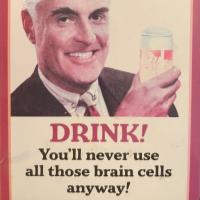
Wednesday, November 18, 2015 9:02:00 AM
Below is a warning letter from FDA to another company misbranding their hangover cure as a supplement in exactly the same way as HJOE does.
One day FDA will go after the crooks behind HJOE as well, assuming they haven't gone on the lam by then.
"Department of Health and Human Services
Public Health Service
Food and Drug Administration
Cincinnati District Office
Central Region
6751 Steger Drive
Cincinnati, OH 45237-3097
Telephone: (513) 679-2700
FAX: (513) 679-2775
September 17, 2015
Ms. Cheryl Krueger, President/Owner
Life Support Development Ltd
2818 Fisher Road
Columbus, OH 43204
Warning Letter
CIN-452082-25
Dear Ms. Krueger:
The U.S. Food & Drug Administration (FDA) conducted an inspection at your dietary supplement manufacturer and distributor, Life Support Development Ltd., located at 2818 Fisher Road, Columbus, OH on December 16, 17, 22 and 30, 2014. In addition, we reviewed your product label collected during the inspection. We also reviewed your website at https://lifesupport.com in September 2015 and determined that you take orders there for the product Life Support Hangover Relief.
Based on our inspection and subsequent review of your product labeling collected during the inspection, as well as your firm's website, we found serious violations of the Federal Food, Drug, and Cosmetic Act (the Act) and applicable regulations. You may find the Act and the FDA’s regulations through links on FDA’s home page at www.fda.gov.
Unapproved New Drug
We also have determined that Life Support Hangover Relief product is being promoted for conditions that cause the product to be a drug under section 201(g)(1)(B) of the Act [21 U.S.C. § 321(g)(1)(B)]. The therapeutic claims in your product labeling establish that the products are drugs because they are intended for use in the cure, mitigation, treatment, or prevention of disease.
Examples of claims that provide evidence that your Life Support Hangover Relief product is intended for use as a drug include:
•“Hangover Relief”
•“Tired of Hangovers? Life Support’s cutting-edge formula contains an extract from the fruit of the Japanese Raisin Tree, known specifically to aid in the recovery from alcohol intoxication.”
•(website) “Life Support can protect the liver and brain from damage …”
Your Life Support Hangover Relief product is not generally recognized as safe and effective for the above referenced uses and, therefore, the products are “new drugs” under section 201(p) of the Act [21 U.S.C. § 321(p)]. New drugs may not be legally introduced or delivered for introduction into interstate commerce without prior approval from FDA, as described in section 505(a) of the Act [21 U.S.C. § 355(a)]; see also section 301(d) of the Act [21 U.S.C. § 331(d)]. FDA approves a new drug on the basis of scientific data submitted by a drug sponsor to demonstrate that the drug is safe and effective.
Adulterated Dietary Supplement
Even if your Life Support Hangover Relief product was not an unapproved new drug, it would still be an adulterated dietary supplement under section 402(g)(1) of the Act. The inspection revealed significant violations of the CGMP requirements for dietary supplements. These violations cause your dietary supplement products to be adulterated under section 402(g)(1) of the Act [21 U.S.C.§ 342(g)(1)] in that they have been prepared, packed, or held under conditions which do not meet the Current Good Manufacturing Practice (CGMP) regulations for dietary supplements, Title 21, Code of Federal Regulations, Part 111 (21 CFR Part 111).
Specifically, our investigator observed the following significant violations:
1. Your firm failed to establish the following specifications as required by 21 CFR 111.70:
a) Identity specifications for each component that you use in the manufacture of a dietary supplement [21 CFR 111.70(b)(1)]. Specifically, your employee stated that your firm did not have specifications for incoming components;
b) Product specifications for the identity, purity, and strength, of the finished batch of the dietary supplement, and for limits on those types of contamination that may adulterate, or that may lead to adulteration of the finished batch of the dietary supplement to ensure the quality of the dietary supplement [21 CFR 111.70(e)]. Specifically, your Life Support Ingredient Breakdown that you provided to our investigator as documentation of product specifications does not contain specifications for the identity, purity, and strength of the finished batch of the dietary supplement or limits on any contaminants.
