Followers | 9 |
Posts | 1597 |
Boards Moderated | 1 |
Alias Born | 01/27/2014 |
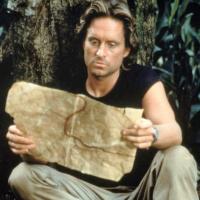
Wednesday, March 15, 2017 10:13:48 PM
The patent secures 3D giant
We've been asking for news. For what it's worth, here it is.
Patenten säkrar 3D-jätten
Using Google Translate - The patent secures 3D giant
The patent secures 3D giant
Magnus René. In the picture beside Plastic Printers with wire and use liquor method.
RADIATION METHOD. In Arcam machine adds thin layers of metal powder out and melted with an electron beam.
The globe is printed in a single part, but can still rotate.
Arcam's headquarters will remain in Mölndal, but CEO Magnus René has moved to the United States, which is the company's fastest growing market. Photo: Amanda Lindgren
By CATHERINE HOFBAUER
published: March 14, 2017, 21:00 Updated: March 15, 2017, 09:15
Although the industry is relatively young celebrates the 3D printer manufacturer Arcam 20th anniversary this year.
Already seated many Arcamtillverkade details of people and aircraft engines - and the potential ahead are great, according to CEO Magnus René.
Krokslätts factories in Mölndal, outside Gothenburg, housed around the turn of the century, a weaving business. As with so many other companies in the cable industry went into the grave in the aftermath of the 1960s the textile crisis. But while industries disappear or move creates new.
Just decades after the coffee crisis had evacuated the premises began weaving company Arcam's co-founder Ralf Larson ponder Rapid prototyping. And it is in Krokslätts factories we now find 3D printing company Arcam.
Company printers are used for manufacturing aircraft parts.
"It is Arcamtillverkade details of the new Bombardier plane with Pratt engines and Rolls-Royce have run with Arcamtillverkade parts in their test series. GE is the engine called GE9X that will sit in the triple 7th grade (Boeing 777), which will have the turbine blades manufactured in our machine, "says Arcam's CEO Magnus René.
The most spectacular objects that come from Arcam printers are different types of orthopedic implants.
For about ten years ago wrote the New Technology of Jules Poukens surgeon at the University Hospital of Maastricht, which replaced a portion of the skull of a young woman, who had suffered a car accident, with a titanium implant printed in a Arcamskrivare.
Two years ago, Forbes wrote about a Spanish cancer patient who received both the new ribs and sternum in a new titanium, also from a Arcammaskin.
That which most often are produced by so called additive manufacturing of metal is an orthopedic detail called acetabular cup. Arcam's CEO Magnus René explains:
"When you do a hip replacement surgery, the patient down a component in the femur as the hip ball sitting on. The second part, the ball should be in placed in the pelvis and it is called the acetabular cup. What makes the additive manufacturing suitable is that you can do something that is very solid and materially accurate. But since it is made with a printer you can also do a lot of intricate and interesting structures on the outside, as the bone grows into and which fixes part of the pelvis. "
The exterior of the brick building we are in, with large windows and a classic smokestack, provides a strong contrast to the Arcam modern interior.
Once we have passed the entrance we are in production, with refrigerator-like 3D printers in various manufacturing stages are all around. It is peaceful and quiet in the room. A fully assembled machine will flash a little when it prints the test rods that all machines must be able to produce before they are shipped to customers. The process is virtually silent.
The space is much larger than at Di's last visit three years ago.
"Yes, we have built out a part," says Magnus René.
Its headquarters is not the only thing that has grown. AP & C, the metal producers that Arcam bought in late 2013, for a total consideration of approximately SEK 240 million, doubled its workforce last year and in October started construction of a second powder plant in Montreal, Canada.
AP & C, which prior to the acquisition was a supplier to the Arcam is now the world's largest manufacturers of spherical titanium powder.
Titanium is the material often used in Arcam printer, but really it is possible to use any metal form. The reason that titanium is so popular print in the price of doing.
"If you look at the biggest advantages of 3D printers, it is an important advantage that the process is efficient materials. And then, one strives to use expensive materials that are difficult to process in other ways. The more expensive the better, because the material efficiency would be greater importance ", says Magnus René.
A 20-kilo cans of powder Magnus René showcases costs about 28,000 crowns.
"We are the world's largest titanium powder, but looking to the total titanium production, we will account for 1 percent."
