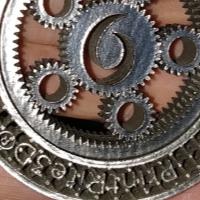
Monday, October 16, 2017 11:12:27 PM
The caliber of the corporations engaged with Sigma Labs’ product line is impressive to say the least, and is a veritable who’s who of the Additive Manufacturing world. In February 2017 Sigma Labs filed SEC form S-1/A showing a snapshot of current business customers, and the lineup of corporations in the sales opportunity pipeline. Whether current, or in negotiations, the list includes:
GE Aviation
EOS
Honeywell Aerospace
Aerojet Rocketdyne
Farinia Group-Spartacus 3D
Woodward
GE Power &Water (Switzerland)
Siemens AG
Safran Group
Pratt & Whitney
Rolls Royce Plc
Sisma (Italy)
Michelin Fives (France)
Aspect (Japan)
Additive Industries NV
Renishaw Plc
SpaceX
Moog Inc/Linear AMS
Edison Welding Institute
Michelin Tire
Honeywell FM&T (Kansas City)
BMW
Blue Origin
Solar Turbines Inc
3D Material Technologies LLC
13D
Polyshape (France)
Layerwise (3D Systems)
These corporations sit at the leading edge of efforts to establish metal 3D printing as a reliable and proven process for manufacturing complex, critical, high-reliability products at production scales. The spectrum of industries for which metal AM is being established is extensive and growing. Experts believe that metal AM will significantly and beneficially impact part design, cycle time to finished products, production costs, material logistics, part functionality and end-use efficiencies in aerospace, military, automotive, oil & gas, power generation, medical and bio-medical industries. Sigma Lab’s unique selling point, due to PrintRite3D’s® real-time, in-process inspection, analysis and certification, is that it offers even greater savings in production, inspection, and time expenditure costs by avoiding slow and excessively costly conventional post-build inspection techniques available from traditional manufacturing. Sensor based, real-time, in-process inspection is the next major step in manufacturing efficiency, and PrintRite3D® looks set to deliver.
Sigma Labs currently has at least 12 PrintRite3D® systems installed within the Aerospace and OEM 3D Printer manufacturing industries. Systems are currently operational at GE Aviation, Honeywell Aerospace, Aerojet Rocketdyne, Farinia Group-Spartacus 3D, Additive Industries, Siemens AG, Pratt & Whitney, Woodward Inc and an undisclosed European OEM.
Significantly, Sigma Labs announced in January 2017 that they have completed a multiyear commercial contract with an undisclosed leading European OEM corporation for which PrintRite3D® will be embedded in the OEM’s AM equipment offerings. The deal was reported to be conservatively valued at $6 Million USD over a 7 year period.
Mark Cola, President and CEO of Sigma Labs stated:
“We are excited to have such a highly regarded company, which cannot be named due to competitive reasons, be an OEM partner going forward. Building strategic relationships with equipment OEMs has always been a key element of Sigma Labs’ growth strategy – enabling our software to be embedded in AM machines as a salient feature from the very beginning. As part of this agreement, our partner will be able to provide the full power of Sigma Labs’ PrintRite3D® capabilities to its customers, ensuring they can maximize the benefits of In-Process Quality Assurance™(IPQA®) during additive manufacturing – which should increase production yields, process reliability, and part quality. The agreement is an important milestone for Sigma Labs as we build alliances to better serve the burgeoning AM industry and bolster our long-term growth trajectory.”
Prior to the February 2017 form S-1/A release, a July 2016 form S-1 release showed the German metal printer manufacturer, Trumpf GmbH, listed as having an active PrintRite3D® Inspect™ module installed for evaluation. With the announcement of the unnamed European OEM printer manufacturer, and the removal of Trumpf GmbH from the February form S-1/A, it may be that Trumpf is the undisclosed OEM, and is now embedding Sigma Labs’ PrintRite3D® into their machines.
