This doesn't happen overnight over a month or even a year it takes years of research and development to complete.
A company must be absolutely 100% sure that their process especially over multiple printers will produce Quality Parts.
The few companies that have been working with us for multiple years are just about ready for production and have publicly stated while purchasing are software that it will be utilized for production purposes.
Many of the other companies that are currently producing additive manufactured parts are spending an extraordinary amount of money to inspect those parts post-process.
Once companies become comfortable with the fact they can use an in process Quality Assurance Technology to create a record of each individual print showing compliance to design intent, they will then be able to greatly diminish and or eventually eliminate post-process inspection.
Since this type of in process monitoring data is just being looked at by the standardization and entities such as NIST, it shows that the confidence in this data is growing because the correlation between the data and material characteristics of each individual print is very strong.
This type of software proves that the data captured from monitoring the Melt pool as well as process parameters can sufficiently prove compliance of each individual part.
As we've seen more and more companies start to use our software, and also solidifies our in-process Quality Assurance Technology is a viable solution for mass production of additive manufactured parts.
I believe it is lack of standards, lack of knowledge, and lack of trust in the data extracted from the hardware and software in in process quality Monitoring Solutions.
Now that sufficient testing has been done, years of Department of Defense projects, America makes programs, individual company studies, and so on so forth, Sigma Labs ipqa solution has been proven over and over again.
As our technology has continued to improve over the years, and with the addition of TED, Sigma Labs has proven itself to have a commercialized product capable of the issue of mass production with additive manufacturing processes.
The first to Market I might add.
I think the fact that NIST signed a collaboration with us, is probably the strongest possible signal in the world to prove that our technology is capable of providing significant data to prove the quality of each individual part during a print, while also qualifying the powder and also spent powder, which is a very significant value chain asset in itself.
We are at the very bottom of this hockey stick growth pattern and it certainly seems like the industry is just about ready to spike up significantly in mass production activity.
I don't think all companies will wait for standards, as if they are able to store the data captured from IPQM Technologies that's Supply significant evidence that each part followed process parameters to a compliant build, that should be sufficient evidence in the scenario a part fails, to at least explain that the part was printed correctly, however, conditions out of our control cause the part to fail.
That is the biggest fear of any company in the additive Manufacturing world right now especially with Aerospace, is having an additive manufactured part fail, and not being able to explain why it happened.
That is why with Sigma labs technology, you can prove that each particular part was followed to a working design model that passed every stress test necessary.
If the part fails, but had met all those qualities, it is not additive manufacturing or the companies fault. Just adverse conditions that caused the failure.
Sigma Labs collects, analyzes, and stores that data comparing it to correct builds, to prove validation.
As this is a new idea within any industrial environment to have to use in process quality monitoring softwares to prove a part is correct it is taking a long time for many companies to be understanding and trusting of this type of data.
It's been called industry 4.0 and an industrial revolution for a reason. this process is completely different than anything that's ever been done before in terms of manufacturing.
That is what is causing the industry to slowly adopt additive manufacturing as a whole and especially in process quality monitoring as validation.
However Sigma Labs has been able to do an extremely great job at continuing to improve their software as well as collect data that proves it works.
We now have approximately 7 years of strong data showing that ipqa works thru DoD programs.
Multiple DARPA programs, USAF projects, aerojet Rocketdyne verification, Honeywell verification, 3D Sim verification.
I've been rambling and I am very exhausted so I'm just going to end this message here since nobody probably read this far anyways lol
Glta SGLB
Recent SASI News
- Form D - Notice of Exempt Offering of Securities • Edgar (US Regulatory) • 03/06/2024 02:09:28 PM
- Form 8-K - Current report • Edgar (US Regulatory) • 02/22/2024 09:20:29 PM
- Form 8-K - Current report • Edgar (US Regulatory) • 02/12/2024 10:11:48 PM
- Form DEFA14A - Additional definitive proxy soliciting materials and Rule 14(a)(12) material • Edgar (US Regulatory) • 02/12/2024 02:01:27 PM
- Form DEF 14A - Other definitive proxy statements • Edgar (US Regulatory) • 02/09/2024 10:30:29 PM
- Form 4 - Statement of changes in beneficial ownership of securities • Edgar (US Regulatory) • 02/05/2024 01:25:51 PM
- Form PRE 14A - Other preliminary proxy statements • Edgar (US Regulatory) • 01/30/2024 11:12:15 PM
- Form 8-K - Current report • Edgar (US Regulatory) • 01/30/2024 09:45:39 PM
- Form 4 - Statement of changes in beneficial ownership of securities • Edgar (US Regulatory) • 01/23/2024 09:15:49 PM
- Form 8-K/A - Current report: [Amend] • Edgar (US Regulatory) • 01/16/2024 09:30:35 PM
- Form 8-K - Current report • Edgar (US Regulatory) • 01/16/2024 01:32:12 PM
- Form 8-K/A - Current report: [Amend] • Edgar (US Regulatory) • 01/10/2024 09:30:17 PM
- Form 8-K - Current report • Edgar (US Regulatory) • 01/09/2024 10:00:16 PM
- Form 4 - Statement of changes in beneficial ownership of securities • Edgar (US Regulatory) • 01/04/2024 01:39:21 AM
- Form 4 - Statement of changes in beneficial ownership of securities • Edgar (US Regulatory) • 01/04/2024 01:38:26 AM
- Form 8-K - Current report • Edgar (US Regulatory) • 01/03/2024 01:30:17 PM
- Form 8-K - Current report • Edgar (US Regulatory) • 01/02/2024 10:20:32 PM
- Form DEFA14A - Additional definitive proxy soliciting materials and Rule 14(a)(12) material • Edgar (US Regulatory) • 12/07/2023 01:35:07 PM
- Sigma Additive Solutions Announces Filing of Definitive Proxy Statement Relating to Proposed Acquisition and Shareholder Vote • Business Wire • 12/07/2023 01:31:00 PM
- Form DEF 14A - Other definitive proxy statements • Edgar (US Regulatory) • 12/01/2023 11:03:17 AM
- Form 8-K - Current report • Edgar (US Regulatory) • 11/24/2023 09:05:37 PM
Element79 Gold Corp Appoints Warren Levy to Board of Directors • ELMGF • Aug 28, 2024 9:51 AM
Integrated Ventures Announces Strategic Entry Into Health & Wellness Industry with Focus on GLP-1 Products • INTV • Aug 28, 2024 8:30 AM
ELEMENT79 ANNOUNCES UPLISTING TO OTCQB VENTURE MARKET • ELMGF • Aug 26, 2024 10:03 AM
North Bay Resources Announces Gold Assays up to 2.2 Ounces per Ton, Fran Gold Project, British Columbia • NBRI • Aug 26, 2024 10:00 AM
PickleJar Unveils Latest Venue Managed Services Innovations in Upcoming Webinar • PKLE • Aug 23, 2024 1:11 PM
Element79 Gold Corp Provides Update on Nevada Portfolio • ELMGF • Aug 23, 2024 8:00 AM