Over time think Magnus René to Arcam machines will be able to compete in terms of production in other materials. Product development is currently most of the productivity and precision.
Among other things, the company has received about 2 million, ie around 19 million, from the EU for a plasma project that aims to develop a new way to generate electron beam melts the metal during the printing process.
"The idea is that it should be even higher power."
Warmer need the beam gets. Instead, it should move faster to print objects. Productivity is a key factor in increasing market shares in different industries.
"It is not that we are straight up and down can compete with the casting. Should we do it, which is our intent, we must be a few times more efficient. "
Efficiency actually leads to lower cost per part produced, and to take on new industries have to offer customers lower costs.
In addition to material efficiency is reduced lead times, another key advantage that 3D manufacturing has over traditional manufacturing. No specialized tools are needed and it does not manufactured some molds for casting.
"A third advantage is the design freedom and can be used on at least two different ways. One is to produce things that simply can not do otherwise. The second is to manufacture products which, instead of using many different parts that are welded and bolted together can print everything that one detail, "says Magnus René.
Construction chamber size is what sets the limits. The largest objects that can be printed in a Arcammaskin is 40 centimeters in diameter and 40 centimeters high.
Why have you chosen to focus you on the right flights and orthopedics?
"We want to work with industries and companies that use expensive materials and does not work with huge volumes. Lead-efficiency and low utility costs increase the weight of the lower volumes. Another objective is to find industries where design freedom gives benefit. And then you end up in implants and aerospace industry. "
Design freedom as 3D printers produce, help the aviation industry to reduce the weight of planes and reduce fuel consumption.
"These two industries are also so large that it will be enough for us to turn to them for a very long time," says Magnus René.
In addition to Arcam manufactures 3D printers and related powder company also offers so-called contract manufacturing by the US company DiSanto, which was acquired in full for about two and a half years ago. DiSanto manufactures, on behalf of customers, orthopedic implants and instruments, with both the traditional technique using Arcam's 3D printers.
In round numbers are printers for half of Arcam's turnover, the powder is about 35 percent and contract manufacturing around 15 percent. Powder bulk is growing fastest.
The printers cost between half a million and 1 million euros, and customers often expect to add about as much to install the machines and learning to use the technology, because the use is not simply to master.
Arcam's first paten t arrived in the early 1990s and was taken out by entrepreneur and inventor Ralf Larson.
"Ralf was very early with additive manufacturing. The first company in the industry, 3D Systems, started in 1986. So it is still a young industry.
To get spin on the whole thing took Ralf Larson help of Charlie Davidsson, professor of robotics.
"Charlie put it up as an example, job opportunity, to see if it was possible to realize that Ralf had been patented," says Magnus René.
Morgan Larsson was named the student who took on the task and a company created in 1997 by Ralf Larson and Jarl Assmundson, who was the financier. In February, celebrated because the company's 20th anniversary.
After just a few years proved to technology have flaws. An audit of the led to the electron beam technology Arcam still uses and is completely unique in the industry.
The new solution means a whole series of patents. Using an electron beam in a 3D printer could not be patented.
"But we have lots of other patents around the electron beam technology, which is extracted during the entire trip, which is important for us", says Magnus René, who says he is sure that no one else can start using electron beam technology.
The portfolio consists of about a hundred patents around the electron beam.
Arcam competitors, EOS, Concept Laser and SLM Solutions uses all laser to melt titanium powder in their printers. It allows competitors to some extent focused on little other end users than the Arcam.
"It is clear that there are areas where we overlap, so that we are direct competitors with the system based on the laser. But we have quite a large area where we are diversified too. There you can also see on the big customers, they almost always have both Arcamskrivare and laser printers, "says Magnus René.
The Arcam electron beam is more productive and thus can print more implants in less time, will enable the company, according to Magnus René, is larger than competitors on right hip implants. The competitors with laser technology is often more niche in industries that manufacture small parts in titanium.
"Dental products make you happy with the laser," he says.
Long was Industry Fund Arcam's largest shareholder.
"It was very successful, both for them and for us. We are, I believe, Industrial Fund's second best investment ever. Data analysis company Qlik is number one."
Today ownership situation is completely different. After General Electric's bid last fall takes giant group 76 percent of the company. Elliott Capital, which has just budprocesser as investment philosophy, owns 10 percent. But hedge fund is not alone to hold on to their shares.
