Followers | 9 |
Posts | 1597 |
Boards Moderated | 1 |
Alias Born | 01/27/2014 |
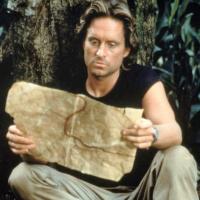
Friday, July 14, 2017 4:57:04 AM
improved titanium alloy to reduce aircraft weight
In looking for more information about Aidimme, GH Induction's additive partner, I found another interesting process development.
At interempresas.net - Aidimme investiga la fabricación 3D con una aleación mejorada de titanio para reducir el peso de los aviones - 17/02/2017
The spanish article using Google translate:
The Technological Institute coordinates Nanotun3D which will significantly reduce the CO2 emissions of aircraft
Aidimme investigates 3D manufacturing with an improved titanium alloy to reduce aircraft weight
Drafting Interempresas 2/17/2017
The Metalmecánico Technological Institute, furniture, wood, packaging and related industries, Aidimme , is developing a new base alloy modified titanium ceramics for additive metal fabrication nanoparticles that will strengthen the structure between 15 and 40% and substantially reduced The weight of the components, with an estimated savings of materials between 40 and 50%, compared to those manufactured using traditional processes. Particularly attractive features for a sector such as aerospace, according to the promoters of the European research project Nanotun3D.
The new material in development, Nanotun3D, takes the name of the European project with the same name in which 9 partners from Belgium, Great Britain, Germany, Italy and Spain participate, including the Aidimme Technological Institute itself, research coordinator.
Less weight, fuel economy, less CO 2
The ambitious Nanotun3D initiative 'Developing the complete workflow to produce and use a novel nanomodified Titanium-based alloy by additive manufacturing for special applications' offers a great benefit to the airline sector, with estimated savings of between 0.02 and 0, 04 liters of fuel per hour for each kilogram of reduced weight in the parts, as well as a substantial reduction of CO 2 emissions , in the same way as for the space sector, and where the performance of the structural properties of the materials is a Critical aspect for both.
Another key aspect of transferring the results to the aerospace industry is the qualification of the new material and manufacturing process. It is a question of verifying that the results obtained reach the established standards and are verified over time and in different batches of manufacture. During the project, the bases are being laid to carry out the aforementioned qualification, so as to facilitate the manufacturers of aeronautical components the certification of the products manufactured with this new alloy processed by additive technology.
In this way, the project has taken on the challenge of providing the aerospace sector with solutions with the material and systems indicated under strict compliance with the Safety Management System (SMS) of services and products for aircraft.
Workflow Nanotund3D: development of nano-modified materials for additive manufacturing and characterization of their operational life cycle, from the synthesis of nanoparticles and the manufacture of metal powder to the final piece.
Additive Manufacturing
It also brings direct advantages to other sectors such as automotive, dental and dental implants, and capital goods, for example, and the many inherent to the additive manufacturing itself, such as the design and manufacture of complex geometries; Manufacturing on demand; The reduction of time to market; The absence of production tools, the processing of materials to measure; Cost savings due to material reduction; Reduction of the supply chain; And the manufacture of spare parts and repair of damaged parts, among other advantages.
The efficient dispersion of silicon carbide (SiC) nanoparticles is fundamental for improving Ti6Al4V alloys, and for this it is necessary to ensure their presence throughout the entire production chain, even after the additive manufacturing process. The novel core-shell configuration adopted in this research protects the nanoparticle during the transformation process and reinforces the metal matrix.
Consolidated Ti6Al4V matrix with silicon carbide (SiC) nanoparticles and titanium dioxide (TiO2) coating by HIP, to produce electrodes for the EIGA process.
Innovation through 'core-shell'
In this line of work, Nanotun3D provides an innovative concept based on 'core-shell' structures to solve this limitation and thus improve the dispersion and guarantee presence of SiC nanoparticles, where the core is made of silicon carbide and Outer material is a metal oxide, either ferric oxide (Fe 2 O 3 ) or titanium dioxide (TiO 2 ). In this sense, the research currently addresses a series of tests for the correct synthesis and fabrication of 'core-shell' encapsulation at an industrial pilot scale that allows a suitable embedding of the ceramic nanoparticles in the Ti6Al4V matrix and thus improve the interaction In the whole process, from obtaining the metallic powder,
Equipment for the production of core-shell nanoparticles on an industrial scale.
HSE
The project also considers the incorporation of HSE (health, safety and environmental) policies and standards in order to control the safety risks associated with the use of nanoparticles along the value chain Of the industry, and will define safe work processes in the manufacture, manipulation and processing of metallic powder.
Powder manufacturing, FA processing and post-processing
In addition, the project addresses new lines of research for the manufacture of industrial powders using standard atomization techniques after casting, such as gas (GA) and its electrode induction variant (EIGA). With reactive alloys such as titanium. In the same way, a redesign of the injection-molding system (DIE) for gas atomization is used, which allows the nanoparticles to be inserted during the atomization process for the manufacture of the metallic powder with a suitable dispersion.