2. You failed to prepare and follow a written master manufacturing record (MMR) for each unique formulation of dietary supplement you manufacture and for each batch size, to ensure uniformity in the finished batch from batch to batch, in the manner required by 21 CFR 111.210. Though you informed our investigator that you did not have a MMR, there is evidence to suggest that you maintain documents that contain elements of an MMR. However, your MMR does not contain all the required elements; specifically:
a) The strength, concentration, weight or measure of each dietary ingredient for each batch size [21 CFR 111.210(a)];
b) An accurate statement of the weight or measure of each component to be used [21 CFR 111.210(c)];
c) A statement of theoretical yield of a manufactured dietary supplement expected at each point, step, or stage of the manufacturing process where control is needed to ensure the quality of the dietary supplement, and the expected yield when you finish manufacturing the dietary supplement, including the maximum and minimum percentages of theoretical yield beyond which a deviation investigation of a batch is necessary and material review is conducted and disposition decision is made [21 CFR 111.210(f)];
d) A representative label, or a cross-reference to the physical location of the actual or representative label [21 CFR 111.210(g)];
e) Written instructions, including specifications for each point, step, or stage in the manufacturing process where control is necessary to ensure the quality of the dietary supplement and that the dietary supplement is packaged and labeled as specified in the MMR [21 CFR 111.210(h)(1)];
f) Written procedures for sampling in the MMR and a cross reference to procedures for tests or examinations [21 CFR 111.210(h)(2)].
3. Your firm failed to follow written procedures for manufacturing operations as required by 21 CFR 111.353. Specifically, your employee provided the investigator with your “Production Procedure Outline” as documentation of your manufacturing operations; however, according to your employee, the procedure is not followed as some steps have changed and/or been omitted from production.
4. Your firm failed to establish and follow written procedures for the responsibilities of your quality control operations, including written procedures for conducting a material review and making a disposition decision, and for approving or rejecting any reprocessing, as required by 21 CFR 111.103. Specifically, your employee indicated to our investigator that no written procedures exist for your quality control operations.
Further, as a manufacturer and distributor that contracts with other entities to label packaging that your firm uses to package dietary supplements that are then distributed under your firm’s name, your firm has an obligation to know what and how labeling activities are performed so that you can make decisions related to whether your dietary supplement products conform to established specifications and whether to approve and release the products for distribution [72 Fed. Reg. 34752, 34790 (Jun. 25, 2007)]. Your firm introduces or delivers, or causes the introduction or delivery, of dietary supplement products into interstate commerce in their final form for distribution to consumers. As such, your firm has an overarching and ultimate responsibility to ensure that all phases of the production of that product are in compliance with dietary supplement CGMP requirements.
Although your firm may contract out certain operations, it cannot by the same token, contract out its ultimate responsibility to ensure that the dietary supplements it places into commerce (or causes to be placed into commerce) are not adulterated for failure to comply with dietary supplement CGMP requirements (see United States v. Dotterweich, 320 U.S. 277, 284 (1983) (explaining that an offense can be committed under the Act by anyone who has a “responsible share in the furtherance of the transaction which the statute outlaws”); United States v. Park, 421 U.S. 658, 672 (1975) (holding that criminal liability under the Act does not turn on awareness of wrongdoing, and that “agents vested with the responsibility, and power commensurate with that responsibility, to devise whatever measures are necessary to ensure compliance with the Act” can be held accountable for violations of the Act). In particular, the Act prohibits a person from introducing or delivering for introduction, or causing the delivery or introduction, into interstate commerce a dietary supplement that is adulterated under section 402(g) for failure to comply with dietary supplement CGMP requirements [21 U.S.C. §§ 342(g), 331(a)]. Thus, a firm that contracts with other firms to conduct certain dietary supplement manufacturing, packaging, or labeling operations for it is responsible for ensuring that the dietary supplement is not adulterated for failure to comply with dietary supplement CGMP requirements, regardless of who actually performs the dietary supplement CGMP operations.