Perhaps of equal significance, also in January 2017, Sigma Labs announced that it has signed a commercial contract with aerospace giant Pratt & Whitney (a unit of United Technology Corp). Terms of the deal were not disclosed, but Pratt & Whitney, a competitor of GE Aviation and Honeywell Aerospace, is a major player in the manufacturing of aircraft engines and auxiliary power units. This deal may become the first site in which PrintRite3D® will be employed in a full production environment.
Mark Cola, President and CEO of Sigma Labs:
“I’m very pleased to announce that Pratt &Whitney, the esteemed aerospace and defense manufacturer, is joining our Early Adopter Program. Signing high quality, well-known customers coming on the heels of our contract with Siemens just a few weeks ago clearly demonstrates a growing market for our PrintRite3D® quality assurance software and strong brand recognition for our products.”
As noted above, these recent contracts followed hot on the heels of November’s announcement that AM powerhouse Siemens Industrial Turbo machinery AB of Finspang, Sweden (a unit of Siemens AG) has also adopted PrintRite3D® for evaluation. In February 2017 Siemens announced ‘breakthrough results’ at full power and temperature outputs in their gas turbine AM testing, the department where PrintRite3D® is under evaluation.
Non Disclosure Agreements and/or PrintRite3D® system quotes have been exchanged with the remaining fifteen corporations engaged. Undoubtedly the list will be growing.
The planned build-out of production AM manufacturing in the aerospace industry alone is enormous. GE Aviation made a very large splash in the AM industry toward the end of 2016 with their $1.4 billion dollar announcement that they were purchasing the metal printer machine manufacturers Arcam and Concept Laser. Following these purchases David Joyce, CEO of GE Aviation, suggested internal demand for metal AM machines in GE could reach 1,000 in the next 10 years; a statement backed up by GE Additive VP Mohammad Ehteshami who revealed an additional goal to produce 10,000 machines in the same time frame for global customers.
Other major manufacturers are not standing still. Sigma Labs’ partner Honeywell Aerospace has established metal 3D printing facilities at Phoenix, Arizona, Bangalore, India, Bruno, Czech Republic, Shanghai, China, and most recently the Chihuahua Machining Operations center in Mexico. Within these facilities Honeywell has nearly tripled its capacity for metal 3D printing. Led by Donald Godfrey, the Honeywell AM group, alongside the US military research agency DARPA, are currently in the final 3rd phase of an initiative for establishing Integrated Computational Materials Engineering (ICME) principles. The project may well be the defining work of nailing down the crucial techniques required for metal printer operations and in-process inspection. Already, military agency follow-on projects are incorporating this initiative’s program and explicitly stating that sensor based, in-process inspection and analysis will be a structural part of the program. Sigma Labs’ IPQA® and PrintRite3D® has played a central role in this project from the very beginning.
It is clear the expected growth rate of installed printers for AM in aerospace alone is very large. When you combine the build-out of the additional industries establishing metal AM production, the number of printers that will be requiring the capabilities of Sigma Lab’s PrintRite3D® is staggering.
Mark Cola, CEO of Sigma Labs, has spoken of a ‘push-pull’ effect influencing the adoption of the company’s IPQA® and PrintRite3D® product suite within the metal AM industry. Several industry oversight and standards bodies have programs ongoing to establish best practices and guidance for AM manufacturing. The two leading programs are the America Makes/ANSI project 4027, led by several national entities including GE Aviation, Lockheed Martin, and NASA, and DARPA-ICME initiative mentioned above, led by Honeywell Aerospace. The America Makes project has just released its final draft copy of their standard. The framework for the project explicitly acknowledged that the metal AM industry will likely not be viable from a profitability standpoint if conventional post-build inspection techniques were utilized.