At this writing, there are about 1 000 shareholders of Arcam, and even if GE would buy Elliott's 10 percent, the company will not actually over the 90 percent of shares required to initiate compulsory acquisition.
GE has bought a majority think Magnus René will be very good for the company.
The same day as the bid for Arcam came, GE also bid on one of Arcam's German competitors, SLM Solutions. This commandment was not through. Instead, GE acquired another German competitor, Concept Laser.
But although he is happy, and have sold all their shares to GE, Magnus René could not help but reflect upon the situation could have been different. He seems somewhat disappointed by the lack of interest that has been around for the company among Swedish investors.
When the Industrial Development Fund in 2015 wanted to dispose of their shares was Magnus René with and tried to place the shares at any Swedish player. But it did not work.
A thought that Magnus René has about it is that Swedish investors have found it difficult to value the company. Many thought that the Industrial Development Fund wanted to charge a lot. But when GE over a year later made a bid for the company was the American group prepared to pay twice as much.
"One may wonder why this is so. We might as well have owned a Swedish industrial company. In this type of company requires that anyone can come in with a lot of resources and determination and there are many Swedish companies with the resources. "
Even when it comes to other Swedish efforts in this area are Magnus René particularly impressed.
Innovation agency Vinnova's efforts in recent years he describes as "too little, too late".
As for universities, the Royal Institute of Technology and the universities in Ostersund and Örebro was his Arcammaskin. There are important initiatives, but compared with institutions in other countries in the Arcam customer records are modest installations.
"Unfortunately Sweden has fallen a bit behind, despite the fact that we are here."
As for the customers out Magnus René Arcam is very niche on two industries that is as far in Sweden.
Among the international customers, he can count up all of the major in the aerospace industry, such as Rolls-Royce, Pratt & Whitney, Honeywell, GKN and Airbus.
The headquarters will remain in Mölndal. Magnus René, however, moved to the United States, partly because it is the fastest growing market. The workforce is now greater there than in Europe. Arcam is growing rapidly in both Sweden and abroad, and are continuously looking for new employees.
How the business will change in concrete terms, in that the company has received a new principal owner is so far hard to say.
"It still means that we have a new principal owner who has great ambition for us, and that is very good at flying. They have resources, both in terms of technical expertise and financial muscle. They are also very determined to get both this industry and for us to grow, which is reasonably good. "
When Magnus René looks to the future, it is still in orthopedics and aerospace as he sees the greatest potential.
"Within ten years, I believe that all of the metal in orthopedics will be made with 3D printing," he says.
It provides a strong growth potential because less than 1 percent of orthopedic implants in metal today are produced in 3D printers.
"When it comes to flight, we believe that the potential is at least ten times as large as the potential in orthopedics. So there is much left to do. "
In addition to product development that takes place in the efficiency and precision Magnus René believe that industrialization will be crucial in the coming years.
"This is still machinery that is something of lab equipment. Compared to a 3D printer with the cutter at any time, so the training is to run the printer long and it takes a long time to serve it. They are also not very effective. "
A industrialization think he therefore becomes absolutely critical to take in new sectors, but also to diversify in areas Arcam already inside.
There is therefore a distant thought of going outside aviation and orthopedics?
"Sometime we will do it, but not right now."
Where there is the potential?
"They talk a lot about the gas and oil industry, they have not been so keen on investment. It's not about the drills without equipment to the bottom of the drill holes. It is a very technology-intensive industry operating in a difficult environment, which require advanced materials. Nor is it so long series. On the car side and also in the truck systems, one can imagine turbochargers and such. Things where design freedom or materials will make a difference. "
Magnus René is clear that the printers Arcam sells primarily used for volume production. The 3D printer would only be a tool for developing rapid prototyping is a description that he did not want to acknowledge.
"Then utilize only lead abbreviation and not the other benefits. Should you exploit the design freedom is of course totally pointless to print a prototype and then manufacturing it in any other way where you do not have design freedom, then you can not use the prototype. To take advantage of material efficiency and design freedom you have to go into production with the technology. "
When it comes to printers for consumers, Magnus René difficult to see the same potential in the industry. The vision of consumers would print their own shoes at home instead of buying them in the store think he will not become a reality.
"Just look at the market for standard printers. Although many have a home, it is not so many who have a good enough to print something that would work to have the painting on the wall, "he says.