Your firm must establish a system of production and process controls and implement quality control operations to ensure the quality of your dietary supplements and that the dietary supplements are packaged and labeled as specified in the master manufacturing record [21 CFR 111.55 and 111.65]. You firm must establish and follow written procedures for the responsibilities of the quality control operations [21 CFR 111.103]. The quality control personnel must ensure that your manufacturing, packaging, labeling, and holding operations ensure the quality of the dietary supplement and that the dietary supplement is packaged and labeled as specified in the master manufacturing record [21 CFR 111.105]. Further, you must have documentation of the quality control personnel review and approval of release for any packaged and labeled dietary supplement [21 CFR 111.127(h) and 111.140(b)(2)].
5. Your firm failed to collect and hold reserve samples of each lot of packaged and labeled dietary supplements that you distribute, as required by 21 CFR 111.83(a). Specifically, according to your employee, your firm did not collect and hold reserve samples for production lots 150, 156 and166.
6. Your batch production records (BPRs) do not include complete information relating to the production and control of each batch as required by 21 CFR 111.255(b). Specifically, we reviewed your BPRs for batches PR108, PR110, PR112 and PR113 of your Life Support Hangover Relief supplement. These BPR’s do not include the following information that is required by 21 CFR 111.260:
a) The identity of the equipment and processing lines used in producing the batch [21 CFR 111.260(b)];
b) The date and time of the maintenance, cleaning and sanitizing of the equipment and processing lines used in producing the batch, or a cross-reference to records, such as individual equipment logs, where this information is retained [21 CFR 111.260(c)];
c) The unique identifier that you assigned to each component and packaging used [21 CFR 111.260(d)];
d) A statement of the actual yield and a statement of the percentage of theoretical yield at appropriate phases of processing [21 CFR 111.260(f)];
e) The actual results obtained during any monitoring operations [21 CFR 111.260(g)];
f) The results of any testing or examination performed during the batch production, or a cross-reference to such results [21 CFR 111.260(h)];
g) Documentation that the finished dietary supplement meets specifications established in accordance with 111.70(e) and, with respect to packaging, 111.70(g) [21 CFR 111.260(i)];
h) Documentation, at the time of performance, of the manufacturing of the batch, including the initials of the person performing each step, the initials of the person responsible for weighing or measuring each component used in the batch, the initials of the person responsible for verifying the weight or measure of each component used in the batch, the initials of the person responsible for adding the component to the batch, and the initials of the person responsible for verifying the addition of components to the batch [21 CFR 111.260(j)].
i) Documentation, at the time of performance, of packaging operations, including the unique identifier that you assigned to packaging used, the quantity of the packaging used; an actual representative label, or a cross-reference to the physical location of the actual or representative label specified in the master manufacturing record; and the results of any tests or examinations conducted on packaged and labeled dietary supplements, or a cross-reference to the physical location of such results [21 CFR 111.260(k)];
j) Documentation, at the time of performance, that the quality control reviewed the BPR; approved or rejected any reprocessing or repackaging; approved and released, or rejected, the batch for distribution, including any reprocessed batch; and approved and released or rejected, the packaged and labeled dietary supplement, including any repackaged or relabeled dietary supplement [21 CFR 111.260(l)].
Additionally, you failed to prepare a BPR every time you manufacture a batch of dietary supplement, as required by 111.225(a). Specifically, according to your employee a BPR was not prepared for batch PR111.
7. Your firm failed to establish written procedures to fulfill the requirements related to product complaints as required by 21 CFR 111.553. Specifically, during the inspection, your employee indicated to our investigator that no written procedures exist at your facility for investigating product complaints.