At the same time, adjustments are being made to the parameters required to process the new nanomodified material through laser selective sintering (SLM) and EBM (electron beam fusion) systems and modifications that may be required by the processing machinery Dust, as well as the reuse of the residual dust.
The research includes an exhaustive evaluation of post-processing in terms of thermal and surface treatments, among other factors such as ease of machining, in order to improve roughness, fatigue behavior, reduction of residual stresses and distortions of Manufactured parts.
In looking for more information about Aidimme, GH Induction's additive partner, I found another interesting process development.
At interempresas.net - Aidimme investiga la fabricación 3D con una aleación mejorada de titanio para reducir el peso de los aviones - 17/02/2017
The spanish article using Google translate:
The Technological Institute coordinates Nanotun3D which will significantly reduce the CO2 emissions of aircraft
Aidimme investigates 3D manufacturing with an improved titanium alloy to reduce aircraft weight
Drafting Interempresas 2/17/2017
The Metalmecánico Technological Institute, furniture, wood, packaging and related industries, Aidimme , is developing a new base alloy modified titanium ceramics for additive metal fabrication nanoparticles that will strengthen the structure between 15 and 40% and substantially reduced The weight of the components, with an estimated savings of materials between 40 and 50%, compared to those manufactured using traditional processes. Particularly attractive features for a sector such as aerospace, according to the promoters of the European research project Nanotun3D.
The new material in development, Nanotun3D, takes the name of the European project with the same name in which 9 partners from Belgium, Great Britain, Germany, Italy and Spain participate, including the Aidimme Technological Institute itself, research coordinator.
Less weight, fuel economy, less CO 2
The ambitious Nanotun3D initiative 'Developing the complete workflow to produce and use a novel nanomodified Titanium-based alloy by additive manufacturing for special applications' offers a great benefit to the airline sector, with estimated savings of between 0.02 and 0, 04 liters of fuel per hour for each kilogram of reduced weight in the parts, as well as a substantial reduction of CO 2 emissions , in the same way as for the space sector, and where the performance of the structural properties of the materials is a Critical aspect for both.
Another key aspect of transferring the results to the aerospace industry is the qualification of the new material and manufacturing process. It is a question of verifying that the results obtained reach the established standards and are verified over time and in different batches of manufacture. During the project, the bases are being laid to carry out the aforementioned qualification, so as to facilitate the manufacturers of aeronautical components the certification of the products manufactured with this new alloy processed by additive technology.
In this way, the project has taken on the challenge of providing the aerospace sector with solutions with the material and systems indicated under strict compliance with the Safety Management System (SMS) of services and products for aircraft.
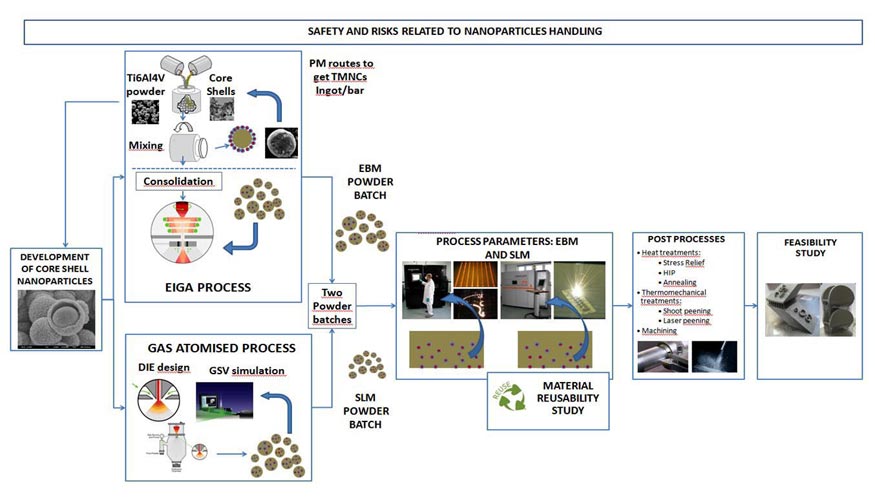
Workflow Nanotund3D: development of nano-modified materials for additive manufacturing and characterization of their operational life cycle, from the synthesis of nanoparticles and the manufacture of metal powder to the final piece.
Additive Manufacturing
It also brings direct advantages to other sectors such as automotive, dental and dental implants, and capital goods, for example, and the many inherent to the additive manufacturing itself, such as the design and manufacture of complex geometries; Manufacturing on demand; The reduction of time to market; The absence of production tools, the processing of materials to measure; Cost savings due to material reduction; Reduction of the supply chain; And the manufacture of spare parts and repair of damaged parts, among other advantages.
The efficient dispersion of silicon carbide (SiC) nanoparticles is fundamental for improving Ti6Al4V alloys, and for this it is necessary to ensure their presence throughout the entire production chain, even after the additive manufacturing process. The novel core-shell configuration adopted in this research protects the nanoparticle during the transformation process and reinforces the metal matrix.