That people could sit at home and print spare parts for refrigerators and furniture that is broken, he believes not on.
"Then I think more on the industrial development of such spare parts are no longer manufactured."
CATHERINE HOFBAUER
cathrine.hofbauer@di.se
There is a side panel with the following text:
LAYERING - HOW DOES A 3D PRINTER
The concept of 3D printing has gained great popularity among lay people and the press.
In industry speak, however, rather on additive manufacturing, at least when it comes to using technology in production. The concept comes from the manufacturing process is done by adding materials rather than subtracting from traditional manufacturing methods such as turning and milling.
Common to all 3D printers are starting from a three-dimensional drawing, usually a CAD drawing, which is divided into layers. The actual production of the item is then done by printing a layer at a time, layer upon layer. The Arcam printers begin the process of a thin layer of powder is placed on a base plate, on which the first layer is printed by the electron beam melts just those parts depicted in the layer. When it's time to write the next layer in the 3D model, moving the bottom plate down, the machine spreads a new layer of powder and then the electron beam is directed against those parts to be melted in the layer. The object is then printed out from the bottom up.
When all the layers are printed is building the house full of powder. The powder which has not melted is blown off and the remaining will be the printed object. To save time and money do you write out as many items as possible at the same time. Several other manufacturers of metal printers use a similar method, even if the beam that melts the metal is not the same. Another way to print three-dimensional models of the metal is to use a metal wire which is advanced by means of a robot arm and melted in the right place, layer by layer.
Plastic Printers also uses various techniques. The earliest, stereolithography SLA employs a tank of liquid plastic which is hardened by means of laser, layer by layer. The most common type of printer used today prints using a plastic thread that piped out.
THE BID FROM GE
GE's initial bid of Arcam came September 6, 2016 and stood at SEK 285 per share, which was approximately 53 percent above the previous day's closing price. A unanimous board recommended the offer.
About a week later, Elliott Capital managed to acquire 6.6 percent of the shares of Arcam. A week into October flagged hedge fund that it had been over 10 percent.
On 27 October, GE raised the bid to 300 kronor per share.
In November, GE announced that the offer would be implemented, even though the company then had only been together about 74 percent of the shares.
When the acceptance period then ended, GE has control over 76 percent of the shares.
We've been asking for news. For what it's worth, here it is.
Patenten säkrar 3D-jätten
Using Google Translate - The patent secures 3D giant
The patent secures 3D giant

Magnus René. In the picture beside Plastic Printers with wire and use liquor method.

RADIATION METHOD. In Arcam machine adds thin layers of metal powder out and melted with an electron beam.

The globe is printed in a single part, but can still rotate.

Arcam's headquarters will remain in Mölndal, but CEO Magnus René has moved to the United States, which is the company's fastest growing market. Photo: Amanda Lindgren
By CATHERINE HOFBAUER
published: March 14, 2017, 21:00 Updated: March 15, 2017, 09:15
Although the industry is relatively young celebrates the 3D printer manufacturer Arcam 20th anniversary this year.
Already seated many Arcamtillverkade details of people and aircraft engines - and the potential ahead are great, according to CEO Magnus René.
Krokslätts factories in Mölndal, outside Gothenburg, housed around the turn of the century, a weaving business. As with so many other companies in the cable industry went into the grave in the aftermath of the 1960s the textile crisis. But while industries disappear or move creates new.
Just decades after the coffee crisis had evacuated the premises began weaving company Arcam's co-founder Ralf Larson ponder Rapid prototyping. And it is in Krokslätts factories we now find 3D printing company Arcam.
Company printers are used for manufacturing aircraft parts.
"It is Arcamtillverkade details of the new Bombardier plane with Pratt engines and Rolls-Royce have run with Arcamtillverkade parts in their test series. GE is the engine called GE9X that will sit in the triple 7th grade (Boeing 777), which will have the turbine blades manufactured in our machine, "says Arcam's CEO Magnus René.
The most spectacular objects that come from Arcam printers are different types of orthopedic implants.
For about ten years ago wrote the New Technology of Jules Poukens surgeon at the University Hospital of Maastricht, which replaced a portion of the skull of a young woman, who had suffered a car accident, with a titanium implant printed in a Arcamskrivare.
Two years ago, Forbes wrote about a Spanish cancer patient who received both the new ribs and sternum in a new titanium, also from a Arcammaskin.