See: AMSC 16-033, Preliminary Final Draft AMSC Roadmap (12/14/16)
In Process Monitoring
AM offers the capability to have significant in process monitoring, and the capability of in process monitoring is expected to grow significantly in the next several years. This will dictate what data should be captured and when this data can be used to give assurances that a part was made to a required specification. Currently, it is not possible to reliably take process monitoring data and convert it into an accurate 3D file representing the part manufactured. However, this technology is growing rapidly. Further, the only way to get the data necessary for the qualification of critical parts is through CT scanning. This process is very expensive and represents a significant barrier to the industry. As long as 100% CT scanning of parts is required, a business case for AM will be difficult to justify.
These programs are serving to push Sigma Lab’s IPQA® and PrintRite3D® into the industry. The regulating and oversight bodies recognize that IPQA® is a crucial component to enabling metal AM manufacturing.
An additional push is starting to come from the metal printer machine manufacturers themselves. As of the end of 2016 there were 25 metal 3D printer manufacturers globally. The AM industry initiatives are currently mainly focused upon Powder Bed Fusion machines. Only 18 of these manufacturers produce Powder Bed Fusion machines. The remaining types of metal printers fall under Binder Jetting, Direct Energy Deposition and Material Jetting formats.
Sigma Labs has PrintRite3D® installations already active with Trumpf gmbH and Additive Industries NV. Renishaw, Sisma and Aspect are already engaged with Sigma Labs’ offerings. Sigma Labs states that they believe “there is potential for our PrintRite3D® software to be incorporated into a majority of 3D metal printing devices made by companies like Electro-Optical Systems (“EOS”), Additive Industries, Concept Lasers, Trumpf Lasers, Renishaw, Sentrol, Farsoon and others.” As it continues to appear that sensor based in-process systems will be utilized by the AM industry, more printer manufacturers will undoubtedly turn to Sigma Labs.
Many of these machine manufacturers have their own version of sensor based in-process inspection systems. It is unclear whether these systems are capable of the sophistication and analytical power of PrintRite3D®. However, Sigma Labs retains patent ownership within the space covering sensor based in-process inspection methods. Further, there is an inherent conflict of interest when a printer manufacturer incorporates its own in-process quality inspection solution in the part-build process. It is an unaccepted practice in Quality Assurance that a manufacturing machine, or process, also performs its own self inspection and critical evaluation of a produced part. PrintRite3D® provides a completely independent 3rd party quality assurance platform that impartially determines build-to-specification qualification and certification. Independent impartiality is a key aspect of the service offered by PrintRite3D®. None the less, serious competition may come from some of these players. To date, information covering the industry’s testing, evaluations, and the various standards development projects, indicates that thus far only Sigma Labs’ PrintRite3D® is being utilized in these efforts.
Perhaps the largest force for Sigma Labs’ product move into the industry is the pull that is inherent in the motivation behind Additive Manufacturing itself. Promising unprecedented part design freedom, enhanced part function, integrity, and system efficiencies across the shop floor, the cost savings to manufacturing and service divisions across the global network of manufacturing should easily be in the multiple tens of billions of dollars, and could approach $100 billion. PrintRite3D® is a vital enabler of these savings. Just at GE alone, in their September 2016 AM Investors Meeting Conference, Jeff Immelt, the CEO of GE, stated that they believe the cost savings will be $3 to $5 billion:
“We expect the business to have about $300 million of revenue in 2017 and grow quickly to $1 billion by 2020. In addition, it should facilitate $3 billion to $5 billion of cost out inside GE over time.”
In certain cases PrintRite3D®’s advanced sensor technology is not just an additional product, but a necessity. Additive Manufacturing pioneer and current GE Executive, Greg Morris, stated that GE Aviation sees the use of sensor based inspection systems as a necessity. In that same September 2016 Investor Conference Morris stated:
“We see four primary industry drivers that create the value chain, machines; materials; production; and services. Primary among these is the maturation and advancement of the equipment capabilities. Current laser and electron beam technology is very capable, but in order to achieve mass adoption, we will need to take machine productivity and speed to a new level. For each step change in machine speed and size, the number of parts that become candidates for additive multiplies exponentially. We also believe there are number of opportunities to incorporate advanced sensing and monitoring capabilities into future machines that will result in unparalleled part consistency and quality.”
