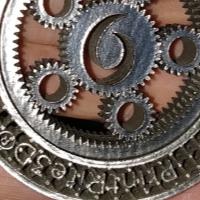
Saturday, August 05, 2017 2:49:32 AM
https://www.google.com/url?sa=t&source=web&rct=j&url=https://drc.libraries.uc.edu/bitstream/handle/2374.UC/745767/ISABE2015_CS%2526A_Mark%2520J.%2520Cola_227_MANUSCRIPT_20190.pdf%3Fsequence%3D2&ved=0ahUKEwic8su1v7_VAhVCziYKHUBdDtIQFgg7MAg&usg=AFQjCNH_WrDK2IJZbN9x37QplXXMEpRabg
IN-PROCESS QUALITY ASSURANCE™ A PROCESS MONITORING
AND INSPECTION TOOL FOR ADDITIVE MANUFACTURING
ISABE2015-20190
Vivek R. Dave, Mark J. Cola and R. Bruce Madigan*
Sigma Labs, Inc.
Santa Fe, NM 87501
*Montana Tech University
Butte, MT 59701
ABSTRACT
Despite the outstanding
promise of 3D Printing (3DP) and
Additive Manufacturing (AM) for
critical metal parts, three basic
limitations exist that will hold
back growth and cost-effectiveness
of current and future applications:
Quality, Geometry and Speed. In
terms of quality, Additive
manufacturing for highly critical
metal parts such as for aerospace
and automotive still exhibits
variability between runs, between
machines, and over time. In terms
of geometry, Additive manufacturing
can only realize a dimensional
accuracy of about 100 microns with
a positioning accuracy of about 20
microns, and the surface finish is
very rough as compared to aerospace
requirements. Also, the geometry
must currently be measured by
expensive post-process inspection
such as x-ray CT scanning. In
terms of productivity and speed,
the typical output of an AM machine
for metal is still below 20 cc/hr.,
and the entire world's production
capacity of AM metal machines
running 24-7-365 for an entire year
would still produce less material
than a steel mill could produce in
half of one daily shift. Sigma
Labs, Inc. is addressing the first
two issues, namely quality and
geometry, by implementing in-
process NDI as well as process
monitoring for metal Additive
Manufacturing. Specific sensing
and measurement technologies will
be discussed as well as the 'Big
Data' challenges of accumulating up
to terabytes of data per part and
then analyzing this data to produce
actionable knowledge. Also, the
reporting and interfacing
requirements will be discussed to
ensure that in-process, real-time
on-machine inspection data can be
effectively integrated into
existing and legacy manufacturing
execution systems and enterprise
data systems used by many large
aerospace and automotive suppliers.
INTRODUCTION
From a technical perspective,
there are three high level steps
that must be undertaken to design
and implement a quality control
system for any manufacturing
process including Additive
manufacturing: i) the establishment
of technical requirements linked to
ultimate end-use performance; ii)
the development and implementation
of a quality control system and
associated destructive and non-
destructive measurements capable
of directly or indirectly measuring
attributes of parts or defects; and
iii) the data analysis, correlation
methodology, and uncertainty
quantification to show in a
mathematically rigorous manner that
the measurements and data gathered
by the quality control system will
in fact correlate to the technical
requirements needed to meet end-use
environment performance targets,
and that the quality control system
over time will support such
objective evidence of compliance.
ZenaTech, Inc. (NASDAQ: ZENA) Launchs IQ Nano Drone for Commercial Indoor Use • HALO • Oct 10, 2024 8:09 AM
CBD Life Sciences Inc. (CBDL) Targets Alibaba as the Next Retail Giant for Wholesale Expansion of Top-Selling CBD Products • CBDL • Oct 10, 2024 8:00 AM
Foremost Lithium Announces Option Agreement with Denison on 10 Uranium Projects Spanning over 330,000 Acres in the Athabasca Basin, Saskatchewan • FAT • Oct 10, 2024 5:51 AM
Element79 Gold Corp. Reports Significant Progress in Community Relations and Development Efforts in Chachas, Peru • ELEM • Oct 9, 2024 10:30 AM
Unitronix Corp Launches Share Buyback Initiative • UTRX • Oct 9, 2024 9:10 AM
BASANITE INDUSTRIES, LLC RECEIVES U.S. PATENT FOR ITS BASAFLEX™ BASALT FIBER COMPOSITE REBAR AND METHOD OF MANUFACTURING • BASA • Oct 9, 2024 7:30 AM