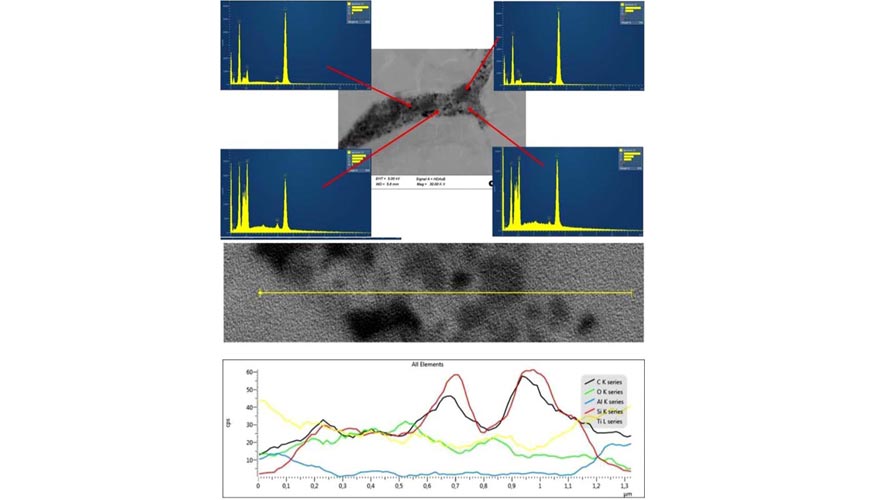
Consolidated Ti6Al4V matrix with silicon carbide (SiC) nanoparticles and titanium dioxide (TiO2) coating by HIP, to produce electrodes for the EIGA process.
Innovation through 'core-shell'
In this line of work, Nanotun3D provides an innovative concept based on 'core-shell' structures to solve this limitation and thus improve the dispersion and guarantee presence of SiC nanoparticles, where the core is made of silicon carbide and Outer material is a metal oxide, either ferric oxide (Fe 2 O 3 ) or titanium dioxide (TiO 2 ). In this sense, the research currently addresses a series of tests for the correct synthesis and fabrication of 'core-shell' encapsulation at an industrial pilot scale that allows a suitable embedding of the ceramic nanoparticles in the Ti6Al4V matrix and thus improve the interaction In the whole process, from obtaining the metallic powder,
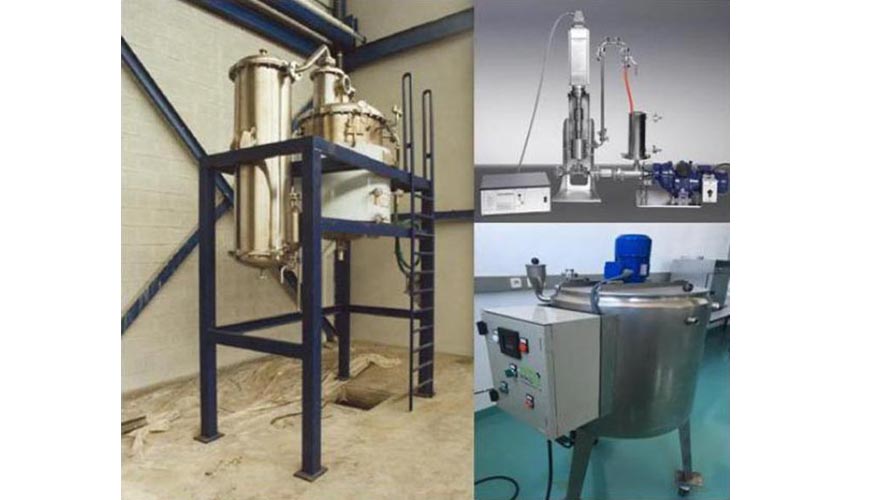
Equipment for the production of core-shell nanoparticles on an industrial scale.
HSE
The project also considers the incorporation of HSE (health, safety and environmental) policies and standards in order to control the safety risks associated with the use of nanoparticles along the value chain Of the industry, and will define safe work processes in the manufacture, manipulation and processing of metallic powder.
Powder manufacturing, FA processing and post-processing
In addition, the project addresses new lines of research for the manufacture of industrial powders using standard atomization techniques after casting, such as gas (GA) and its electrode induction variant (EIGA). With reactive alloys such as titanium. In the same way, a redesign of the injection-molding system (DIE) for gas atomization is used, which allows the nanoparticles to be inserted during the atomization process for the manufacture of the metallic powder with a suitable dispersion.
At the same time, adjustments are being made to the parameters required to process the new nanomodified material through laser selective sintering (SLM) and EBM (electron beam fusion) systems and modifications that may be required by the processing machinery Dust, as well as the reuse of the residual dust.
The research includes an exhaustive evaluation of post-processing in terms of thermal and surface treatments, among other factors such as ease of machining, in order to improve roughness, fatigue behavior, reduction of residual stresses and distortions of Manufactured parts.
Join the InvestorsHub Community
Register for free to join our community of investors and share your ideas. You will also get access to streaming quotes, interactive charts, trades, portfolio, live options flow and more tools.