Followers | 9 |
Posts | 1597 |
Boards Moderated | 1 |
Alias Born | 01/27/2014 |
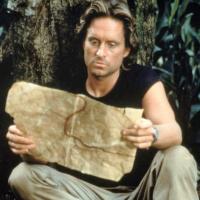
Tuesday, July 04, 2017 9:06:12 AM
3D Printing Orthopedic Surgeons’ Invention Ideas
This article does not mention EBM. It's significance is that it exemplifies how additive manufacturing will enable innovation from previously unused expert resources. It shows how practicing orthopedic surgeons work with an engineer to develop an idea, produce a very low cost non-functional prototype to visualize the device, produce (contract for manufacture) the actual metal prototypes used to prove the new part. If successful, the idea and proof are submitted to larger medical device manufacturers.
Additive manufacturing will enable the "high tech garage mechanics" in all areas, not just medical. Untapped experts will DEMAND innovation.
We've seen where large manufacturers have used croudsourcing to drive innovation:
HOW GE PLANS TO ACT LIKE A STARTUP AND CROWDSOURCE BREAKTHROUGH IDEAS
Airbus Group and Local Motors Challenge You to Help Design the Drones of the Future
_______________________________________________________________________
At odtmag.com - 3D Printing Orthopedic Surgeons’ Invention Ideas - 06.28.17
The introduction:
Jody Stallings, Industrial Creations
06.28.17
3D printing is becoming an important tool in nearly every industry today, but one area where it is really making an impact is in the medical field.
Doctors and surgeons can use 3D printed organ or bone models to explain to patients or students the details of a surgery or to practice the surgery itself. Other surgeons are actually designing their own prototypes of new surgical tools or bone replacement options.
The challenge, historically, is that 3D printing can be expensive and difficult to complete.
As a mechanical engineer, I began my career in automation design and robotics, but moved into the medical industry in 1990 when I was hired by an orthopedic knee replacement company. They asked me to utilize my experience to automate the process for finishing knee implants. It was a three-year project and the result was a new process that produced a knee implant in minutes instead of hours.
During that process, I saw the opportunity that surgeons have to develop new techniques and tools to enhance surgical procedures, but they lacked the resources to turn their ideas into a reality. Now, in my spare time I work with the doctors and surgeons to brainstorm a design based on their idea and 3D print it so that they can pitch to companies for production.
So, how does it all work?
An orthopedic surgeon comes up with an idea and it is then modeled using computer-aided design (CAD) software. The design is then printed using a desktop ABS 3D printer to fabricate the first conceptual models and get the surgeon to a point where they are happy with the design and are confident the part will be functional.
Up to this point, it’s fairly easy to manage time and expenses. However, when it comes time for a real functional prototype, that means working with metal and that’s when the costs start to increase. As the surgeons are often doing this on their own time and paying for it from their own pocket, it’s important that costs are managed.
Historically, the key to managing project costs has been to design parts with the prototyping or end manufacturing process in mind. This used to require thinking about manufacturability at every step so that the product design did not end up so complex and complicated that it couldn’t be manufactured. Up until 3D printing was capable of fabricating high-quality metal parts, this meant designing each part with machining in mind. Unfortunately, this significantly limited the complexity of the surgeons’ designs as well as the dimensions and shapes of the parts. Now, metal 3D printing has evolved to the point that it can be considered as the end manufacturing process. As a result, the surgeons can design streamlined, more complex parts with fine details that would be too hard to machine.
One example is implant designs that need to be porous to encourage bone growth. Adding porosity is very difficult in a machining application, because it relies on a laser taking material away from a solid part or a secondary material being applied. But with 3D printing, porosity can be built into the design and accurately output by the printer.
All things considered, designing for manufacturability has been massively aided by advancements in metal 3D printing.
This article does not mention EBM. It's significance is that it exemplifies how additive manufacturing will enable innovation from previously unused expert resources. It shows how practicing orthopedic surgeons work with an engineer to develop an idea, produce a very low cost non-functional prototype to visualize the device, produce (contract for manufacture) the actual metal prototypes used to prove the new part. If successful, the idea and proof are submitted to larger medical device manufacturers.
Additive manufacturing will enable the "high tech garage mechanics" in all areas, not just medical. Untapped experts will DEMAND innovation.
We've seen where large manufacturers have used croudsourcing to drive innovation:
HOW GE PLANS TO ACT LIKE A STARTUP AND CROWDSOURCE BREAKTHROUGH IDEAS
Airbus Group and Local Motors Challenge You to Help Design the Drones of the Future
_______________________________________________________________________
At odtmag.com - 3D Printing Orthopedic Surgeons’ Invention Ideas - 06.28.17
The introduction:
Jody Stallings, Industrial Creations
06.28.17
3D printing is becoming an important tool in nearly every industry today, but one area where it is really making an impact is in the medical field.
Doctors and surgeons can use 3D printed organ or bone models to explain to patients or students the details of a surgery or to practice the surgery itself. Other surgeons are actually designing their own prototypes of new surgical tools or bone replacement options.
The challenge, historically, is that 3D printing can be expensive and difficult to complete.
As a mechanical engineer, I began my career in automation design and robotics, but moved into the medical industry in 1990 when I was hired by an orthopedic knee replacement company. They asked me to utilize my experience to automate the process for finishing knee implants. It was a three-year project and the result was a new process that produced a knee implant in minutes instead of hours.
During that process, I saw the opportunity that surgeons have to develop new techniques and tools to enhance surgical procedures, but they lacked the resources to turn their ideas into a reality. Now, in my spare time I work with the doctors and surgeons to brainstorm a design based on their idea and 3D print it so that they can pitch to companies for production.
So, how does it all work?
An orthopedic surgeon comes up with an idea and it is then modeled using computer-aided design (CAD) software. The design is then printed using a desktop ABS 3D printer to fabricate the first conceptual models and get the surgeon to a point where they are happy with the design and are confident the part will be functional.
Up to this point, it’s fairly easy to manage time and expenses. However, when it comes time for a real functional prototype, that means working with metal and that’s when the costs start to increase. As the surgeons are often doing this on their own time and paying for it from their own pocket, it’s important that costs are managed.
Historically, the key to managing project costs has been to design parts with the prototyping or end manufacturing process in mind. This used to require thinking about manufacturability at every step so that the product design did not end up so complex and complicated that it couldn’t be manufactured. Up until 3D printing was capable of fabricating high-quality metal parts, this meant designing each part with machining in mind. Unfortunately, this significantly limited the complexity of the surgeons’ designs as well as the dimensions and shapes of the parts. Now, metal 3D printing has evolved to the point that it can be considered as the end manufacturing process. As a result, the surgeons can design streamlined, more complex parts with fine details that would be too hard to machine.
One example is implant designs that need to be porous to encourage bone growth. Adding porosity is very difficult in a machining application, because it relies on a laser taking material away from a solid part or a secondary material being applied. But with 3D printing, porosity can be built into the design and accurately output by the printer.
All things considered, designing for manufacturability has been massively aided by advancements in metal 3D printing.
Join the InvestorsHub Community
Register for free to join our community of investors and share your ideas. You will also get access to streaming quotes, interactive charts, trades, portfolio, live options flow and more tools.