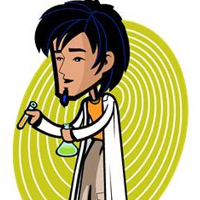
Thursday, June 11, 2015 10:15:55 AM
This is a work in progress that a few of you have known that I am working on. Was posted to the less widely read SI site on Tuesday night. This should be viewed as a draft, if a fairly together one - and as a description that I plan on modifying and attempting to post somewhere like Seeking Alpha once I figure out how to address some comments that I got back from their editorial staff when they reviewed it on Tuesday:
It is a description of what I saw, and some idea of what I think it all means, at the Shelton plant during the week of May 26. It's long,.... but I hope mostly organized and worth the read. My thanks to those few others of you who have read and commented on earlier versions of this as I got it assembled.
The credit - or blame for what is written here - is all mine and is my opinion and understanding of where we currently stand.
----------------------------------------------------------------------
As a long shareholder of NanoViricides(NNVC, NYSE MKT), I have watched with interest as the company has begun to take significant steps forward to finally becoming a clinical stage bio-pharma company. One of the most significant of these steps has been the identification of, purchase of, remodeling of, and equipping of their pilot-plant in Shelton CT. Once all phases of the structure are online and certified, NNVC will have the capability to produce their anti-viral compounds in sufficient quality and quantity to carry the company forward into commercial production.
Work to identify a location for this pilot-plant has been in the works since at least sometime during 2011. The 18,000 square foot building at 1 Controls Dr. in Shelton, CT was first purchased by Dr. Diwan, current Chairman and President of NNVC (via his Inno-Haven LLC) in 2011. Engineering, design and renovations were conducted on the structure to meet the growing production needs of NNVC to develop and insure quality for their antiviral compounds generally known as nanoviricides(or 'Cides for short). After extensive planning, some fits and starts, and what seemed like a never-ending period (especially to shareholders)of planning, construction and testing - a certificate of occupancy for that facility was finally issued in June 2014. The finished plant was sold by Inno-Haven LLC to NNVC at an audited, at-cost price estimate during January 2015. A timeline for this process is available via press releases found at the NNVC corporate website, and I will not discuss these events in any additional detail.
Facility validation and some remaining specific modifications have been undertaken by NNVC to the Shelton facility since the June 2014 occupancy certificate. Shareholders and the general public had the opportunity to view this facility before many of these additional modifications and upgrades were online during the Grand Opening of that facility held during July of 2014. I was not among those who could attend the Grand Opening due to scheduling conflicts. However, I and a few other shareholders were given the opportunity to tour the Shelton facility during the last week of May, 2015. The remainder of this article will seek to review and relate some of what I saw and learned about this new plant and its potential to help elevate NNVC into the successful clinical-stage pharma that it can be.
Office space, desk-space, current occupancy, and staffing:
Before being allowed to enter past the vestibule of the facility, all staff and visitors are issued a set of disposable shoe covers, and a hairnet. All staff & visitors must wear these at all times while in the building, and these precautions are taken even for those only entering the office spaces. The laboratory is a combination of Class 10,000 R&D, and a Class 100 production laboratory space that possesses a filtered air system designed to limit airborne particulates throughout the facility. This set of precautions is taken in an effort to minimize the chances of introducing environmental contamination in the more vital laboratory work areas.
We were informed that there were 25 total employees working in the combined facilities of Shelton, and the old R&D facilities nearby, as of as of the tour date. Of these 25, not all have had their positions and equipment transferred over to the Shelton facility from the old R&D facility. I have not seen the old facility, and thus cannot assess the degree of similarity or difference between the old and new and will not attempt to do so. On the day that I took the tour, I at least briefly met 8-9 of the people on the Shelton staff, and there were an additional few employees that I didn't get a chance to meet. Dr. Seymour (CEO of NNVC) indicates that there are at present 3 total employees of NNVC; himself, the CFO Ms. Meeta Vyas, and one other. Ms. Vyas was also present for part of that day, and I had the pleasure of meeting her. The remaining staff at the Shelton facility, and for the older R&D facility, is composed of TheraCour Pharma Inc. employees that are involved in R&D and in process development for the 'Cides to meet NNVC's needs. TheraCour is a privately held company headed by Dr. Diwan that has licensed the technology to NNVC that is being developed into clinical anti-viral treatments (the 'Cides).
