Followers | 9 |
Posts | 1597 |
Boards Moderated | 1 |
Alias Born | 01/27/2014 |
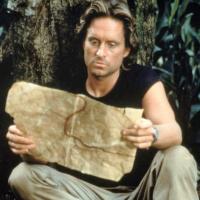
Thursday, September 22, 2016 11:39:09 AM
Connect the dots.
Read the referring post - Someone else connected some dots, too.
From the question and answer period at the end of the conference call:
Matthias Holmberg, DNB Markets - Analyst
"in orthopedics you only mentioned DePuy, which, at least to my knowledge, is not a customer today, and I just wonder if you would like to comment on that."
Magnus Rene, Arcam AB - CEO
"Obviously, they are a customer."
Then read - Johnson & Johnson Adopts Cutting Edge 3D Printing for the Future of Medical Devices - September 07, 2016
The introduction:
Healthcare is one of the industries to most dramatically see changes occur due to the use of 3D printing technology. In fact, market research firm Gartner suggests that it is the medical sector that is leading the advancement of 3D printing over other industries.
3D printing has already become the dominant technology used to manufacture patient-specific hearing aids and dental aligners and, more recently, 3D printing has become increasingly leveraged for the manufacturing of patient-tailored implants and instruments for craniomaxillofacial (CMF) reconstruction and knee and hip replacements. This is clearly just the beginning for additively manufactured products in the medical space, which will one day include 3D-printed organs and patient-specific pharmaceuticals.
Among the large industrial players to adopt 3D printing for the production of medical products is Johnson & Johnson, a multinational corporation with some 250 subsidiaries across 57 countries and a market cap of $323.8 billion. While the multinational corporation’s 3D-printed orthopedic implants have been on the market for several years, Johnson & Johnson is also partnering with some of the most exciting firms in the 3D printing space, such as Carbon, HP, 3D Systems, Organovo and Materialise.
To learn more about how the corporation will leverage the technologies from these firms, I spoke with Joseph Sendra, worldwide vice president of Manufacturing Engineering and Technology for Johnson & Johnson. As one might expect from such a large multinational corporation, the executive could not divulge too much about what Johnson & Johnson is working on behind closed doors, but Sendra was able to lay out the corporation’s larger vision for 3D printing technology.
3D-Printed Implants and Instruments
3D printing has long been adopted by manufacturers as a means of prototyping during the design process, but starting several years ago, Johnson & Johnson subsidiary DePuy Synthes began using the technology to produce patient-specific instruments and implants.
Sendra described the work being performed by DePuy Synthes, “We have a product line called TRUMATCH in our orthopedic segment that consists of implants and surgical guides for CMF surgery, and resection guides for knees that are personalized today. These personalized devices have complex geometries and are provided on demand for surgical applications in the CMF space and knee surgery.”
From Materialize - DePuy Synthes TruMatch CMF Solutions
From DePuy Synthes of Johnson & Johnson - TRUMATCH® CMF Solutions – PSI/ Materials
Titanium (commercially pure, implant grade)
Ultra-high strength as compared to cortical bone
Radioopaque
Autoclavable - withstands repeated sterilization
Titanium implant is 2.5 mm thick (nominal)
Titanium Mechanical Properties
Cortical Bone[1] Titanium[2]
Modulus of Elasticity (stiffness) (GPa) 8-24 103
Yield Strength (MPa) 115 230
Notes regarding the use of Titanium Patient Specific Implants:
Titanium Patient Specific Implants cannot be modified. If there are any minor fit modifications required, the surgeon must modify the patient's bone.
Titanium Patient Specific Implants require the use of DePuy Synthes Low Profile Neuro or MatrixNEURO fixation systems (plates and screws).
The surgeon must preselect the location of the DePuy Synthes plates and machine screw holes during the implant design review process.
The implant will be provided with threaded screw holes. The Titanium Low Profile Neuro Machine Screws (488.066) are required for attachment of the Low Profile Neuro or MatrixNEURO plates to the titanium implant.
