Followers | 9 |
Posts | 1597 |
Boards Moderated | 1 |
Alias Born | 01/27/2014 |
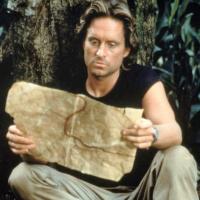
Monday, June 12, 2017 6:57:09 AM
3DPrinting innovates while breathing life into traditional aero manufacturing
At sae.org - Reaching forward and back: 3D printing innovates while breathing life into traditional aero manufacturing - 10-Jun-2017
The end section of the text:
For now, the jet’s maiden flight showcased the major role that 3D printing will have in the country’s manufacturing sector. Wendy Mok, Research Manager of IDC China’s Imaging Printing and Document Solutions, sees continued increases in the adoption of 3D printing technologies in the aerospace industry.
"For instance, General Electric acquired two metal 3D printer manufacturers, Concept Laser and Arcam, in which they have been providing 3D printers to aircraft parts manufacturers. Rolls Royce is one of Arcam’s users. Norsk Titanium produces the first FAA-approved 3D printed structural titanium components for Boeing's 787," she said. (Read more about Norsk Titaniums’s work here.) "In China, the success of C919’s maiden flight implies the use of 3D printed parts on airliners have been recognized by the aviation industry in China.
The domestic demand for 3D printed parts will grow with expectations that the orders of 570 units of C919 delivered by Comac in the future, coupled with an increase in localization rate
“Market players like 3D printer vendors, material suppliers, and service bureaus should have a comprehensive understanding on the market segments and their related development trends,” Mok said. “With the right market positioning and entry point, these market players will be able to gain more return on the fast-growing 3D printing market.”
While 3D printed “on-demand” components and new lightweight designs enabled by 3D printing promise affordability and accelerated production times, many firms in the US have been incorporating 3D printing techniques to enhance their existing traditional manufacturing processes, such as casting.
The ability to replace sophisticated castings with AM-produced metal parts has not yet matured. A current alternative that many manufacturers are leveraging is incorporating 3D printed tooling for rapid production of precision castings.
While wax patterns have been used to some degree for many years, the production of complex investment castings requires the use of sophisticated ceramic cores and molds. The tooling for these process aids is expensive and takes months to design, produce, and qualify.
“Rapid 3D printing for prototyping for patterns has existed in the aerospace industry for years, but now we’re able to 3D printing for cores and complete molds” said Ben Rampulla, Senior Engineer at PCC Structurals during a presentation at the RAPID + TCT Conference in Pittsburgh.
With traditional investment casting, an aluminum pattern of the cast is machined. This tooling will be used to mold wax into the cast shape. Depending on complexity, this may take a few weeks to a few months. Once the wax is injected and is formed into patterns, the patterns are assembled to a “tree.” The tree is dipped into a ceramic slurry and then into sand and left to dry. The ceramic coating process may be repeated several times. That takes between a day to a week to perform, depending on a facility’s capabilities.
The wax is then melted out and the ceramic tree is fired. The gaps left from the wax tree are the channels that the casting metal will take to reach the empty ceramic molds. After the metal is poured and has cooled, the ceramic tree is broken, and then the castings go into post processing.
“With additive, what we’ve done is taken the CAD model that had been used to make the injection molding tooling and we’ve 3D printed a ceramic mold. The ceramic mold goes into firing, then we pour the metal, break the mold, and then go into post processing. And we performed that entire process in a week,” said Rampulla.
Rampulla’s co-presenter, Dan Sokol, Managing Partner of Renaissance Services, went on to describe their study into to traditional injection process of ceramic cores, specifically for airfoils.
“It is a very nuanced process. It’s not like making coffee cups. The ceramic can’t be too strong and it can’t be too weak. It has to be strong enough to endure the wax injection, but it’s got to be able to be removed through the leaching process to make that airfoil hollow. There are very complex yield rates,” said Sokol.
According to Sokol, the real applications for 3D printing enhanced casting are not in the low-complexity, high-volume operations, but when there is experimentation, when there is a need for specific features like multiwalled cores, or when tooling is expensive—as in aging airframes and engines that no longer have active supply chains associated with them.
“If you start looking at some of the ages of these aircraft and engines—the B-52 for example—which is still a mainstay of the U.S. Air Force, it’s 50 or 60 years old. For a while they cannibalizing parts for them from the boneyard out at Davis-Monthan Air Force Base, but now they’re starting to run out of parts. We were out at Tinker Air Force Base where they maintain at least 20,000 or so engines where we were told ‘Here’s an aluminum accessory housing that is ordered 2 years out at $80,000 and this aircraft will be on ground until we get it,’ because there’s no tooling for the part anymore. That’s some of the stuff we’re working on now, where 3D can alleviate pain points with rapid solutions.”