8. Your firm failed to establish and follow written procedures for your packaging operations, as required by 21 CFR 111.403. Specifically, your employee indicated to our investigator that no written procedures exist at your facility for packaging operations. For example, you must examine, before packaging operations, packaging for each batch or dietary supplement to determine whether the packaging conform to the master manufacturing record [21 CFR 111.410(c)]. You must also implement a system to determine the complete manufacturing history and control of a packaged and labeled dietary supplement through distribution [21 CFR 111.410(d)].
9. Your firm failed to establish and follow written procedures for holding and distributing operations, as required by 21 CFR 111.453. Specifically, during the inspection, your employee indicated to our investigator that no written procedures exist at your facility for holding and distributing operations. Additionally, your firm does not routinely maintain distribution records for your finished products distributed, as required by 21 CFR 111.475(a)(2).
10. Your firm failed to establish written procedures for personnel qualification requirements as required by 21 CFR 111.8. Specifically, your employee stated that the firm does not have procedures to ensure employees are qualified to conduct job functions. Once you have established written procedures you must make and keep documentation of personnel training, including the date of the training, the type of training, and the person(s) trained, as required under 21 CFR 111.14(b)(2). Specifically, you told our investigator that your employees are trained by walking employees through the production process, but this training is not documented.
11. Your firm failed to maintain your physical plant in a clean and sanitary condition, as required by 21 CFR 111.15(b)(1). Specifically, our investigator observed product residue on production equipment and the walls and floor of the production room from a previous production run from two days prior. In addition, you failed to establish and follow written procedures for cleaning the physical plant and for pest control, as required under 21 CFR 111.16. Specifically, according to your employee, your firm does not have written procedures for cleaning the plant.
This letter is not intended to be an all-inclusive list of the violations that exist in connection with
your products. You are responsible for investigating and determining the causes of the violations identified above and for preventing their recurrence or there occurrence of other violations. It is your responsibility to ensure that your firm complies with the Act and FDA regulations.
You should take prompt actions to correct the violations noted in this letter. Failure to promptly correct these violations may result in FDA taking enforcement action without further notice, including, without limitation, seizure and injunction under section 302 and 304 of the Act [21 U.S.C. §§ 332 and 334].
Section 743 of the Act [21 U.S.C. 379j-31] authorizes FDA to assess and collect fees to cover FDA’s costs for certain activities, including reinspection-related costs. A reinspection is one or more inspections conducted subsequent to an inspection that identified noncompliance materially related to a food safety requirement of the Act, specifically to determine whether compliance has been achieved. Reinspection-related costs means all expenses, including administrative expenses, incurred in connection with FDA’s arranging, conducting, and evaluating, the results of the reinspection and assessing and collecting the reinspection fees [21 U.S.C. 379j-31(a)(2)(B)]. For a domestic facility, FDA will assess and collect fees for reinspection-related costs from the responsible party for the domestic facility. The inspection noted in this letter identified non-compliance materially related to a food safety requirement of the Act. Accordingly, FDA may assess fees to cover any re-inspection-related costs.
Please respond to this office in writing within fifteen (15) working days from your receipt of this letter. In your response, identify the steps you have taken or will take to correct the above noted violations and prevent similar ones. In your response, please include timeframes in which the corrections will be completed and provide any documentation that will effectively assist us in evaluating whether the corrective actions have been made and their adequacy. If you are unable to complete the corrective actions within fifteen (15) working days, identify the reason for the delay and the time within which you will complete the corrections.
Your written response should be sent to the U.S. Food & Drug Administration, Attn: Allison C. Hunter, Compliance Officer, at 6751 Steger Drive, Cincinnati, Ohio 45237. If you have questions, please contact Ms. Hunter at 513-679-2700, Ext. 2134 or email at allison.hunter@fda.hhs.gov.
Sincerely,
/S/
Toniette K. Williams
Acting District Director
Cincinnati District"
http://www.fda.gov/ICECI/EnforcementActions/WarningLetters/2015/ucm472299.htm
One day FDA will go after the crooks behind HJOE as well, assuming they haven't gone on the lam by then.
