Followers | 154 |
Posts | 15663 |
Boards Moderated | 4 |
Alias Born | 01/30/2007 |
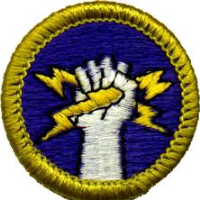
Wednesday, June 04, 2014 6:52:10 AM
http://ih.advfn.com/p.php?pid=nmona&article=62442561
The Company had to shut down its production late in the fourth quarter of 2013 due to severe cold weather that caused damage to condensers and other components of our processors. Management estimates that the repair of the processors will require the expenditure of between $175,000 and $200,000. At June 3, 2014, we lacked the working capital or access to bank credit to make these repairs.
We had to shut down its production in the fourth quarter of2013. Management estimates bringing the facility back into full production will require the expenditure of between $175,000 and $200,000. The plant is presently testing and evaluating the feedstock from potential purchasers of processors. At June 3, 2014, we lacked the working capital or access to bank credit to restore full production. The 2013 shut downs was driven by the following items.
?
Unseasonably cold temperatures in the winter of 2013/2014 . The temperature in winter 2013 was far below what we had ever operated through, with some periods sustaining below zero Fahrenheit temperatures. This low temperature caused many local issues with off-the-shelf diesel freezing and gelling. Our Fuel Oil #6 meets ASTM D396 fuel standards which include a pour point (or freezing point) of -6 C pour point (21° F). The temperature often dropped below 5°F and at some periods below 0°F. These unseasonably cold temperatures and high winds froze our fuel and in some places our new water lines. We experimented with pour point depressants used in diesel for artic temperatures. After testing and verifying compatibility and functionality, we secured a good pour point depressant that will allow our fuel to flow at temperatures down to -30°C or -22°F. Subsequently to the weather damage and condenser failure (see below), we idled our processors in late December 2013. We also temporarily reduced our operation and fabrication work force in January 2014. We repaired temperature damage from the 2013/2014 winter in the spring of 2014. We replaced the new condensers on Processor #3 with condensers that have historically never failed in the process. We are adding equipment to our facility support systems to inject additives for lubricity and pour point to meet off road diesel use. The additives we tested performed well in off-road diesel equipment and the pour depressant is tested to work in extremely cold temperatures.
?
The failure of new condensers installed throughout the plant of 2013/2014 . We use a device called a condenser to cool hot liquids or heat cold liquids. Numerous condensers are located throughout a processor and plant. Our legacy condensers were performing well over the past few years however there were different sizes and manufacturers used. This posed lead time problems and higher costs when sourcing parts for future sales. In the spring of 2013, we standardized, acquired and installed new condensers for cooling to standardize all condensers across the factory. We also designed, procured, and installed central plant support systems for our processors including: centralized water chilling and storage, centralized gas compression for collect, compress and distribute off-gas generated by processors, centralized hot oil system for cooling high temperature fluids, and developed a site control system to monitor all of the auxiliary plant support systems. In late December 2013, the new condensers installed across the plant and in the processors began to fail. Over a six week period, all the new condensers failed in operation. Upon reviewing the failure in the condenser, we found the stitch welding used to manufacture them was defective. Management believes we have developed a comprehensive front-line QC procedure to ensure plastic is not littered tools, steel or bad fillers. All new vendor equipment must be tested on our R&D system, Processor#1, before deploying on other processors. This will mitigate the risk of poor quality components from being sources or installed without significant testing.
27
?
Bad heat transfer fluid (HTF). In 2013, the Company was permitted to run used heat transfer liquid HTF, such as used oils, in the process. This involved a significant learning curve to develop testing protocols to determine if the liquid being received is in fact used heat transfer liquid. The permit and procedures describe numerous tests that must be conducted to ensure the HTF does not contain hazardous chemicals. Some unscrupulous suppliers will attempt and sell or deliver emulsions or other liquid products that look like HTF but are in fact not. After 2 months of operating HTF from a variety of sources, management was able to develop testing methods to determine if the HTF was in fact 100% HTF.
?
Other causes of significant downtime issues in 2013.
o
Bad material in waste Plastic. The Company has developed a comprehensive front-line QC procedure to ensure plastic is not littered tools, steel or bad fillers.
o
Water & snow in waste plastic. The Company has developed a comprehensive front-line testing procedure to stop large amounts of water from being fed into the process.
o
Emergency Shutdowns. Several emergency plant shutdowns for plant evacuations due to other local adjacent factories having serious fires or emergency releases. The Company installed a plant evacuation system and developed a better protocol to halt the processor when having to evacuate the site due to external factors.
o
Installation of new facility subsystems for Processors #1,#2 & #3 to eliminate downtime from old systems.
o
Installation of Processor #3 which is now operational.
o
Routine maintenance & shutdown.
MLM playing White: Queen sacrifice bait and mate in 7
The Chess Board http://investorshub.advfn.com/boards/board.aspx?board_id=14740
Glidelogic Corp. Becomes TikTok Shop Partner, Opening a New Chapter in E-commerce Services • GDLG • Jul 5, 2024 7:09 AM
Freedom Holdings Corporate Update; Announces Management Has Signed Letter of Intent • FHLD • Jul 3, 2024 9:00 AM
EWRC's 21 Moves Gaming Studios Moves to SONY Pictures Studios and Green Lights Development of a Third Upcoming Game • EWRC • Jul 2, 2024 8:00 AM
BNCM and DELEX Healthcare Group Announce Strategic Merger to Drive Expansion and Growth • BNCM • Jul 2, 2024 7:19 AM
NUBURU Announces Upcoming TV Interview Featuring CEO Brian Knaley on Fox Business, Bloomberg TV, and Newsmax TV as Sponsored Programming • BURU • Jul 1, 2024 1:57 PM
Mass Megawatts Announces $220,500 Debt Cancellation Agreement to Improve Financing and Sales of a New Product to be Announced on July 11 • MMMW • Jun 28, 2024 7:30 AM