That which most often are produced by so called additive manufacturing of metal is an orthopedic detail called acetabular cup. Arcam's CEO Magnus René explains:
"When you do a hip replacement surgery, the patient down a component in the femur as the hip ball sitting on. The second part, the ball should be in placed in the pelvis and it is called the acetabular cup. What makes the additive manufacturing suitable is that you can do something that is very solid and materially accurate. But since it is made with a printer you can also do a lot of intricate and interesting structures on the outside, as the bone grows into and which fixes part of the pelvis. "
The exterior of the brick building we are in, with large windows and a classic smokestack, provides a strong contrast to the Arcam modern interior.
Once we have passed the entrance we are in production, with refrigerator-like 3D printers in various manufacturing stages are all around. It is peaceful and quiet in the room. A fully assembled machine will flash a little when it prints the test rods that all machines must be able to produce before they are shipped to customers. The process is virtually silent.
The space is much larger than at Di's last visit three years ago.
"Yes, we have built out a part," says Magnus René.
Its headquarters is not the only thing that has grown. AP & C, the metal producers that Arcam bought in late 2013, for a total consideration of approximately SEK 240 million, doubled its workforce last year and in October started construction of a second powder plant in Montreal, Canada.
AP & C, which prior to the acquisition was a supplier to the Arcam is now the world's largest manufacturers of spherical titanium powder.
Titanium is the material often used in Arcam printer, but really it is possible to use any metal form. The reason that titanium is so popular print in the price of doing.
"If you look at the biggest advantages of 3D printers, it is an important advantage that the process is efficient materials. And then, one strives to use expensive materials that are difficult to process in other ways. The more expensive the better, because the material efficiency would be greater importance ", says Magnus René.
A 20-kilo cans of powder Magnus René showcases costs about 28,000 crowns.
"We are the world's largest titanium powder, but looking to the total titanium production, we will account for 1 percent."
Over time think Magnus René to Arcam machines will be able to compete in terms of production in other materials. Product development is currently most of the productivity and precision.
Among other things, the company has received about 2 million, ie around 19 million, from the EU for a plasma project that aims to develop a new way to generate electron beam melts the metal during the printing process.
"The idea is that it should be even higher power."
Warmer need the beam gets. Instead, it should move faster to print objects. Productivity is a key factor in increasing market shares in different industries.
"It is not that we are straight up and down can compete with the casting. Should we do it, which is our intent, we must be a few times more efficient. "
Efficiency actually leads to lower cost per part produced, and to take on new industries have to offer customers lower costs.
In addition to material efficiency is reduced lead times, another key advantage that 3D manufacturing has over traditional manufacturing. No specialized tools are needed and it does not manufactured some molds for casting.
"A third advantage is the design freedom and can be used on at least two different ways. One is to produce things that simply can not do otherwise. The second is to manufacture products which, instead of using many different parts that are welded and bolted together can print everything that one detail, "says Magnus René.
Construction chamber size is what sets the limits. The largest objects that can be printed in a Arcammaskin is 40 centimeters in diameter and 40 centimeters high.
Why have you chosen to focus you on the right flights and orthopedics?
"We want to work with industries and companies that use expensive materials and does not work with huge volumes. Lead-efficiency and low utility costs increase the weight of the lower volumes. Another objective is to find industries where design freedom gives benefit. And then you end up in implants and aerospace industry. "
Design freedom as 3D printers produce, help the aviation industry to reduce the weight of planes and reduce fuel consumption.
"These two industries are also so large that it will be enough for us to turn to them for a very long time," says Magnus René.
In addition to Arcam manufactures 3D printers and related powder company also offers so-called contract manufacturing by the US company DiSanto, which was acquired in full for about two and a half years ago. DiSanto manufactures, on behalf of customers, orthopedic implants and instruments, with both the traditional technique using Arcam's 3D printers.
In round numbers are printers for half of Arcam's turnover, the powder is about 35 percent and contract manufacturing around 15 percent. Powder bulk is growing fastest.
The printers cost between half a million and 1 million euros, and customers often expect to add about as much to install the machines and learning to use the technology, because the use is not simply to master.
Arcam's first paten t arrived in the early 1990s and was taken out by entrepreneur and inventor Ralf Larson.
"Ralf was very early with additive manufacturing. The first company in the industry, 3D Systems, started in 1986. So it is still a young industry.