There are 4-5 full size offices facing out the front of the Shelton building and a moderate-sized lunch and coffee break area on the north side of the building. There are additional sets of desks for people working in the labs set on the outside walls of the main R&D lab space that are partitioned off from that lab space with full walls and doors. We were told by Dr. Diwan that there is desk space for 40-50 people in the facility. There is plenty of desk space for additional staff, even once the current set of 25 employees have all moved into the Shelton facility, and once the facility can be regarded as fully functional and the remaining open positions have been filled. Dr. Diwan also indicated they were still regularly (every week or so) interviewing qualified candidates to fill currently vacant positions needed to continue scale-up and product development.
The Class 10,000 laboratory space
This is the segment of this document where I think there is the most information to convey, as it is the portion of the facility most occupied, online, and in use as of the date of the tour.
See a source like http://www.cemag.us/articles/2014/03/understanding-cleanroom-classifications for a full outline of the specifications of cleanroom facilities and designations as that is outside the scope of this article. I also will not discuss the differences and similarities of the topics Good Laboratory Practices and Good Manufacturing Practices as they are outside the scope of this article. For those interested in reviewing these criteria and how they will apply to NNVC/TheraCour as the potential products move forward I would recommend a review of any of a number of FDA documents discussing those terms and what they include ( http://www.fda.gov/). Suffice it to say for my purposes in the article is that GMP, GLP and Cleanroom designations and guidelines do not equate to one another on a one-to-one basis, or in any combination.
Ordinary room air is approximately Class 1,000,000 (Federal Standard 209E, or FS-209E) rated which is correlated with the number of measurable particles of given sizes found in one cubic foot of air. The R&D portion of the lab facility is at Shelton is rated as a Class 10,000 work area. The facility also contains a Class 100 work areas (I will discuss these in more detail in a later section) that will be used to manufacture 'Cides for internal use in Clinical Trials, and that will be used for initial production once NNVC enters that phase after completing clinical testing.
However, reaction scale-up optimizations, reagent preparations, QC, and preparing the materials needed to complete toxicity (TOX) testing for IV (Intravenous) FluCide can each be done to completion in the Class 10,000 areas of the facility, and do not need to be accomplished using the Class 100 section of the facility. IV FluCide is the anti-viral compound that is NNVC's current pipeline leader.
We entered the Class 10,000 portion of the lab from the office-space area via a vestibule designed to help limit inflow of outside air into the lab facility. Those entering this segment of the lab facility all enter into the vestibule, doors are closed behind them, and the air inside the vestibule is briefly filtered through an air exchange system to limit the entry of new particles with those entering the workspace. Once air is sufficiently exchanged, doors on the other side of the vestibule can be opened to allow entry. The process is reversed to exit the Class 10,000 lab.
The main lab itself is spacious, well lit, and has sets of bench-tops with an appropriate quantity and quality of power and utility outlets, several sets of bench-top chemical fume hoods, and several reach-in bench-top Class II sterile work areas. These chemical fume hoods are sufficiently large that smaller sets of bioreactors (1 L to a few L capacity) can easily fit inside of them. While we were doing our walk-through some of these fume hoods were in use by members of the staff- where they monitored reactions, and added ingredients to reactions that were in progress. The current laboratory space is not nearly used at capacity at present -less than a third of the workspaces in that room were in use that day. Keep in mind that with a capacity of 40-50 people on staff at peak, but only about a dozen people working on site- one should expect noticeable unused capacity in the lab at this point. My comment here is not intended as some criticism of wasted or excess space, but as a reflection of that fact.