"Department of Health and Human Services
Public Health Service
Food and Drug Administration
Cincinnati District Office
Central Region
6751 Steger Drive
Cincinnati, OH 45237-3097
Telephone: (513) 679-2700
FAX: (513) 679-2775
September 17, 2015
Ms. Cheryl Krueger, President/Owner
Life Support Development Ltd
2818 Fisher Road
Columbus, OH 43204
Warning Letter
CIN-452082-25
Dear Ms. Krueger:
The U.S. Food & Drug Administration (FDA) conducted an inspection at your dietary supplement manufacturer and distributor, Life Support Development Ltd., located at 2818 Fisher Road, Columbus, OH on December 16, 17, 22 and 30, 2014. In addition, we reviewed your product label collected during the inspection. We also reviewed your website at https://lifesupport.com in September 2015 and determined that you take orders there for the product Life Support Hangover Relief.
Based on our inspection and subsequent review of your product labeling collected during the inspection, as well as your firm's website, we found serious violations of the Federal Food, Drug, and Cosmetic Act (the Act) and applicable regulations. You may find the Act and the FDA’s regulations through links on FDA’s home page at www.fda.gov.
Unapproved New Drug
We also have determined that Life Support Hangover Relief product is being promoted for conditions that cause the product to be a drug under section 201(g)(1)(B) of the Act [21 U.S.C. § 321(g)(1)(B)]. The therapeutic claims in your product labeling establish that the products are drugs because they are intended for use in the cure, mitigation, treatment, or prevention of disease.
Examples of claims that provide evidence that your Life Support Hangover Relief product is intended for use as a drug include:
•“Hangover Relief”
•“Tired of Hangovers? Life Support’s cutting-edge formula contains an extract from the fruit of the Japanese Raisin Tree, known specifically to aid in the recovery from alcohol intoxication.”
•(website) “Life Support can protect the liver and brain from damage …”
Your Life Support Hangover Relief product is not generally recognized as safe and effective for the above referenced uses and, therefore, the products are “new drugs” under section 201(p) of the Act [21 U.S.C. § 321(p)]. New drugs may not be legally introduced or delivered for introduction into interstate commerce without prior approval from FDA, as described in section 505(a) of the Act [21 U.S.C. § 355(a)]; see also section 301(d) of the Act [21 U.S.C. § 331(d)]. FDA approves a new drug on the basis of scientific data submitted by a drug sponsor to demonstrate that the drug is safe and effective.
Adulterated Dietary Supplement
Even if your Life Support Hangover Relief product was not an unapproved new drug, it would still be an adulterated dietary supplement under section 402(g)(1) of the Act. The inspection revealed significant violations of the CGMP requirements for dietary supplements. These violations cause your dietary supplement products to be adulterated under section 402(g)(1) of the Act [21 U.S.C.§ 342(g)(1)] in that they have been prepared, packed, or held under conditions which do not meet the Current Good Manufacturing Practice (CGMP) regulations for dietary supplements, Title 21, Code of Federal Regulations, Part 111 (21 CFR Part 111).
Specifically, our investigator observed the following significant violations:
1. Your firm failed to establish the following specifications as required by 21 CFR 111.70:
a) Identity specifications for each component that you use in the manufacture of a dietary supplement [21 CFR 111.70(b)(1)]. Specifically, your employee stated that your firm did not have specifications for incoming components;
b) Product specifications for the identity, purity, and strength, of the finished batch of the dietary supplement, and for limits on those types of contamination that may adulterate, or that may lead to adulteration of the finished batch of the dietary supplement to ensure the quality of the dietary supplement [21 CFR 111.70(e)]. Specifically, your Life Support Ingredient Breakdown that you provided to our investigator as documentation of product specifications does not contain specifications for the identity, purity, and strength of the finished batch of the dietary supplement or limits on any contaminants.