At sae.org - Reaching forward and back: 3D printing innovates while breathing life into traditional aero manufacturing - 10-Jun-2017
The end section of the text:
For now, the jet’s maiden flight showcased the major role that 3D printing will have in the country’s manufacturing sector. Wendy Mok, Research Manager of IDC China’s Imaging Printing and Document Solutions, sees continued increases in the adoption of 3D printing technologies in the aerospace industry.
"For instance, General Electric acquired two metal 3D printer manufacturers, Concept Laser and Arcam, in which they have been providing 3D printers to aircraft parts manufacturers. Rolls Royce is one of Arcam’s users. Norsk Titanium produces the first FAA-approved 3D printed structural titanium components for Boeing's 787," she said. (Read more about Norsk Titaniums’s work here.) "In China, the success of C919’s maiden flight implies the use of 3D printed parts on airliners have been recognized by the aviation industry in China.
The domestic demand for 3D printed parts will grow with expectations that the orders of 570 units of C919 delivered by Comac in the future, coupled with an increase in localization rate
“Market players like 3D printer vendors, material suppliers, and service bureaus should have a comprehensive understanding on the market segments and their related development trends,” Mok said. “With the right market positioning and entry point, these market players will be able to gain more return on the fast-growing 3D printing market.”
While 3D printed “on-demand” components and new lightweight designs enabled by 3D printing promise affordability and accelerated production times, many firms in the US have been incorporating 3D printing techniques to enhance their existing traditional manufacturing processes, such as casting.
The ability to replace sophisticated castings with AM-produced metal parts has not yet matured. A current alternative that many manufacturers are leveraging is incorporating 3D printed tooling for rapid production of precision castings.
While wax patterns have been used to some degree for many years, the production of complex investment castings requires the use of sophisticated ceramic cores and molds. The tooling for these process aids is expensive and takes months to design, produce, and qualify.
“Rapid 3D printing for prototyping for patterns has existed in the aerospace industry for years, but now we’re able to 3D printing for cores and complete molds” said Ben Rampulla, Senior Engineer at PCC Structurals during a presentation at the RAPID + TCT Conference in Pittsburgh.
With traditional investment casting, an aluminum pattern of the cast is machined. This tooling will be used to mold wax into the cast shape. Depending on complexity, this may take a few weeks to a few months. Once the wax is injected and is formed into patterns, the patterns are assembled to a “tree.” The tree is dipped into a ceramic slurry and then into sand and left to dry. The ceramic coating process may be repeated several times. That takes between a day to a week to perform, depending on a facility’s capabilities.
The wax is then melted out and the ceramic tree is fired. The gaps left from the wax tree are the channels that the casting metal will take to reach the empty ceramic molds. After the metal is poured and has cooled, the ceramic tree is broken, and then the castings go into post processing.
“With additive, what we’ve done is taken the CAD model that had been used to make the injection molding tooling and we’ve 3D printed a ceramic mold. The ceramic mold goes into firing, then we pour the metal, break the mold, and then go into post processing. And we performed that entire process in a week,” said Rampulla.
Rampulla’s co-presenter, Dan Sokol, Managing Partner of Renaissance Services, went on to describe their study into to traditional injection process of ceramic cores, specifically for airfoils.
“It is a very nuanced process. It’s not like making coffee cups. The ceramic can’t be too strong and it can’t be too weak. It has to be strong enough to endure the wax injection, but it’s got to be able to be removed through the leaching process to make that airfoil hollow. There are very complex yield rates,” said Sokol.
According to Sokol, the real applications for 3D printing enhanced casting are not in the low-complexity, high-volume operations, but when there is experimentation, when there is a need for specific features like multiwalled cores, or when tooling is expensive—as in aging airframes and engines that no longer have active supply chains associated with them.
“If you start looking at some of the ages of these aircraft and engines—the B-52 for example—which is still a mainstay of the U.S. Air Force, it’s 50 or 60 years old. For a while they cannibalizing parts for them from the boneyard out at Davis-Monthan Air Force Base, but now they’re starting to run out of parts. We were out at Tinker Air Force Base where they maintain at least 20,000 or so engines where we were told ‘Here’s an aluminum accessory housing that is ordered 2 years out at $80,000 and this aircraft will be on ground until we get it,’ because there’s no tooling for the part anymore. That’s some of the stuff we’re working on now, where 3D can alleviate pain points with rapid solutions.”
Join the InvestorsHub Community
Register for free to join our community of investors and share your ideas. You will also get access to streaming quotes, interactive charts, trades, portfolio, live options flow and more tools.