These savings will be repeated across the global AM manufacturing industry. But with respect to the industry knowing that conventional post-build inspection makes the proposition unprofitable, there is a very large pull for the type of in-process inspection and analysis that Sigma Labs’ PrintRite3D® package provides. Sigma Labs states in their SEC form S1 that the company believes PrintRite3D® is capable of reducing manufacturing costs by a factor of 10, and development time for new design parts by 50% or more. It has been stated numerous times that current post-build inspection techniques cost more than the making of the part; on the order of $1 dollar to build verses $6 dollars to inspect.
Assisting this pull into the AM industry is the fact that PrintRite3D® is printer machine agnostic. Sigma Labs’ product suite can be installed within any of the various manufacturers’ machines. This aspect is very important because not only are build processes different between different machines and materials, but repeat builds on the same machine can vary in quality. It is within this framework that Sigma Labs’ In-Process Quality Assurance™ will excel, allowing end users to have certification of part quality from different suppliers, using different machines, and different processes.
Additionally, efforts have long been underway to integrate the front-end, machine, and back-end software platforms to enable seamless handling of data, planning and logistics. A much anticipated 3D part-build software simulation platform for the front-end of the AM process is expected from the private company 3DSIM, out of Park City, Utah. In early 2016 Sigma Labs signed a Technology Development Agreement with 3DSIM to link the analysis and IPQA® capabilities of the two platforms. A combination of 3DSIM’s modeling and PrintRite3D®’s in-process inspection would lead to a groundbreaking, powerful, new level of AM manufacturing process offering to the industry. This should prove to be a powerful tool in the offering of Quality Assurance to the AM industry.
Complementary to the push/pull from the AM industry, Sigma Labs established a 3D Printing Contract Manufacturing division internally to the company. This division employs an EOS M290 printer machine for providing contract printing services to corporations desiring AM production parts. Sigma Labs’ printer utilizes the full PrintRite3D® suite of modules for providing Quality as a Service (QaaS) to their customers. This ability enables Sigma Labs to both serve the contract printing demand in the industry, and ensure that they are abreast of the technological challenges and changes that are presented in the AM industry. With Sigma Labs’ QaaS philosophy using PrintRite3D®, the customer base experiences the full potential of Sigma Labs’ product line.
Sigma Labs’ Contract Printing division is growing. Aside from the traditional manufacturing powerhouses such as GE and Honeywell, the AM industry is seeing the birth of new powerful players who are shaking up the AM supply chain. One such company is Morf3D.
In February 2017 Sigma Labs announced it has entered into a strategic alliance with California based Morf3D. Morf3D is a forward thinking partnership between Altair, RUAG and Morf3D. It is focused on building the AM ecosystem and is deeply connected within the aerospace, space, medical and automotive industry for AM manufacturing.
“In an effort to bring enhanced solutions for additive manufacturing (“AM”) to the aerospace and defense (“A&D”) sector and capitalize on growth in demand for 3D printed metal components within the A&D industry, we recently entered into a strategic alliance with Morf3D, a California based company that specializes in additive engineering and manufacturing with metals and that provides advisory services in additive manufacturing strategy and technology adoption road-mapping. By leveraging our PrintRite3D® quality assurance software, we believe that Morf3D will be able to provide a means for its customers to increase AM production rates while ensuring consistent part quality, thereby better meeting the high quality demands of its aerospace customers. We also plan to work together with Morf3D to manufacture certain 3D printed parts. Morph3D has informed us that it is a party to development contracts with aircraft, space, medical and automotive customers, and that it expects to commence serial production contracts in 2017. We believe that by working together with Morf3D, the companies we will be in a position to design, manufacture, and assure the quality of AM components across a number of important aerospace applications….” (Quoted from February 2017 S-1 filing, page 38).