To get spin on the whole thing took Ralf Larson help of Charlie Davidsson, professor of robotics.
"Charlie put it up as an example, job opportunity, to see if it was possible to realize that Ralf had been patented," says Magnus René.
Morgan Larsson was named the student who took on the task and a company created in 1997 by Ralf Larson and Jarl Assmundson, who was the financier. In February, celebrated because the company's 20th anniversary.
After just a few years proved to technology have flaws. An audit of the led to the electron beam technology Arcam still uses and is completely unique in the industry.
The new solution means a whole series of patents. Using an electron beam in a 3D printer could not be patented.
"But we have lots of other patents around the electron beam technology, which is extracted during the entire trip, which is important for us", says Magnus René, who says he is sure that no one else can start using electron beam technology.
The portfolio consists of about a hundred patents around the electron beam.
Arcam competitors, EOS, Concept Laser and SLM Solutions uses all laser to melt titanium powder in their printers. It allows competitors to some extent focused on little other end users than the Arcam.
"It is clear that there are areas where we overlap, so that we are direct competitors with the system based on the laser. But we have quite a large area where we are diversified too. There you can also see on the big customers, they almost always have both Arcamskrivare and laser printers, "says Magnus René.
The Arcam electron beam is more productive and thus can print more implants in less time, will enable the company, according to Magnus René, is larger than competitors on right hip implants. The competitors with laser technology is often more niche in industries that manufacture small parts in titanium.
"Dental products make you happy with the laser," he says.
Long was Industry Fund Arcam's largest shareholder.
"It was very successful, both for them and for us. We are, I believe, Industrial Fund's second best investment ever. Data analysis company Qlik is number one."
Today ownership situation is completely different. After General Electric's bid last fall takes giant group 76 percent of the company. Elliott Capital, which has just budprocesser as investment philosophy, owns 10 percent. But hedge fund is not alone to hold on to their shares.
At this writing, there are about 1 000 shareholders of Arcam, and even if GE would buy Elliott's 10 percent, the company will not actually over the 90 percent of shares required to initiate compulsory acquisition.
GE has bought a majority think Magnus René will be very good for the company.
The same day as the bid for Arcam came, GE also bid on one of Arcam's German competitors, SLM Solutions. This commandment was not through. Instead, GE acquired another German competitor, Concept Laser.
But although he is happy, and have sold all their shares to GE, Magnus René could not help but reflect upon the situation could have been different. He seems somewhat disappointed by the lack of interest that has been around for the company among Swedish investors.
When the Industrial Development Fund in 2015 wanted to dispose of their shares was Magnus René with and tried to place the shares at any Swedish player. But it did not work.
A thought that Magnus René has about it is that Swedish investors have found it difficult to value the company. Many thought that the Industrial Development Fund wanted to charge a lot. But when GE over a year later made a bid for the company was the American group prepared to pay twice as much.
"One may wonder why this is so. We might as well have owned a Swedish industrial company. In this type of company requires that anyone can come in with a lot of resources and determination and there are many Swedish companies with the resources. "
Even when it comes to other Swedish efforts in this area are Magnus René particularly impressed.
Innovation agency Vinnova's efforts in recent years he describes as "too little, too late".
As for universities, the Royal Institute of Technology and the universities in Ostersund and Örebro was his Arcammaskin. There are important initiatives, but compared with institutions in other countries in the Arcam customer records are modest installations.
"Unfortunately Sweden has fallen a bit behind, despite the fact that we are here."
As for the customers out Magnus René Arcam is very niche on two industries that is as far in Sweden.
Among the international customers, he can count up all of the major in the aerospace industry, such as Rolls-Royce, Pratt & Whitney, Honeywell, GKN and Airbus.
The headquarters will remain in Mölndal. Magnus René, however, moved to the United States, partly because it is the fastest growing market. The workforce is now greater there than in Europe. Arcam is growing rapidly in both Sweden and abroad, and are continuously looking for new employees.
How the business will change in concrete terms, in that the company has received a new principal owner is so far hard to say.
"It still means that we have a new principal owner who has great ambition for us, and that is very good at flying. They have resources, both in terms of technical expertise and financial muscle. They are also very determined to get both this industry and for us to grow, which is reasonably good. "
When Magnus René looks to the future, it is still in orthopedics and aerospace as he sees the greatest potential.
