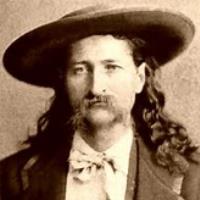
Thursday, August 21, 2014 8:02:41 PM
A Portland facility that turns hard-to-recycle plastics into crude oil will be shuttered while owner Waste Management explores newer technology options.credit: Courtesy of Waste Management
A Portland facility that turns hard-to-recycle plastics into crude oil will be shuttered while owner Waste Management explores newer technology options. | credit: Courtesy of Waste Management
Waste Management plans to idle its new plastics-to-oil facility in North Portland.
It’s only been operating for 16 months, but perhaps not as well as the company had hoped.
The plant takes hard-to-recycle plastics and turns them into crude oil using technology developed by the Beaverton, Oregon, company Agilyx. The process essentially gasifies the plastic, purifies and condenses it. You can read more about the process here.
It’s an alternative, eco-friendly path for dirty and mixed-material plastics that are rejected by traditional recycling facilities because they contaminate the recycled plastic. The resulting crude oil produced can be refined into gasoline, low-sulfur diesel, inks and new plastics.
The Portland facility has been utilizing things like the film plastic used to wrap pallets for transportation, tarps used to cover farm crops, pots from plant nurseries and greasy containers from industrial sites.
And according to Waste Management spokeswoman Jackie Lang, the plant has been successful in turning that material into crude oil. But the company is holding out for a more efficient version of the technology. The plant is currently using what Agilyx calls Generation 5, but now there’s a Generation 6 that looks better.
“We’ve decided to discontinue plant operations while Agilyx advances the next generation of its process,” Lang said. “We will be exploring retrofitting the plant with the Generation 6 technology.”
In the meantime, 22 people who work at the plant will be laid off.
Lang said the older technology requires technicians to move materials through a multi-step process that “involved significant manual labor and high energy input.” In contrast, she said, “Generation 6 is a continuous system designed to be more automated and more cost effective.”
I asked Lang if the current technology at the plant isn’t cost effective. She dodged the question, answering it this way:
“What we know now is that Generation 6 is more promising in terms of being more energy efficient and more automated and more cost effective.”
Lang said the things her company learned from its first go-round with plastic-to-crude recycling is helping shape the newer technology it plans to use when it resumes the effort.
The Portland plant was designed to process 40 tons of plastic a day and produce 1.5 million gallons of crude oil annually. According to Waste Management, it takes about nine pounds of plastic to make one gallon of crude oil.
—Cassandra Profita
http://earthfix.opb.org/energy/article/turning-plastics-to-oil-in-portland-maybe-later/
Hydromer, Inc. Reports Preliminary Unaudited Financial Results for First Quarter 2024 • HYDI • Apr 29, 2024 9:10 AM
Avant Technologies to Implement AI-Empowered, Zero Trust Architecture in Its Data Centers • AVAI • Apr 29, 2024 8:00 AM
Bantec Reports an Over 50 Percent Increase in Sales and Profits in Q1 2024 from Q1 2023 • BANT • Apr 25, 2024 10:00 AM
Cannabix's Breath Logix Alcohol Device Delivers Positive Impact to Private Monitoring Agency in Montana, USA • BLO • Apr 25, 2024 8:52 AM
Kona Gold Beverages, Inc. Announces Name Change to NuVibe, Inc. and Initiation of Ticker Symbol Application Process • KGKG • Apr 25, 2024 8:30 AM
Axis Technologies Group and Carbonis Forge Ahead with New Digital Carbon Credit Technology • AXTG • Apr 24, 2024 3:00 AM