The partnership divides the responsibilities with Altair’s focus on software for design and analysis, Morf3D leading program management, part production and quality control, and RUAG leading the design, analysis, documentation, testing and certification. As Franck Mouriaux, GM at RUAG, said “The partnership between Altair, Morf3D and RUAG Space puts together the perfect ecosystem to revolutionize the way space components are engineered, produced and qualified. This breakthrough is absolutely mandatory for us to face the challenges of the new space industry and remain competitive.”
Sigma Labs has recently been making significant moves to bolster its corporate balance sheet and exposure to the wider financial and investment world. In January 2017 the company announced that two new Board of Directors, Sam Bell and Frank Garofalo, would become board members effective immediately. A third board member, John Rice, will be added effective after the closing of a currently open secondary share offering. These three members are significant additions to the leadership of Sigma Labs. All three newly appointed board members have lengthy records of success and experience within the corporate world.
In February 2017 the company issued SEC Form S-1/A detailing current business status, planning, and formal request submissions for share listing on the NASDAQ Capital Market (continuing under the SGLB ticker). The up-listing was successful. On February 15th Sigma Labs’ stock and warrants began trading on the NASDAQ. Associated with the listing on the NASDAQ exchange, Sigma Labs opened an underwritten secondary share offering for raising new cash for facilitating company growth, expansion of their Contract Printing Division, and shoring up the company balance sheet. The secondary offering is intended to raise just under $6 million USD, and result in 4,653,789 shares outstanding, The authorized share limit for the company will be 7,500,000 shares. There was room in the authorized share count for Sigma Labs to have attempted a higher cash raise in the offering. The fact that they did not may be an indication that they expect significant new commercial contract revenue from the AM industry. In any case, the moves would serve to greatly strengthen the directorship, corporate balance sheet, and provide the opportunity for a much larger investor base to take part in Sigma Labs’ business.
One of the interesting aspects of an investment in Sigma Labs is that of current timing. The 2013 bubble that all 3D printing stocks experienced was pierced as investors came to realize they had significantly misjudged the difficulty and delays encountered in establishing and initiating AM industry manufacturing and revenue streams. 3D Printing stocks found their bottom in 2016 and have since moved up. Sigma Labs experienced the same share price rise and decline as the rest of the 3D printing space. However, Sigma Labs’ share price continued to decline in the limited OTC market as the twin drivers of uncertainty over whether sensor based in-process technologies would be incorporated by the AM industry, and shareholder dissatisfaction over the pace of developments within the industry, took effect. Industry delays stretched the company’s bottom line. Additionally, the prevailing secrecy within the nascent and highly competitive AM industry shrouded progress updates and data that would have been useful for determining company valuations. As a result, it is probable that most of Sigma Labs’ future growth is not currently factored into the stock price.
Valuation
Current Wall Street discussions of the 3D printing industry revolve around the corporations that have participated in the industry for a number of years. So far, this does not include Sigma Labs. A successful up-list to the NASDAQ exchange, coupled with an onset of revenue generating contracts, will change that. Once Sigma Labs is considered as an industry participant within Wall Street, the company should begin being valued similarly to the rest of the industry.
There are very few pure-play 3D print industry companies; even fewer for metal AM specifically. The STOXX Global 3D Pure-Play Index includes just 9 companies, including 3D Systems, Stratasys, Materialise, Voxeljet, ExOne, SLM Solutions, Organovo and Perception Inc. Among this group, the minimum, maximum, and average earnings per share ratio is -5.74, 0.22, and -1.70. The minimum, maximum and average price per sales ratio is 1.00, 10.05 and 4.45.
As the market ponders a proper valuation for Sigma Labs, a median pricing of the company would place it around a price per sales ratio of 4.45. Upon completion of the secondary share offering, with an outstanding share count of 4,653,789, a $10 million per year sales rate would place the stock in the neighborhood of $9.50 per share. A $20 million per year rate would price the stock around $19.00 per share.
