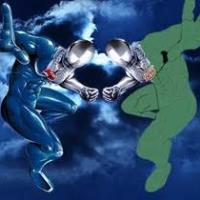
Thursday, November 16, 2017 3:40:06 PM
Nanotechnology Coatings Help Manage Energy Costs
Nano Technology Saves Lives Rising energy costs are a huge motivator for any manufacturer to find ways to increase energy efficiency in its processes and plants. Although, according to the EPA, energy use ranks third among costs for food manufacturers, behind raw materials and labor, for years it has been viewed as a fixed expense, and one not as easily managed. With new technology now available, the food industry has substantial potential for energy efficiency improvement, which may mean significant cost savings for an industry with relatively thin margins compared to other manufacturing sectors.
Featured Products
NANSULATE Paint, Acrylic Latex, Clear
5JER8
NANSULATE Thermal Insulation Coating, Clear, Epoxy
5JER9
NANSULATE Thermal Insulation Coating, Clear, Epoxy
5JET0
It is estimated that 40 percent of the cost of processed food is added through energy intensive manufacturing (1). Process heating and cooling systems have the greatest energy demands for food manufacturing and are critical to maintaining food safety.
Something that these systems all share with other types of manufacturing is the need to use energy to heat and cool – through the use of boilers, heat exchangers, pipes, furnaces and refrigeration units. In every heating or cooling system, there is heat loss and gain. By reducing the amount of heat loss or gain, manufacturers not only reduce the energy used, but they can also improve the manufacturing process and the consistency of the product.
A new technology that is making changes in the food manufacturing industry is a family of nanotechnology-based equipment insulation coatings.
Introduced under the brand name of Nansulate® and manufactured by Industrial Nanotech, Inc. The nanotechnology coatings are based upon an award-winning, patented technology (#7144522) which incorporates a safe, micro-sized particle with nano-sized internal architecture into a low VOC water-based acrylic latex coating. The nanocomposite has extremely low thermal conduction and a hydrophobic nature. What this offers to manufacturers in the food processing industry is the ability to easily insulate heat process and cooling equipment, while also protecting the equipment from corrosion and mold growth.
One early adopter from the dairy industry knows the benefits of this new technology well. In 2005, Ultraspin Technology in Australia used the coating to insulate a 54-square-foot outdoor stainless steel tank which was used for melting butterfat. David Morabito, Process Engineer, explained, “We achieved a measurable difference in the contents of this tank. The outside was previously too hot to touch. With three coats applied, the tank was now warm to the touch and there was a visual improvement to the melting efficiency of the product inside.”
Significant energy savings attributed to the Nansulate coatings have been experienced in many industries, with textile manufacturing being a leader in adoption of the insulation technology. In 2006, Henateks, a textile manufacturer in Istanbul, Turkey, coated all of their heat producing equipment with this technology. They saved over $460,000 in energy costs in 2008 due to the use of the new insulation coatings, and reduced their natural gas use by 38,755,975 cubic feet. Their material cost for the project was $200,000 and their payback period was seven months. Overall energy costs were reduced by 20 percent.
In addition to offering insulation, corrosion prevention and resistance to mold growth, the coatings are also clear, which allows for visual inspection of the substrate surface without costly removal.
The company’s General Purpose product was awarded NSF nonfood compound registration (formerly U.S. Department of Agriculture registration) under the R2 category (Incidental Food Contact), which was done specifically for the food industry (Registration # 138638).
Food safety is an important concern of food manufacturers. There are many processes that have been nearly impossible to insulate because of the porous nature of traditional types of insulation and their propensity to trap dust, dirt, mold and other contaminates. This fact has been a contributing factor to energy consumption being categorized as a fixed expense in the past. Being a “clean” insulation is one of the unique benefits of using insulation in a coating form, which is brushed or sprayed onto equipment and won’t trap moisture, mold or dirt, which can contaminate food processes. With the ability to insulate equipment that could not safely be insulated previously, food manufacturers can now reap significant cost savings.
New technology typically comes with a high price tag, but Nansulate coatings are an exception. Applications can be done while the lines are running. The ability to significantly reduce costs without a large capital expenditure is making this technology a unique and viable option for the food manufacturing industry. Users typically see a return on their initial investment in 6-18 months, and many in less than a year.
Due to the energy intense processing costs of the food manufacturing industry, companies stand to benefit from substantial decreases in energy usage for heating or cooling processes. The bottom line is that this new technology can convert formerly fixed energy costs to manageable variable expenses, allowing manufacturers to lower energy costs and improve profit margins.
1. Source: Energy Trends in Selected Manufacturing Sectors: Opportunities and Challenges for Environmentally Preferable Energy Outcomes. March, 2007. U.S. Environmental Protection Agency).
Article courtesy of INDUSTRIAL NANOTECH, INC., Industrial an official Department of Energy ALLY Organization for the “Save Energy Now” initiative. http://www1.eere.energy.gov/industry/saveenergynow/leader_ally.html
$INTK
PEPSI
NanoViricides Reports that the Phase I NV-387 Clinical Trial is Completed Successfully and Data Lock is Expected Soon • NNVC • May 2, 2024 10:07 AM
ILUS Files Form 10-K and Provides Shareholder Update • ILUS • May 2, 2024 8:52 AM
Avant Technologies Names New CEO Following Acquisition of Healthcare Technology and Data Integration Firm • AVAI • May 2, 2024 8:00 AM
Bantec Engaged in a Letter of Intent to Acquire a Small New Jersey Based Manufacturing Company • BANT • May 1, 2024 10:00 AM
Cannabix Technologies to Deliver Breath Logix Alcohol Screening Device to Australia • BLO • Apr 30, 2024 8:53 AM
Hydromer, Inc. Reports Preliminary Unaudited Financial Results for First Quarter 2024 • HYDI • Apr 29, 2024 9:10 AM