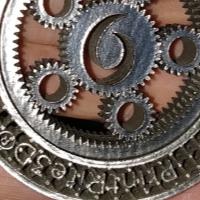
Thursday, December 07, 2017 4:05:38 PM
(1) Process Validation
Device quality, such as feature geometry, overall dimensions, material
characteristics, and mechanical properties, are impacted by AM process
parameters, process steps, and raw material properties, as described in the sections
above. In addition, for an identical device or component, quality may vary when
built using different AM machines, even when the same machine model,
parameters, process steps, and raw materials are used. Therefore, knowledge of
how the variability of each input parameter and processing step affects the final
finished device or component is critical to ensuring part quality. Where the
results of a process cannot be fully verified by subsequent inspection and testing,
the process must be validated with a high degree of assurance and approved
according to established procedures.
21 In addition all documentation must
conform to the existing guidelines in the Quality System regulation for device
validation. Process validation must be performed to ensure and maintain quality
for all devices and components built in a single build cycle, between build cycles,
and between machines, where the results of a process (i.e., output specifications)
cannot be fully verified by subsequent inspection and test.
22 Software also must
be validated for its intended use according to an established protocol23 (i.e.,
software workflow).
For validated processes, the monitoring and control methods and data must be
documented.
This section provides some examples of methods for ensuring the
consistency of quality. The list is meant to be representational of the type of
factors to consider when performing process validation. It can be used as a
reference point but is not exhaustive. The following examples may have the
greatest applicability to powder bed fusion technologies, which comprise a large
portion of AM medical devices. Methods could include:
· in-process monitoring of parameters such as:
o temperature at the beam focus,
o melt pool data,
o build-space environmental conditions (e.g., temperature, pressure,
humidity),
o power of the energy delivery system (e.g., laser, electron beam,
extruder), and
o status of mechanical elements of the printing system (e.g., recoater,
gantry)
In-process monitoring may also be helpful for processes that are not
validated, but is not required.
· manual or automated visual inspection with defined acceptance criteria,
· non-destructive evaluation (see Section V.E.3 Verification), and
· test coupon evaluation (see Section V.E.4 Test Coupons).
Not every AM system will be able to perform all these measurements, either
because the process does not use them or because of technological limitations.
Test methods used for process monitoring and control must be validated.
25
For example, analysis should be conducted to confirm that test coupons used are
representative of the final finished device or component and representative of a
certain area within the build volume.
A single failed component or device in a build cycle may not necessitate the
rejection of all other devices or components within that build cycle. The criteria
for determining whether to reject a single device or component, or the entire
build, should be established before testing.
North Bay Resources Commences Operations at Bishop Gold Mill, Inyo County, California; Engages Sabean Group Management Consulting • NBRI • Sep 25, 2024 9:15 AM
CEO David B. Dorwart Anticipates a Bright Future at Good Gaming Inc. Through His Most Recent Shareholder Update • GMER • Sep 25, 2024 8:30 AM
Cannabix Technologies and Omega Laboratories Inc. Advance Marijuana Breathalyzer Technology - Dr. Bruce Goldberger to Present at Society of Forensic Toxicologists Conference • BLOZF • Sep 24, 2024 8:50 AM
Integrated Ventures, Inc Announces Strategic Partnership For GLP-1 (Semaglutide) Procurement Through MedWell USA, LLC. • INTV • Sep 24, 2024 8:45 AM
Avant Technologies Accelerates Creation of AI-Powered Platform to Revolutionize Patient Care • AVAI • Sep 24, 2024 8:00 AM
VHAI - Vocodia Partners with Leading Political Super PACs to Revolutionize Fundraising Efforts • VHAI • Sep 19, 2024 11:48 AM