The continued diligent work by the industry and Sigma Labs over the past three years has put the company in a position where the onset of real contract revenues looks to have begun. While an investment in Sigma Labs will require some patience yet, the pace of developments within the industry is moving rapidly now. With the industry looking at PrintRite3D®’s capabilities as a powerful enabler of the manufacturing process, Sigma Labs should see considerable growth going forward.
Recent SASI News
- Form D - Notice of Exempt Offering of Securities • Edgar (US Regulatory) • 03/06/2024 02:09:28 PM
- Form 8-K - Current report • Edgar (US Regulatory) • 02/22/2024 09:20:29 PM
- Form 8-K - Current report • Edgar (US Regulatory) • 02/12/2024 10:11:48 PM
- Form DEFA14A - Additional definitive proxy soliciting materials and Rule 14(a)(12) material • Edgar (US Regulatory) • 02/12/2024 02:01:27 PM
- Form DEF 14A - Other definitive proxy statements • Edgar (US Regulatory) • 02/09/2024 10:30:29 PM
- Form 4 - Statement of changes in beneficial ownership of securities • Edgar (US Regulatory) • 02/05/2024 01:25:51 PM
- Form PRE 14A - Other preliminary proxy statements • Edgar (US Regulatory) • 01/30/2024 11:12:15 PM
- Form 8-K - Current report • Edgar (US Regulatory) • 01/30/2024 09:45:39 PM
- Form 4 - Statement of changes in beneficial ownership of securities • Edgar (US Regulatory) • 01/23/2024 09:15:49 PM
- Form 8-K/A - Current report: [Amend] • Edgar (US Regulatory) • 01/16/2024 09:30:35 PM
- Form 8-K - Current report • Edgar (US Regulatory) • 01/16/2024 01:32:12 PM
- Form 8-K/A - Current report: [Amend] • Edgar (US Regulatory) • 01/10/2024 09:30:17 PM
- Form 8-K - Current report • Edgar (US Regulatory) • 01/09/2024 10:00:16 PM
- Form 4 - Statement of changes in beneficial ownership of securities • Edgar (US Regulatory) • 01/04/2024 01:39:21 AM
- Form 4 - Statement of changes in beneficial ownership of securities • Edgar (US Regulatory) • 01/04/2024 01:38:26 AM
- Form 8-K - Current report • Edgar (US Regulatory) • 01/03/2024 01:30:17 PM
- Form 8-K - Current report • Edgar (US Regulatory) • 01/02/2024 10:20:32 PM
- Form DEFA14A - Additional definitive proxy soliciting materials and Rule 14(a)(12) material • Edgar (US Regulatory) • 12/07/2023 01:35:07 PM
- Sigma Additive Solutions Announces Filing of Definitive Proxy Statement Relating to Proposed Acquisition and Shareholder Vote • Business Wire • 12/07/2023 01:31:00 PM
- Form DEF 14A - Other definitive proxy statements • Edgar (US Regulatory) • 12/01/2023 11:03:17 AM
- Form 8-K - Current report • Edgar (US Regulatory) • 11/24/2023 09:05:37 PM
NanoViricides Reports that the Phase I NV-387 Clinical Trial is Completed Successfully and Data Lock is Expected Soon • NNVC • May 2, 2024 10:07 AM
ILUS Files Form 10-K and Provides Shareholder Update • ILUS • May 2, 2024 8:52 AM
Avant Technologies Names New CEO Following Acquisition of Healthcare Technology and Data Integration Firm • AVAI • May 2, 2024 8:00 AM
Bantec Engaged in a Letter of Intent to Acquire a Small New Jersey Based Manufacturing Company • BANT • May 1, 2024 10:00 AM
Cannabix Technologies to Deliver Breath Logix Alcohol Screening Device to Australia • BLO • Apr 30, 2024 8:53 AM
Hydromer, Inc. Reports Preliminary Unaudited Financial Results for First Quarter 2024 • HYDI • Apr 29, 2024 9:10 AM