Followers | 38 |
Posts | 13358 |
Boards Moderated | 0 |
Alias Born | 07/09/2002 |

Tuesday, March 14, 2017 1:46:11 PM
Cheap Robots will rapidly impact Jobs at smaller manufacturers - http://fortune.com/2017/03/14/robots-automated-technology-workforce-jobs/
Robots are on the rise—and the greatest growth may be about to come. Some 34,600 manufacturing robots shipped in North America last year, nearly double the 18,200 that were sold in 2005, according to the Robotic Industries Association. And as costs drop and performance climbs, the use of such technology is expanding beyond the auto industry, where it has made its deepest incursions.
Robot sales have tripled in industries such as packaged foods and pharmaceuticals during the 2005–16 period. And by early in the next decade, some old-school industries that have been tough to automate, such as furniture-making, will begin to see robotics become cost-effective, according to Boston Consulting Group. Says Justin Rose, a BCG partner who follows the sector: “I don’t think it’s too bold to say that this will deeply impact large swaths of American manufacturing.”
A technician at Task Force Tips in Valparaiso, Ind. works with a Universal Robot to help automate its production of water nozzles for fire departments. The company boosted production and revenues without increasing payroll.
For decades, the costs of robots were so prohibitive that only corporate behemoths could afford them. Bots often required hundreds of hours of programming by teams of engineers and computer scientists, and a single machine might run $100,000. They also took up large amounts of floor space because they were kept inside large steel cages to ensure worker safety.
In recent years, though, a new generation of faster, cheaper bots has emerged, making them affordable for the first time for small and medium-size factories. Today a unit may cost as little as $25,000. They’re easier and safer to use because of more intuitive software, smarter visualization technology, smaller chips, better sensors, and materials such as springs that allow robots to sense and respond to human touch. That means they don’t require safety cages and can be used next to people. Some are operated by touch screen and can easily be repurposed to perform different tasks. In some cases, programming involves simply moving a robot’s arm around to “show” it how to do a job.“In just an hour, we taught the robot to move things around on our CEO’s desk,” jokes Drew Rabkewych, a sales manager at Standby Screw, a Cleveland maker of outdoor equipment parts that recently purchased two robots from a company called Rethink Robotics. Standby Screw employees quickly trained the machines to wash parts and pack them into boxes. One robot replaced 2,400 human-hours a year that were used to pack a single part. The savings allowed the company to stay profitable even when its revenues dipped last year. Says Rabkewych: “Automation and programming will be the future of American manufacturing.”
For unskilled workers, that’s bad news. A 2016 World Economic Forum survey estimated 1.6 million manufacturing and production jobs will be lost globally due to automation between 2015 and 2020.
But it could be a boon for those who are educated and adaptable. Demand is growing for jobs requiring abstract judgment and expertise in engineering, analytics, and creative design. Think job titles like robot coordinator, equipment installer, and mobile service technician.
The addition of robots transformed the workforce at Vickers Engineering, a Michigan company that makes precision-machined components for the auto, oil, and gas industries. The company boosted revenues from $8 million to $50 million and cut its factory-labor costs by a third during the decade following automation. Meanwhile, Vickers expanded from 100 employees to 180, and today only a third of its jobs involve repetitive tasks. The rest involve business operations or machine engineering, maintenance, and quality. Those positions bring salaries of $65,000 to $100,000, vs. something closer to $20,000 for, say, a factory floor operator. “The vast majority of those jobs didn’t exist before automation,” says CEO Matt Tyler.
The same kind of shift occurred at Task Force Tips when it began automating its production of water nozzles for fire departments in 2013, using four bots. The company boosted production and revenues but didn’t need to increase its 250-person payroll, says CEO Stewart McMillan. “Instead of five people doing these jobs, I have one guy running five robots that do tedious jobs longer without quality issues,” says McMillan. “Plus, the robot shows up for work every day and doesn’t get the flu, and it frees people up to use their brains.”
McMillan disagrees with the view that manufacturing jobs were lost solely to offshoring. Even if companies were to move their facilities to the U.S., according to BCG, what takes 60 to 70 workers in China might translate to six or seven American jobs with automation. “Mr. Trump needs an education on manufacturing,” McMillan says.
Only if the U.S. embraces new manufacturing technologies, BCG’s Rose maintains, will the country be able to win a greater share of global production and, potentially, see a net increase in domestic factory jobs. “You can’t do it halfway,” he says.
That requires a change in mind-set. Gone are the days when an owner might build a plant and plug people into jobs they would stick with till retirement. Today companies must stay on top of fast-changing technology and ensure employees refresh their skills. Says Rose: “Companies will have to embrace technologies quickly and train people to get ahead of the curve.”
The federal government supports some apprenticeship and college programs that prepare people for those higher-skilled jobs, and states like Ohio are opening centers to offer advanced manufacturing training.
But much of the workforce training will fall on companies. Some have started pooling resources to educate people for commonly needed jobs. Others, like Task Force Tips, started their own programs. The company invested $250,000 to create an on-site training facility where employees can learn skills related to machine tooling, programming, hydraulics, metrology, computer-aided design, and robots. McMillan, whose father founded the company, believes the program will breed more loyalty and reduce turnover in crucial, high-skilled jobs. After all, McMillan knows robots can’t quit their jobs, but people can.
Robots are on the rise—and the greatest growth may be about to come. Some 34,600 manufacturing robots shipped in North America last year, nearly double the 18,200 that were sold in 2005, according to the Robotic Industries Association. And as costs drop and performance climbs, the use of such technology is expanding beyond the auto industry, where it has made its deepest incursions.