2. You failed to prepare and follow a written master manufacturing record (MMR) for each unique formulation of dietary supplement you manufacture and for each batch size, to ensure uniformity in the finished batch from batch to batch, in the manner required by 21 CFR 111.210. Though you informed our investigator that you did not have a MMR, there is evidence to suggest that you maintain documents that contain elements of an MMR. However, your MMR does not contain all the required elements; specifically:
a) The strength, concentration, weight or measure of each dietary ingredient for each batch size [21 CFR 111.210(a)];
b) An accurate statement of the weight or measure of each component to be used [21 CFR 111.210(c)];
c) A statement of theoretical yield of a manufactured dietary supplement expected at each point, step, or stage of the manufacturing process where control is needed to ensure the quality of the dietary supplement, and the expected yield when you finish manufacturing the dietary supplement, including the maximum and minimum percentages of theoretical yield beyond which a deviation investigation of a batch is necessary and material review is conducted and disposition decision is made [21 CFR 111.210(f)];
d) A representative label, or a cross-reference to the physical location of the actual or representative label [21 CFR 111.210(g)];
e) Written instructions, including specifications for each point, step, or stage in the manufacturing process where control is necessary to ensure the quality of the dietary supplement and that the dietary supplement is packaged and labeled as specified in the MMR [21 CFR 111.210(h)(1)];
f) Written procedures for sampling in the MMR and a cross reference to procedures for tests or examinations [21 CFR 111.210(h)(2)].
3. Your firm failed to follow written procedures for manufacturing operations as required by 21 CFR 111.353. Specifically, your employee provided the investigator with your “Production Procedure Outline” as documentation of your manufacturing operations; however, according to your employee, the procedure is not followed as some steps have changed and/or been omitted from production.
4. Your firm failed to establish and follow written procedures for the responsibilities of your quality control operations, including written procedures for conducting a material review and making a disposition decision, and for approving or rejecting any reprocessing, as required by 21 CFR 111.103. Specifically, your employee indicated to our investigator that no written procedures exist for your quality control operations.
Further, as a manufacturer and distributor that contracts with other entities to label packaging that your firm uses to package dietary supplements that are then distributed under your firm’s name, your firm has an obligation to know what and how labeling activities are performed so that you can make decisions related to whether your dietary supplement products conform to established specifications and whether to approve and release the products for distribution [72 Fed. Reg. 34752, 34790 (Jun. 25, 2007)]. Your firm introduces or delivers, or causes the introduction or delivery, of dietary supplement products into interstate commerce in their final form for distribution to consumers. As such, your firm has an overarching and ultimate responsibility to ensure that all phases of the production of that product are in compliance with dietary supplement CGMP requirements.
Although your firm may contract out certain operations, it cannot by the same token, contract out its ultimate responsibility to ensure that the dietary supplements it places into commerce (or causes to be placed into commerce) are not adulterated for failure to comply with dietary supplement CGMP requirements (see United States v. Dotterweich, 320 U.S. 277, 284 (1983) (explaining that an offense can be committed under the Act by anyone who has a “responsible share in the furtherance of the transaction which the statute outlaws”); United States v. Park, 421 U.S. 658, 672 (1975) (holding that criminal liability under the Act does not turn on awareness of wrongdoing, and that “agents vested with the responsibility, and power commensurate with that responsibility, to devise whatever measures are necessary to ensure compliance with the Act” can be held accountable for violations of the Act). In particular, the Act prohibits a person from introducing or delivering for introduction, or causing the delivery or introduction, into interstate commerce a dietary supplement that is adulterated under section 402(g) for failure to comply with dietary supplement CGMP requirements [21 U.S.C. §§ 342(g), 331(a)]. Thus, a firm that contracts with other firms to conduct certain dietary supplement manufacturing, packaging, or labeling operations for it is responsible for ensuring that the dietary supplement is not adulterated for failure to comply with dietary supplement CGMP requirements, regardless of who actually performs the dietary supplement CGMP operations.
