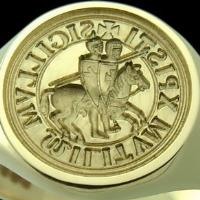
Friday, February 13, 2009 11:04:11 AM
(Previously posted business news article excerpts below)
"...Natural gas operators are examining water recycling as a method to curtail their water usage and demand, but current technology still renders the process less economical than the alternative of simply disposing of the post-drilling, contaminated fluid.
About 3.75 million gallons of water are used for each natural gas well, and what fluid doesn’t remain – or disappear – underground is recaptured either as flow-back water or produced water, both of which are chloride contaminated and need to be managed.
Traditionally, both fluids are inspected in saltwater disposal wells that send the fluids into underground rock formations, where they remain. There are more than 50,000 disposal wells across Texas that serve the more than 216,000 gas wells in the state, according to the Railroad Commission of Texas, which regulates the industry’s subsurface water use.
The saltwater disposal wells are controversial, however, because detractors argue the highly corrosive water could escape and pollute city-used water tables. In October 2007, the Fort Worth City Council enacted a moratorium on these wells, due to expire April 30. However, the city council is expected to extend the measure. Transporting the fluids to these wells is also expensive, representing one of the major costs gas operators incur during the process.
Washing the water
Oklahoma-based Devon Energy Corp. has used a Canadian water treatment technology since 2005 to reclaim and recycle some of the flow-back water and some of the produced water. Devon’s nine mobile heated distillation units, or NOMADs, reclaim and recycle about 24 percent of the 3.5 million gallons of water used during the fracing processes.
The NOMAD systems are designed and built by Aqua-Pure Ventures Inc., based in Calgary, Alberta, Canada, and operated by Granbury-based Fountain Quail Water Management, a subsidiary of Aqua-Pure. In short, the NOMADs use an evaporator and a compressor to treat waters up to saturation, or about 40,000 total dissolved solids, recycling about 80 percent of the inlet water.
“What we’re doing is boiling off the steam, and as the steam evaporates it’s ‘pured,’” said Pat Horner, an engineering team leader at Fountain Quail. “It leaves behind all the contaminants in a concentrate, so we can take that steam and just condense that into pure, distilled water, and take the concentrate away.”
“There are technologies handling the flow-back water, and handling it very well,” Waits said. “The flow-back water has very low T.D.S. and is pretty good shape coming in, and that’s not to talk critically of other technology. Where we come in is the produced water. It has as much as three to four times the T.D.S. of the flow-back water and No. 1: most processes can’t even deal with it, and No. 2: they can’t concentrate it enough.
At the behest of Devon, however, Fountain Quail has been modifying the NOMADs to enable the machines to reach for higher T.D.S. levels.- (Crusader question-ECCI modified NOMADS??? Compare to recent ECCI PR-see below)
Investing in the technologies today is a hope that in the future the costs will decrease and the efficiency will increase, said Grable, but he added if the operators view the technology as “grossly uneconomic,” they’re unlikely to buy into it..." (end excerpt)
COMPARE SOME OF THE HIGHLIGHTED PLAYERS ABOVE WITH THE RECENT ECCI PR BELOW:
Ecoloclean Announces Positive Success at Barnett Shale
* PR Wednesday December 3, 2008, 11:14 am EST
FORT WORTH, Texas--(BUSINESS WIRE)--Ecoloclean Industries, Inc. (Pink Sheets:ECCI - News) today announced recent success of testing results from operations at the Barnett Shale strata.
Full scale operating tests were undertaken at the West Crossroads location of Fountain Quail Water Management. The testing provided positive results and analytical data that the E-C WaterPure™ electrocoagulation process is an effective alternative to chemical based pretreatment processes currently in use in operations at the Barnett Shale strata.
Under the direction Jerry Inman, Vice President of Research and Development and John Adams, Vice President of Operations at Ecoloclean Industries, Inc., the E-C WaterPure™ unit operated for ten days treating flowback water on location. The E-C WaterPure™ unit provided conclusive proven positive results to be effective at reducing suspended solids.
Direct analytical comparisons clearly showed the E-C WaterPure™ unit provided greater effectiveness in removing ten of the twelve contaminants tested. In addition, the E-C WaterPure™ unit is both well suited and fully-developed to provide for implementation in mobile applications.(Crusader question: which 10? If the back flow water is going to an injection well, it does not matter much. If the back flow water is going to be used to frac more wells, then it goes through a NOMAD and all solids are removed by distillation and the NOMAD works cheaper, faster and more effectively!!!NEWS!!?)
Royis Ward, President of Ecoloclean Industries, Inc., stated, “With these solid results under our belt we are moving forward with marketing efforts with other contacts in the oil and gas fields to pre-treat flowback and produced water.”
FEATURED Element79 Gold Corp. Reports Significant Progress in Community Relations and Development Efforts in Chachas, Peru • Oct 9, 2024 10:30 AM
Unitronix Corp Launches Share Buyback Initiative • UTRX • Oct 9, 2024 9:10 AM
BASANITE INDUSTRIES, LLC RECEIVES U.S. PATENT FOR ITS BASAFLEX™ BASALT FIBER COMPOSITE REBAR AND METHOD OF MANUFACTURING • BASA • Oct 9, 2024 7:30 AM
BNCM COMPLETES MERGER WITH DELEX HEALTHCARE • BNCM • Oct 8, 2024 9:54 AM
CBD Life Sciences, Inc. (CBDL) Reaches Unprecedented Heights With Explosive Growth and Strategic Expansion in 2024 • CBDL • Oct 8, 2024 8:00 AM
Unitronix Corp. to Invest $3 Million in USA Unity Coin Project • UTRX • Oct 7, 2024 7:08 AM