"Within ten years, I believe that all of the metal in orthopedics will be made with 3D printing," he says.
It provides a strong growth potential because less than 1 percent of orthopedic implants in metal today are produced in 3D printers.
"When it comes to flight, we believe that the potential is at least ten times as large as the potential in orthopedics. So there is much left to do. "
In addition to product development that takes place in the efficiency and precision Magnus René believe that industrialization will be crucial in the coming years.
"This is still machinery that is something of lab equipment. Compared to a 3D printer with the cutter at any time, so the training is to run the printer long and it takes a long time to serve it. They are also not very effective. "
A industrialization think he therefore becomes absolutely critical to take in new sectors, but also to diversify in areas Arcam already inside.
There is therefore a distant thought of going outside aviation and orthopedics?
"Sometime we will do it, but not right now."
Where there is the potential?
"They talk a lot about the gas and oil industry, they have not been so keen on investment. It's not about the drills without equipment to the bottom of the drill holes. It is a very technology-intensive industry operating in a difficult environment, which require advanced materials. Nor is it so long series. On the car side and also in the truck systems, one can imagine turbochargers and such. Things where design freedom or materials will make a difference. "
Magnus René is clear that the printers Arcam sells primarily used for volume production. The 3D printer would only be a tool for developing rapid prototyping is a description that he did not want to acknowledge.
"Then utilize only lead abbreviation and not the other benefits. Should you exploit the design freedom is of course totally pointless to print a prototype and then manufacturing it in any other way where you do not have design freedom, then you can not use the prototype. To take advantage of material efficiency and design freedom you have to go into production with the technology. "
When it comes to printers for consumers, Magnus René difficult to see the same potential in the industry. The vision of consumers would print their own shoes at home instead of buying them in the store think he will not become a reality.
"Just look at the market for standard printers. Although many have a home, it is not so many who have a good enough to print something that would work to have the painting on the wall, "he says.
That people could sit at home and print spare parts for refrigerators and furniture that is broken, he believes not on.
"Then I think more on the industrial development of such spare parts are no longer manufactured."
CATHERINE HOFBAUER
cathrine.hofbauer@di.se
There is a side panel with the following text:
LAYERING - HOW DOES A 3D PRINTER
The concept of 3D printing has gained great popularity among lay people and the press.
In industry speak, however, rather on additive manufacturing, at least when it comes to using technology in production. The concept comes from the manufacturing process is done by adding materials rather than subtracting from traditional manufacturing methods such as turning and milling.
Common to all 3D printers are starting from a three-dimensional drawing, usually a CAD drawing, which is divided into layers. The actual production of the item is then done by printing a layer at a time, layer upon layer. The Arcam printers begin the process of a thin layer of powder is placed on a base plate, on which the first layer is printed by the electron beam melts just those parts depicted in the layer. When it's time to write the next layer in the 3D model, moving the bottom plate down, the machine spreads a new layer of powder and then the electron beam is directed against those parts to be melted in the layer. The object is then printed out from the bottom up.
When all the layers are printed is building the house full of powder. The powder which has not melted is blown off and the remaining will be the printed object. To save time and money do you write out as many items as possible at the same time. Several other manufacturers of metal printers use a similar method, even if the beam that melts the metal is not the same. Another way to print three-dimensional models of the metal is to use a metal wire which is advanced by means of a robot arm and melted in the right place, layer by layer.
Plastic Printers also uses various techniques. The earliest, stereolithography SLA employs a tank of liquid plastic which is hardened by means of laser, layer by layer. The most common type of printer used today prints using a plastic thread that piped out.
THE BID FROM GE
GE's initial bid of Arcam came September 6, 2016 and stood at SEK 285 per share, which was approximately 53 percent above the previous day's closing price. A unanimous board recommended the offer.
About a week later, Elliott Capital managed to acquire 6.6 percent of the shares of Arcam. A week into October flagged hedge fund that it had been over 10 percent.
On 27 October, GE raised the bid to 300 kronor per share.
In November, GE announced that the offer would be implemented, even though the company then had only been together about 74 percent of the shares.
When the acceptance period then ended, GE has control over 76 percent of the shares.
Join the InvestorsHub Community
Register for free to join our community of investors and share your ideas. You will also get access to streaming quotes, interactive charts, trades, portfolio, live options flow and more tools.