Your firm must establish a system of production and process controls and implement quality control operations to ensure the quality of your dietary supplements and that the dietary supplements are packaged and labeled as specified in the master manufacturing record [21 CFR 111.55 and 111.65]. You firm must establish and follow written procedures for the responsibilities of the quality control operations [21 CFR 111.103]. The quality control personnel must ensure that your manufacturing, packaging, labeling, and holding operations ensure the quality of the dietary supplement and that the dietary supplement is packaged and labeled as specified in the master manufacturing record [21 CFR 111.105]. Further, you must have documentation of the quality control personnel review and approval of release for any packaged and labeled dietary supplement [21 CFR 111.127(h) and 111.140(b)(2)].
5. Your firm failed to collect and hold reserve samples of each lot of packaged and labeled dietary supplements that you distribute, as required by 21 CFR 111.83(a). Specifically, according to your employee, your firm did not collect and hold reserve samples for production lots 150, 156 and166.
6. Your batch production records (BPRs) do not include complete information relating to the production and control of each batch as required by 21 CFR 111.255(b). Specifically, we reviewed your BPRs for batches PR108, PR110, PR112 and PR113 of your Life Support Hangover Relief supplement. These BPR’s do not include the following information that is required by 21 CFR 111.260:
a) The identity of the equipment and processing lines used in producing the batch [21 CFR 111.260(b)];
b) The date and time of the maintenance, cleaning and sanitizing of the equipment and processing lines used in producing the batch, or a cross-reference to records, such as individual equipment logs, where this information is retained [21 CFR 111.260(c)];
c) The unique identifier that you assigned to each component and packaging used [21 CFR 111.260(d)];
d) A statement of the actual yield and a statement of the percentage of theoretical yield at appropriate phases of processing [21 CFR 111.260(f)];
e) The actual results obtained during any monitoring operations [21 CFR 111.260(g)];
f) The results of any testing or examination performed during the batch production, or a cross-reference to such results [21 CFR 111.260(h)];
g) Documentation that the finished dietary supplement meets specifications established in accordance with 111.70(e) and, with respect to packaging, 111.70(g) [21 CFR 111.260(i)];
h) Documentation, at the time of performance, of the manufacturing of the batch, including the initials of the person performing each step, the initials of the person responsible for weighing or measuring each component used in the batch, the initials of the person responsible for verifying the weight or measure of each component used in the batch, the initials of the person responsible for adding the component to the batch, and the initials of the person responsible for verifying the addition of components to the batch [21 CFR 111.260(j)].
i) Documentation, at the time of performance, of packaging operations, including the unique identifier that you assigned to packaging used, the quantity of the packaging used; an actual representative label, or a cross-reference to the physical location of the actual or representative label specified in the master manufacturing record; and the results of any tests or examinations conducted on packaged and labeled dietary supplements, or a cross-reference to the physical location of such results [21 CFR 111.260(k)];
j) Documentation, at the time of performance, that the quality control reviewed the BPR; approved or rejected any reprocessing or repackaging; approved and released, or rejected, the batch for distribution, including any reprocessed batch; and approved and released or rejected, the packaged and labeled dietary supplement, including any repackaged or relabeled dietary supplement [21 CFR 111.260(l)].
Additionally, you failed to prepare a BPR every time you manufacture a batch of dietary supplement, as required by 111.225(a). Specifically, according to your employee a BPR was not prepared for batch PR111.
7. Your firm failed to establish written procedures to fulfill the requirements related to product complaints as required by 21 CFR 111.553. Specifically, during the inspection, your employee indicated to our investigator that no written procedures exist at your facility for investigating product complaints.
8. Your firm failed to establish and follow written procedures for your packaging operations, as required by 21 CFR 111.403. Specifically, your employee indicated to our investigator that no written procedures exist at your facility for packaging operations. For example, you must examine, before packaging operations, packaging for each batch or dietary supplement to determine whether the packaging conform to the master manufacturing record [21 CFR 111.410(c)]. You must also implement a system to determine the complete manufacturing history and control of a packaged and labeled dietary supplement through distribution [21 CFR 111.410(d)].