[1] Mechanical test data on file at DePuy Synthes. Mechanical test results are not necessarily indicative of clinical performance.
[2] Per ISO 5832-2.
Read the referring post - Someone else connected some dots, too.
From the question and answer period at the end of the conference call:
Matthias Holmberg, DNB Markets - Analyst
"in orthopedics you only mentioned DePuy, which, at least to my knowledge, is not a customer today, and I just wonder if you would like to comment on that."
Magnus Rene, Arcam AB - CEO
"Obviously, they are a customer."
Then read - Johnson & Johnson Adopts Cutting Edge 3D Printing for the Future of Medical Devices - September 07, 2016
The introduction:
Healthcare is one of the industries to most dramatically see changes occur due to the use of 3D printing technology. In fact, market research firm Gartner suggests that it is the medical sector that is leading the advancement of 3D printing over other industries.
3D printing has already become the dominant technology used to manufacture patient-specific hearing aids and dental aligners and, more recently, 3D printing has become increasingly leveraged for the manufacturing of patient-tailored implants and instruments for craniomaxillofacial (CMF) reconstruction and knee and hip replacements. This is clearly just the beginning for additively manufactured products in the medical space, which will one day include 3D-printed organs and patient-specific pharmaceuticals.
Among the large industrial players to adopt 3D printing for the production of medical products is Johnson & Johnson, a multinational corporation with some 250 subsidiaries across 57 countries and a market cap of $323.8 billion. While the multinational corporation’s 3D-printed orthopedic implants have been on the market for several years, Johnson & Johnson is also partnering with some of the most exciting firms in the 3D printing space, such as Carbon, HP, 3D Systems, Organovo and Materialise.
To learn more about how the corporation will leverage the technologies from these firms, I spoke with Joseph Sendra, worldwide vice president of Manufacturing Engineering and Technology for Johnson & Johnson. As one might expect from such a large multinational corporation, the executive could not divulge too much about what Johnson & Johnson is working on behind closed doors, but Sendra was able to lay out the corporation’s larger vision for 3D printing technology.
3D-Printed Implants and Instruments
3D printing has long been adopted by manufacturers as a means of prototyping during the design process, but starting several years ago, Johnson & Johnson subsidiary DePuy Synthes began using the technology to produce patient-specific instruments and implants.
Sendra described the work being performed by DePuy Synthes, “We have a product line called TRUMATCH in our orthopedic segment that consists of implants and surgical guides for CMF surgery, and resection guides for knees that are personalized today. These personalized devices have complex geometries and are provided on demand for surgical applications in the CMF space and knee surgery.”
From Materialize - DePuy Synthes TruMatch CMF Solutions
From DePuy Synthes of Johnson & Johnson - TRUMATCH® CMF Solutions – PSI/ Materials
Titanium (commercially pure, implant grade)
Ultra-high strength as compared to cortical bone
Radioopaque
Autoclavable - withstands repeated sterilization
Titanium implant is 2.5 mm thick (nominal)
Titanium Mechanical Properties
Cortical Bone[1] Titanium[2]
Modulus of Elasticity (stiffness) (GPa) 8-24 103
Yield Strength (MPa) 115 230
Notes regarding the use of Titanium Patient Specific Implants:
Titanium Patient Specific Implants cannot be modified. If there are any minor fit modifications required, the surgeon must modify the patient's bone.
Titanium Patient Specific Implants require the use of DePuy Synthes Low Profile Neuro or MatrixNEURO fixation systems (plates and screws).
The surgeon must preselect the location of the DePuy Synthes plates and machine screw holes during the implant design review process.
The implant will be provided with threaded screw holes. The Titanium Low Profile Neuro Machine Screws (488.066) are required for attachment of the Low Profile Neuro or MatrixNEURO plates to the titanium implant.
[1] Mechanical test data on file at DePuy Synthes. Mechanical test results are not necessarily indicative of clinical performance.
[2] Per ISO 5832-2.

Join the InvestorsHub Community
Register for free to join our community of investors and share your ideas. You will also get access to streaming quotes, interactive charts, trades, portfolio, live options flow and more tools.