Robot sales have tripled in industries such as packaged foods and pharmaceuticals during the 2005–16 period. And by early in the next decade, some old-school industries that have been tough to automate, such as furniture-making, will begin to see robotics become cost-effective, according to Boston Consulting Group. Says Justin Rose, a BCG partner who follows the sector: “I don’t think it’s too bold to say that this will deeply impact large swaths of American manufacturing.”
A technician at Task Force Tips in Valparaiso, Ind. works with a Universal Robot to help automate its production of water nozzles for fire departments. The company boosted production and revenues without increasing payroll.
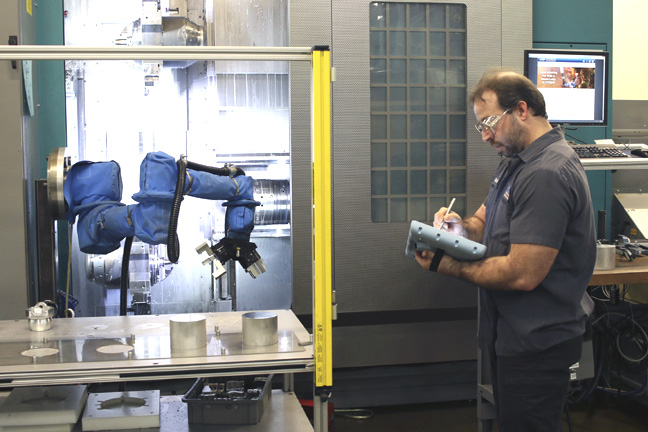
For decades, the costs of robots were so prohibitive that only corporate behemoths could afford them. Bots often required hundreds of hours of programming by teams of engineers and computer scientists, and a single machine might run $100,000. They also took up large amounts of floor space because they were kept inside large steel cages to ensure worker safety.
In recent years, though, a new generation of faster, cheaper bots has emerged, making them affordable for the first time for small and medium-size factories. Today a unit may cost as little as $25,000. They’re easier and safer to use because of more intuitive software, smarter visualization technology, smaller chips, better sensors, and materials such as springs that allow robots to sense and respond to human touch. That means they don’t require safety cages and can be used next to people. Some are operated by touch screen and can easily be repurposed to perform different tasks. In some cases, programming involves simply moving a robot’s arm around to “show” it how to do a job.“In just an hour, we taught the robot to move things around on our CEO’s desk,” jokes Drew Rabkewych, a sales manager at Standby Screw, a Cleveland maker of outdoor equipment parts that recently purchased two robots from a company called Rethink Robotics. Standby Screw employees quickly trained the machines to wash parts and pack them into boxes. One robot replaced 2,400 human-hours a year that were used to pack a single part. The savings allowed the company to stay profitable even when its revenues dipped last year. Says Rabkewych: “Automation and programming will be the future of American manufacturing.”
For unskilled workers, that’s bad news. A 2016 World Economic Forum survey estimated 1.6 million manufacturing and production jobs will be lost globally due to automation between 2015 and 2020.
But it could be a boon for those who are educated and adaptable. Demand is growing for jobs requiring abstract judgment and expertise in engineering, analytics, and creative design. Think job titles like robot coordinator, equipment installer, and mobile service technician.
The addition of robots transformed the workforce at Vickers Engineering, a Michigan company that makes precision-machined components for the auto, oil, and gas industries. The company boosted revenues from $8 million to $50 million and cut its factory-labor costs by a third during the decade following automation. Meanwhile, Vickers expanded from 100 employees to 180, and today only a third of its jobs involve repetitive tasks. The rest involve business operations or machine engineering, maintenance, and quality. Those positions bring salaries of $65,000 to $100,000, vs. something closer to $20,000 for, say, a factory floor operator. “The vast majority of those jobs didn’t exist before automation,” says CEO Matt Tyler.
The same kind of shift occurred at Task Force Tips when it began automating its production of water nozzles for fire departments in 2013, using four bots. The company boosted production and revenues but didn’t need to increase its 250-person payroll, says CEO Stewart McMillan. “Instead of five people doing these jobs, I have one guy running five robots that do tedious jobs longer without quality issues,” says McMillan. “Plus, the robot shows up for work every day and doesn’t get the flu, and it frees people up to use their brains.”
McMillan disagrees with the view that manufacturing jobs were lost solely to offshoring. Even if companies were to move their facilities to the U.S., according to BCG, what takes 60 to 70 workers in China might translate to six or seven American jobs with automation. “Mr. Trump needs an education on manufacturing,” McMillan says.
Only if the U.S. embraces new manufacturing technologies, BCG’s Rose maintains, will the country be able to win a greater share of global production and, potentially, see a net increase in domestic factory jobs. “You can’t do it halfway,” he says.
That requires a change in mind-set. Gone are the days when an owner might build a plant and plug people into jobs they would stick with till retirement. Today companies must stay on top of fast-changing technology and ensure employees refresh their skills. Says Rose: “Companies will have to embrace technologies quickly and train people to get ahead of the curve.”
The federal government supports some apprenticeship and college programs that prepare people for those higher-skilled jobs, and states like Ohio are opening centers to offer advanced manufacturing training.
But much of the workforce training will fall on companies. Some have started pooling resources to educate people for commonly needed jobs. Others, like Task Force Tips, started their own programs. The company invested $250,000 to create an on-site training facility where employees can learn skills related to machine tooling, programming, hydraulics, metrology, computer-aided design, and robots. McMillan, whose father founded the company, believes the program will breed more loyalty and reduce turnover in crucial, high-skilled jobs. After all, McMillan knows robots can’t quit their jobs, but people can.
We've run out of other people's Social Security taxes needed to subsidize our low income tax rates.
Join the InvestorsHub Community
Register for free to join our community of investors and share your ideas. You will also get access to streaming quotes, interactive charts, trades, portfolio, live options flow and more tools.