A set of larger chemical fume hoods, and larger Class II workspace designed to fit 30 L and 50 L bioreactors were in a separate room next to the first lab space we entered. The largest of these fume hoods and Class II spaces are sufficiently large that a person can enter them standing up. These work spaces have sufficient clearance for these larger reaction vessels, clearance for their top-mounted motors, and for the rolling mounts that they must be kept on in order to be moved. These larger hoods have recessed ports with their own airflow restrictors to permit hook up of water supplies for maintaining reaction temperatures in the bioreactors and for the needed power to run the motors. Once reaction scale-up is completed, the larger yield reactions needed to make the remaining TOX materials to send off to BASi (BioAnalytical Systems, Inc, NASDAQ) will be conducted in that room and in those hoods. BASi is the laboratory contracted to complete the independent TOX testing of IV FluCide.
There was one member of staff working in that room in one of the smaller chemical fume hoods also located there preparing reagents in a 4 L sized bioreactor. However, no work was being done in the spaces for the larger bioreactors on that workday.
There is a small, separate adjoining room for clean-up of bioreactors once a reaction cycle is completed so that the vessels can be effectively cleaned and reused for later sets of reactions.
In general - the Class 10,000 workspace appears well laid out, clean, organized, has plenty of available workspaces, power and water hook-ups, and should provide the needed space and resources to continue scale-up procedures in the short to medium-term. As the staff at the Shelton plant continues to expand, this lab should also provide more than adequate R&D workspaces for further development of 'Cides against other viruses; even once production of larger batches of GLP and GMP compliant FluCide are well under way at Shelton. I hope to get the opportunity to see this lab in action once it is fully staffed and once the company has taken the next steps to place the Class 100 laboratory space into use making materials needed for Clinical studies of IV FluCide.
The Class 100 laboratory space
We entered the Class 100 portion of the lab from the Class 10,000 lab area via another vestibule designed to help limit inflow of outside air into that clean lab facility. As with entry to the Class 10,000 area - those entering the lab facility enter into a vestibule, doors are closed behind them, and the air inside the vestibule is briefly filtered through an air exchange system to limit the entry of new particles with those entering. Once air is given a chance to be effectively exchanged, doors on the other side of the vestibule are opened to allow entry. The process is reversed to exit the Class 100 lab, and there is no direct access to the other regions of the facility from the Class 100. This will help to maintain the cleanroom conditions inside that space once it is in use operationally.
Additionally, once the Class 100 work area is active and in use for production, staff with work to do in that segment of the lab will be required to shower, change into scrubs and other specific cleanroom protection, and only then will be allowed to enter the space. Similarly, those garments will need to be removed and the individuals shower out to exit. The fact that the Class 100 area is not currently in use was one of the reasons that us outsiders could get a look at it from the inside. Access to this section will be much more restricted once manufacturing is going on in there, and when maintaining the purity of the working environment becomes a premium.
There is much less to relate at this point about activities inside the Class 100 area, than on the Class 10,000 side since the Class 100 area is not currently in use for production. The Class 100 section will also not be used as an R&D lab when it is active and running under full cleanroom protocols. The workspace in the Class 100 area, while smaller than that in the Class 10,000 area, is similarly laid out and equipped with chemical fume hoods and class II workspaces. The Class 100 lab also has walk-in sized chemical fume hoods and Class II work areas sized for the larger bioreactors with the same sorts of recessed ports power and water hook ups as seen in the Class 10,000 segment of the facility. This standardization should allow reaction protocols and processes developed in the Class 10,000 portions of the facility to be seamlessly moved into the Class 100 portion of the facility once that level of manufacturing purity is required.
While on the tour - Dr. Diwan and his staff described several of the processes and procedures that are going to be put into place to maintain GLP and GMP standards. Chemicals used inside the production facility must be assayed prior to use, and the results of those assays properly documented before those batches of chemicals & raw materials are allowed to be used inside the Class 100 facility. Assayed batches of chemicals will be kept at the entrance to the work area, and moved in only into the Class 100 area as needed quantities for given protocols. The reagents for individual reactions will be weighed/measured out, placed into transport containers, those containers surface disinfested and cleaned, and then passed into the Class 100 area through airlocks built into the lab walls. Similarly - finished materials will be moved out of the Class 100 area in sealed containers, through a different set of 'exit only' airlocks.
