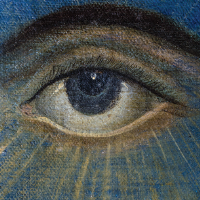
Saturday, February 19, 2022 2:34:48 PM
I believe that Advent has developed an automated (digitized) workflow using multiple pieces of equipment to close and automate most of these processes for the commercial production of DCVax. The lot release specifications required for a commercial product are much more stringent than for clinical trials, so it’s necessary to eliminate technician variability, and contamination risk by closing and automating the open manual processes. (recall that Novartis was forced to give away over 25% of Kymriah batches for free because they could not meet commercial specs) Part of process optimization also involves reducing high cleanroom and labor costs, and eliminating potential time-sensitive bottlenecks due to manual processes. (there’s no sense in automating and speeding up certain processes, only to be backed up later by a lengthy manual step following it)
I believe the first manufacturing step, isolation/enrichment of PBMC’s from the leukapheresis material, has already been closed and automated with Tangential Flow Filtration, and the culturing, maturation, lysate pulsing,and washing will be automated and closed within the Flaskworks system. The final, “fill and finish” step is currently open and manual, which brings inherent technician-dependent variability, potential contamination risk, high labor and cleanroom costs, and a potential bottleneck in higher volumes, so I believe it will also be closed and automated for commercial production. I’m guessing that Advent may use a commercially available fill and finish system like the “Finia,” which is capable of filling individual doses into cryovials. Although it shows cryobags instead of vials, there’s a video which compares this automated system to the manual method here
Advent has been working on a monumental task that not only includes building out and certifying Sawston, but also developing a new automated manufacturing protocol based on the previous manual protocols, and incorporating that with Autolomous’s manufacturing execution system (MES,) a comprehensive, dynamic software system that monitors, tracks, documents, and controls the process of manufacturing goods from raw materials to finished products. Some of this work has been done, but a good part could not even begin until production was started at Sawson, so anyone who thinks this will be completed by the first or second quarter is probably underestimating the task.
Recent NWBO News
- Biophma Announces Exclusive In License for Dendritic Cell Technology, Sending Shares Higher • AllPennyStocks.com • 06/17/2024 04:40:00 PM
- Form 8-K - Current report • Edgar (US Regulatory) • 06/04/2024 09:11:16 PM
- Form DEF 14A - Other definitive proxy statements • Edgar (US Regulatory) • 06/03/2024 09:22:55 PM
- Form PRE 14A - Other preliminary proxy statements • Edgar (US Regulatory) • 05/22/2024 08:13:36 PM
- Form 10-Q - Quarterly report [Sections 13 or 15(d)] • Edgar (US Regulatory) • 05/10/2024 09:04:57 PM
- Form NT 10-K - Notification of inability to timely file Form 10-K 405, 10-K, 10-KSB 405, 10-KSB, 10-KT, or 10-KT405 • Edgar (US Regulatory) • 03/01/2024 10:04:38 PM
- Form 4 - Statement of changes in beneficial ownership of securities • Edgar (US Regulatory) • 12/02/2023 01:31:35 AM
- Form 8-K - Current report • Edgar (US Regulatory) • 11/16/2023 10:11:54 PM
- Epazz, Inc. (OTC Pink: EPAZ) ZenaDrone Demonstration to Defense Departments of UAE and Saudi Arabia • InvestorsHub NewsWire • 11/15/2023 12:19:31 PM
- Form 10-Q - Quarterly report [Sections 13 or 15(d)] • Edgar (US Regulatory) • 11/09/2023 09:30:39 PM
- Epazz, Inc. (OTC Pink: EPAZ) US Navy Collaboration ZenaDrone 1000 • InvestorsHub NewsWire • 11/09/2023 01:00:34 PM
- Epazz, Inc. (OTC Pink: EPAZ) US Navy Collaboration ZenaDrone 1000 Extreme Weather Demo • InvestorsHub NewsWire • 11/07/2023 12:29:43 PM
- Form 10-Q - Quarterly report [Sections 13 or 15(d)] • Edgar (US Regulatory) • 08/09/2023 08:36:14 PM
Last Shot Hydration Drink Announced as Official Sponsor of Red River Athletic Conference • EQLB • Jun 20, 2024 2:38 PM
ATWEC Announces Major Acquisition and Lays Out Strategic Growth Plans • ATWT • Jun 20, 2024 7:09 AM
North Bay Resources Announces Composite Assays of 0.53 and 0.44 Troy Ounces per Ton Gold in Trenches B + C at Fran Gold, British Columbia • NBRI • Jun 18, 2024 9:18 AM
VAYK Assembling New Management Team for $64 Billion Domestic Market • VAYK • Jun 18, 2024 9:00 AM
Fifty 1 Labs, Inc Announces Acquisition of Drago Knives, LLC • CAFI • Jun 18, 2024 8:45 AM
Hydromer Announces Attainment of ISO 13485 Certification • HYDI • Jun 17, 2024 9:22 AM