9. Your firm failed to establish and follow written procedures for holding and distributing operations, as required by 21 CFR 111.453. Specifically, during the inspection, your employee indicated to our investigator that no written procedures exist at your facility for holding and distributing operations. Additionally, your firm does not routinely maintain distribution records for your finished products distributed, as required by 21 CFR 111.475(a)(2).
10. Your firm failed to establish written procedures for personnel qualification requirements as required by 21 CFR 111.8. Specifically, your employee stated that the firm does not have procedures to ensure employees are qualified to conduct job functions. Once you have established written procedures you must make and keep documentation of personnel training, including the date of the training, the type of training, and the person(s) trained, as required under 21 CFR 111.14(b)(2). Specifically, you told our investigator that your employees are trained by walking employees through the production process, but this training is not documented.
11. Your firm failed to maintain your physical plant in a clean and sanitary condition, as required by 21 CFR 111.15(b)(1). Specifically, our investigator observed product residue on production equipment and the walls and floor of the production room from a previous production run from two days prior. In addition, you failed to establish and follow written procedures for cleaning the physical plant and for pest control, as required under 21 CFR 111.16. Specifically, according to your employee, your firm does not have written procedures for cleaning the plant.
This letter is not intended to be an all-inclusive list of the violations that exist in connection with
your products. You are responsible for investigating and determining the causes of the violations identified above and for preventing their recurrence or there occurrence of other violations. It is your responsibility to ensure that your firm complies with the Act and FDA regulations.
You should take prompt actions to correct the violations noted in this letter. Failure to promptly correct these violations may result in FDA taking enforcement action without further notice, including, without limitation, seizure and injunction under section 302 and 304 of the Act [21 U.S.C. §§ 332 and 334].
Section 743 of the Act [21 U.S.C. 379j-31] authorizes FDA to assess and collect fees to cover FDA’s costs for certain activities, including reinspection-related costs. A reinspection is one or more inspections conducted subsequent to an inspection that identified noncompliance materially related to a food safety requirement of the Act, specifically to determine whether compliance has been achieved. Reinspection-related costs means all expenses, including administrative expenses, incurred in connection with FDA’s arranging, conducting, and evaluating, the results of the reinspection and assessing and collecting the reinspection fees [21 U.S.C. 379j-31(a)(2)(B)]. For a domestic facility, FDA will assess and collect fees for reinspection-related costs from the responsible party for the domestic facility. The inspection noted in this letter identified non-compliance materially related to a food safety requirement of the Act. Accordingly, FDA may assess fees to cover any re-inspection-related costs.
Please respond to this office in writing within fifteen (15) working days from your receipt of this letter. In your response, identify the steps you have taken or will take to correct the above noted violations and prevent similar ones. In your response, please include timeframes in which the corrections will be completed and provide any documentation that will effectively assist us in evaluating whether the corrective actions have been made and their adequacy. If you are unable to complete the corrective actions within fifteen (15) working days, identify the reason for the delay and the time within which you will complete the corrections.
Your written response should be sent to the U.S. Food & Drug Administration, Attn: Allison C. Hunter, Compliance Officer, at 6751 Steger Drive, Cincinnati, Ohio 45237. If you have questions, please contact Ms. Hunter at 513-679-2700, Ext. 2134 or email at allison.hunter@fda.hhs.gov.
Sincerely,
/S/
Toniette K. Williams
Acting District Director
Cincinnati District"
http://www.fda.gov/ICECI/EnforcementActions/WarningLetters/2015/ucm472299.htm
"It is difficult to get a man to understand something, when his salary depends upon his not understanding it."
Upton Sinclair
"Nobody ever went broke underestimating the intelligence of the American public."
H. L. Mencken
Join the InvestorsHub Community
Register for free to join our community of investors and share your ideas. You will also get access to streaming quotes, interactive charts, trades, portfolio, live options flow and more tools.