GLP and GMP standards are primarily concerned with documentation of protocols, documentation of tests and standards, and regular audits of those doing the procedures. The structure and layout of the facility was designed in large part to aid NNVC in making sure that documentation and processes are done properly. So that when the time comes to get FDA certifications of GLP/GMP for their facility, that process is deeply ingrained in both the developed facility workflow and in the minds of the staff working there. These protocols are not yet in place - but we were assured that documentation is already well under way, and by the time the Class 100 section is needed, the staff will be prepared, the protocols, procedures, and training will be done, and the process will part of the culture there.
One other interesting space within this Class 100 area I was not expecting to see was a small set of rooms being set up for culturing and maintaining cell culture lines. This room already has a CO2 incubator in palace and will function as a Class II/III containment area. The significance of this particular operation being set up in the Shelton facility was immediately obvious to me.
Early in efficacy testing, many of the assays for assessing potential efficacy of new prospective nanovirucides test these compounds against live viruses that are infecting cultured cell lines. The advantage to having such a capacity at the Shelton facility is that many early optimization tests can be done rapidly, with replication, and in a very small space, to quickly weed out obviously ineffective drug candidates.
One of the recurring difficulties that NNVC has had in getting initial testing of candidate 'Cides done is that they have been completely dependent on that initial testing being done in outside laboratories where NNVC is at the mercy of the resources and schedules of those outside laboratories. Although the small facility being set up at Shelton will have some significant limitations as to what can, and what cannot, be worked on for safety or quarantine reasons, this small facility could be a very useful asset for the facility to have on site for at least some viruses. More extensive testing than can be conducted in this small workspace, testing that has significant risk for human mortality or morbidity, and all animal testing will still have to be done with a collaborator who possesses the needed facilities, expertise, and permits. However, early stages of testing and modification of candidate ligands and compounds could be expedited nicely for use for at least some viruses once this capacity is ready. This should be viewed as a distinct improvement of NNVC's future over the process they are required to follow currently.
Analytical Chemistry lab
We then exited the Cleanroom sections of the lab, and entered a large, well organized, and partially equipped Analytical Chemistry lab. It's a large room, with what appears to be ample bench space, power access, a very nice set of windows facing out through the front of the facility, and a large assortment of instruments that will be needed to assess chemical composition of reactants and products needed for QC as production goes forward. The area is still a work in progress - in that not all of the equipment that will be needed to do the needed QC and analyses is in place as of this site visit, and the staff to do the work there is still being recruited.
Among the instruments, I noticed an apparatus designed to measure particle sizes by assessing the light scattered when it passes through a solution containing them. There was a variety of chromatography equipment that will be needed for separating chemical components in reactions, assessing their purity, and confirming chemical structures. There were also machines with ion exchange columns and, what appeared to be, at least one mass-spectrometer.
Dr. Diwan used part of this time to explain to those of us on the tour how some of the time and delays in getting this part of the facility fully operational had occurred. As individual pieces of equipment arrive, they must first make appointments with technical staff with the manufacturer to do an unpacking and inventory to ensure that what was ordered is what was received and is also what is actually needed to do an job. Then a separate appointment has to be made to get it set up and calibrated by other techs working for that manufacturer. Then finally at least a couple members of the staff at Shelton have to attend short (a few days or less) training sessions in using and maintaining that piece of equipment. The company needs to ensure that more than one employee is capable of running each piece of equipment for what I hope are obvious reasons - redundancy is always a good thing in a business where individuals get sick, take vacations, or on occasion, take other positions.
I will be interested in getting another look at this room and its equipment in future visits to see this and the staff in action once it is fully equipped.
This essentially ended the tour. We exited the facility for a bit of a late lunch and had a continuing discussions of what we had seen, how this all fits together - now, and in the long-run, and what are anticipated next steps for FluCide, and for the candidate HerpesCide, DengueCide, and other products in NNVC preclinical the pipeline.
Mechanical Spaces and General Assessments of the Facility and Staff.
We did get a quick view of one of the main mechanical rooms - and other than noting that I didn't see anything unusual. There isn't much else to be said about it. All of these pieces of infrastructure equipment are located with access through an external wall with separate access points outside of the lab spaces so that they can be readily serviced by technicians when needed without generally having to enter the cleaner portions of the facility. We did not see the air handling systems and most of the air filtration systems as they were located outside of the building and on the roof.
