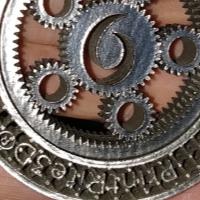
Monday, September 18, 2017 2:57:00 AM
The evolution of AM from prototyping to volume manufacturing in production runs is occurring in, and led by, aerospace while also appearing in niche products such as medical appliances and replacement parts of diverse applications, including unavailable parts required by still deployed but aging technologies. A major problem for 3D metal products production-run manufacturing today is that traditional quality systems rely heavily on after-manufacture inspection procedures that lack strong statistical reliability in small lot manufacturing. Post-production non-destructive test instruments from ultrasound to CT Scans are either not effective or not cost efficient on many complex part configurations that take advantage of 3D capability, and in the case of CT scans, are prohibitively expensive for production cost efficiency. The most important feature of our PrintRite3D® is that it develops actionable quality and process control data of manufacturing information in real-time and, when no flaws are detected, can provide manufacturers and their end-users with a part-by-part quality certification backed up by a file of supporting data.
Our PrintRite3D® suite, as described below, is composed of hardware, software, data analytics, and proprietary algorithms. The hardware is an array of photodiodes, non-contact pyrometer, and a data processing unit that can be either sold with an AM manufacturing machine unit by an OEM manufacturer or retrofitted on customers’ sites.
?PrintRite3D® SENSORPAK™ – the auxiliary sensor and hardware kit that sits on every AM machine to collect the data to drive the software.
?PrintRite3D® INSPECT™ – software which verifies quality layer by layer.
?PrintRite3D® CONTOUR™ – software which assures the as-built geometry.
27
The following software modules are currently in development:
?PrintRite3D® ANALYTICS™ – software that harvests, aggregates, and analyzes big data from in-process manufacturing data and post-process manufacturing data.
?PrintRite3D® THERMAL™ – software which predicts the residual stress and distortion in the part.
The proprietary software and its embedded algorithms process the very substantial quantity of layer by layer data gathered and then informs operators of the Quality Compliance status of each part in a build. We have been active in patent protecting our in-depth data analysis and quality algorithms to link our analysis to root cause metallurgy for determining the granular quantification of the part conformance to metallurgical requirements such as tensile strength. Concurrent with assessing the internal quality features of all parts in a build, PrintRite3D® deploys its CONTOUR™ module that measures each part’s adherence to the configuration specification of both internal channels and external form. OEM machine manufacturers as well as control system manufacturers may use the Sigma data stream to direct machine performance adjustments.
We have developed a tool that enables companies using Additive Manufacturing equipment for metal parts to move from prototyping on into production runs by assuring quality in a uniquely reliable and cost effective fashion. Not only does PrintRite3D® enable a single AM machine to operate at high quality yields, by measuring the product of the manufacturing equipment rather than just the equipment settings, it also is a reliable method to assure and document uniform quality assurance of a single part’s specification being manufactured by factories utilizing a number of different AM machines.
We believe that the broad domain coverage of our PrintRite3D® patents and metallurgical know-how make the licensing of our product suite to be the best means by which Additive Manufacturing OEM equipment manufacturers can offer in-process-quality-monitoring that certifies and documents the quality of all parts that pass continuous inspection. PrintRite3D® provides 3D metal manufacturing equipment makers with a patent protected data configuration of information that the manufacturers may use to adjust controls of their equipment in response to real-time quality information by, for example, precisely adjusting laser power to sustain manufacturing to design and specification.
Our IPQA®-enabled PrintRite3D® software Apps appear well suited to meet the needs of metal AM at this critical juncture in its development. Our technology will allow metal AM to be used during manufacturing of safety-critical or performance-critical metal parts, such as used in aerospace, defense and biomedical. Currently, these applications are difficult because the part quality cannot be completely guaranteed using today’s conventional nondestructive inspection technologies, because using inspection after manufacturing is difficult, costly and does not find all defects of concern. Therefore, we believe that PrintRite3D® could be an enabler for metal AM to realize its full potential. We have unique and patent protected offerings in this field. Furthermore, as a greater number of these AM applications could be cloud-based, the PrintRite3D® technology is fully compatible with highly networked, cloud- or web-based implementation – subject to the data and intellectual property restrictions which may be imposed by some companies for competitive reasons.
Our proprietary PrintRite3D® software Apps have been demonstrated and tested at many manufacturing sites around the world. We believe these demonstrations have served to validate the underlying technology of PrintRite3D® INSPECT™ and SENSORPAK™ software and hardware modules, respectively. In addition, we have developed relationships with experienced aerospace companies in North America that have assisted in the validation of the underlying technology for our PrintRite3D® software App known as CONTOUR™.
We continue to work with General Electric under our Joint Technology Development Agreement (“JTDA”), dated April 10, 2013, to demonstrate and implement our in-process inspection technologies for additive manufactured jet engine components. We are continuing to work with Honeywell Aerospace on the separate development of our PrintRite3D® CONTOUR™ software App for metal-based AM under our Trial Evaluation Agreement with Honeywell Aerospace, which sets forth the parties’ intent to use Honeywell’s Advanced Manufacturing Engineering Center as a beta test site for our PrintRite3D® CONTOUR™ software module. In further support of this effort, in 2015 Honeywell Aerospace installed its second PrintRite3D® system on one of its Concept Laser M2 machines at their Advanced Manufacturing Engineering Center in Phoenix, Arizona.
We have expanded our market presence and associated installed base of PrintRite3D® systems through our EAP and our OEM Partner Program to include European companies in France, Germany and The Netherlands. These European partners’ installations are key to our long term strategy to broaden its installed base through our EAP as well as gain market presence though embedded OEM offerings of our PrintRite3D® technology. Our PrintRite3D® product commercialization efforts reflect the strategic nature of our selective alliance partnerships.
VAYK Confirms Insider Buying at Open Market • VAYK • Nov 5, 2024 10:40 AM
Rainmaker Worldwide Inc. Announces Strategic Partnership Between Miranda Water Technologies and Fleming College • RAKR • Nov 4, 2024 12:03 PM
North Bay Resources Announces Assays up to 9.5% Copper at Murex Copper Project, British Columbia • NBRI • Nov 4, 2024 9:00 AM
Rainmaker Worldwide Inc. to Assume Direct, Non-Dealer Sales of Miranda Water Technologies in U.S. and Mexico in First Quarter of 2025 • RAKR • Nov 4, 2024 8:31 AM
CBD Life Sciences Inc. (CBDL) Launches High-Demand Mushroom Gummy Line for Targeted Wellness Needs, Tapping into a Booming $20 Billion Market • CBDL • Oct 31, 2024 8:00 AM
Nerds On Site Announces Q1 Growth and New Initiatives for the Remainder of 2024 • NOSUF • Oct 31, 2024 7:01 AM