The staff members that I interacted with during the visit were generally friendly and forthcoming with information in at least in general terms. They all seemed to enjoy working there, working as part of the team, and freely talked with us visitors, and with Drs. Diwan and Seymour. Those I interacted with for more than just a few words were bright, seemed ready to answer most questions, and did not appear apprehensive about interacting with us 'outsiders'.
The lab itself remains a work in progress - but it appears that the essential pieces for what they are actively focused on doing at the Shelton site now (TOX preparations, R&D, and scale-up functions) are in place. Other pieces will be gradually gaining more functionality and, barring unforeseen circumstances, should be coming online before they are needed. The infrastructure needed to run the place including power, water supplies, fire suppression systems, air handlers, benches, areas needed to do chemical syntheses, airlocks, and workspaces are all there and functioning. The staff is expanding, and the capabilities of the staff will be expanding accordingly as those gaps get filled by qualified people.
In conclusion - while there is still hard work ahead for NNVC - the pieces needed to get that work done are nicely falling into place. Risks remain - as they do with all pre-revenue tech companies, but these risks are now relatively easy to define for NNVC. There are fewer 'unknown unknowns' remaining in process development. Once the team has overcome their remaining problems in scaling up to Kg quantities of their 'Cides, the logjam blocking forward progress with their pipeline of antiviral products should cease to be a concern, and the single biggest risk factor facing NNVC at present ceases to be a risk factor.
Disclaimers:
drkazmd65 has earned a Ph.D. in Genetics and possesses over 20 years working experience post-degree in genetics, biological chemistry, molecular genetics, population genetics, and in methods development and validation. drkazmd65 has been long in NNVC since 2009, and has periodically added to his holdings in NNVC since that entry point. drkazmd65 has not taken any new positions (buying or selling) with his NNVC holdings since a few weeks prior to the site visit that is related in this article, but he intends to opportunistically continue to accumulate NNVC in the near future.
“The two most powerful warriors are patience and time.”
- Leo Nikolaevich Tolstoy
Recent NNVC News
- NanoViricides Reports that the Phase I NV-387 Clinical Trial is Completed Successfully and Data Lock is Expected Soon • InvestorsHub NewsWire • 05/02/2024 02:07:42 PM
- Form 8-K - Current report • Edgar (US Regulatory) • 02/16/2024 09:53:32 PM
- Form 10-Q - Quarterly report [Sections 13 or 15(d)] • Edgar (US Regulatory) • 02/14/2024 09:55:35 PM
- Form 8-K - Current report • Edgar (US Regulatory) • 01/19/2024 09:44:48 PM
- Form DEF 14A - Other definitive proxy statements • Edgar (US Regulatory) • 12/04/2023 09:08:49 PM
- Form 10-K - Annual report [Section 13 and 15(d), not S-K Item 405] • Edgar (US Regulatory) • 10/13/2023 08:30:41 PM
- Form NT 10-K - Notification of inability to timely file Form 10-K 405, 10-K, 10-KSB 405, 10-KSB, 10-KT, or 10-KT405 • Edgar (US Regulatory) • 09/28/2023 08:44:54 PM
- Form 8-K - Current report • Edgar (US Regulatory) • 09/01/2023 08:46:45 PM
Duane Forrester Joins INDEXR as SVP of Search • MONI • Jul 31, 2024 11:46 AM
Lingerie Fighting Championships Help Fulfill Death-Bed Promise With First Major Motion Picture • BOTY • Jul 31, 2024 9:00 AM
Kona Gold Beverage Significantly Reduces Debt from Multiple Holders • KGKG • Jul 31, 2024 9:00 AM
Avant Technologies Opens Equity Line with GHS Investments as Company Explores Expansion into Additional Technologies • AVAI • Jul 30, 2024 8:00 AM
ELEMENT79 GOLD CORP PROVIDES UPDATE ON CHACHAS COMMUNITY CHARTER AND REVENUE GENERATION, M&A ACTIVITIES • ELMGF • Jul 30, 2024 8:00 AM
INDEXR AI Merges With Moon Equity Holdings Corp. (MONI), Creating a Leading-edge Technology Company • MONI • Jul 29, 2024 9:59 AM