Followers | 9 |
Posts | 1597 |
Boards Moderated | 1 |
Alias Born | 01/27/2014 |
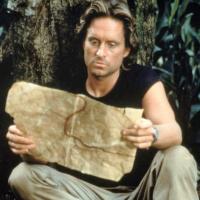
Monday, March 06, 2017 11:40:13 AM
GE's Greg Morris Discusses the Formation of GE Additive
"To get a better idea for how the path led to the creation of GE Additive, ENGINEERING.com spoke with GE Aviation’s Rick Kennedy, Media Relations manager, and Greg Morris, Strategy Growth leader."
From Michael Molitch-Hou at engineering.com - GE's Greg Morris Discusses the Formation of GE Additive - March 06, 2017
An excerpt:
The Turboprop
Manufactured through CFM International, a joint venture between GE Aviation and Safran, the LEAP engine series has already received over 13,400 orders valued at $140 billion from customers that include Airbus, Boeing and Comac. GE went on to set up an AM facility dedicated to mass production of the fuel nozzle in Auburn, Alabama, and has already begun shipping the engines to customers.
After the success of the LEAP engine, the next step for GE Aviation was to take what it had learned from the development of the fuel nozzle and apply it to something even more substantial: an actual engine. Though not as large or complex as a turbofan jet engine traditionally found in civil aircraft, GE set about developing a turboprop engine for a propeller-driven plane.
Made in partnership with Textron Aviation over the course of three years, the Cessna Denali is designed to be a $4.8 million propeller plane that can fly from Los Angeles to Chicago or New York to Miami. As impressive as it was to consolidate 18 subcomponents for the LEAP fuel nozzle, the advanced turboprop engine for the Cessna Denali saw 855 parts reduced to just 12 with 3D printing.
GE Aviation managed to consolidate hundreds of parts into a handful of components with 3D printing. (Image courtesy of GE Aviation.)
Morris relayed the story: “A couple of years ago, we formed a skunk works team internally to GE Aviation—about four or five guys that went off and took one of our small engines that was traditionally manufactured and said, ‘Let’s think about this differently.’”
To demonstrate the power of designing for AM, GE Aviation redesigned one of its legacy engines, the CT7, with 3D printing in mind. In the end, about 35 percent of the engine was made with AM, and these include large structural parts, such as the inlet frame and exhaust case, as well as intricate parts, like fuel nozzles, bearings and sumps and housing. 3D printing assemblies in one piece does away with the need for some fixtures and bolts while also enabling the creation of complex, weight-saving geometries.
With AM, GE Aviation was able to reduce the weight of the engine by 5 percent, thus cutting fuel consumption by 20 percent. At the same time, the CT7 is still capable of providing 1,650 shaft horsepower to the Cessna Denali, about 10 percent more power than other engines in the same class.
The Cessna Denali is a prop plane designed to fly like a private jet. (Image courtesy of Textron Aviation.)
Morris pointed out that, while the new turboprop engine is more efficient from a design standpoint, such a design also impacts the overall manufacturing workflow and supply chain. “On the advanced turboprop, we went from 855 distinct components down to 12,” Morris said. “That’s a very powerful capability. What we’ve in essence been able to do is combine multiple pieces into one. Instead of thinking at the part level, we think at the system level. All 855 pieces had a supply chain associated with them. You add tons of shipping logistics, multiple engineers, multiple prints, multiple CAD files.
“Now, you’ve got maybe a couple engineers working on that single part, not 855,” he continued. “You’ve cut your logistics down to building in one machine and in one location. You’ve cut your quality issues down by not having weld joints and brace joints. Then, one of the most important aspects is that you’ve gone from the digital to physical and you’ve maintained the digital thread throughout. I can take that digital file and inspect this complex part by using that digital file. I know exactly what I’ve been able to print and what I’m going to inspect for the life of the product. That is something that is going to play a more and more important role as we go forward.”
Though the Cessna Denali project was aimed at getting GE Aviation into the private jet and prop aircraft niche, the ability to 3D print one-third of an aircraft engine was proof to the company that AM was a disruptive technology.
The Formation of GE Additive
After the turboprop engine was designed, the president and CEO of GE Aviation toured Morris’s facility in Cincinnati. He was so impressed by the work that Morris’s team had done with the turboprop plane that he then brought in Jeff Immelt, CEO of GE, to see the work for himself.
Kennedy explained, “Our chairman Jeffrey Immelt was talking to the head of GE Aviation, David Joyce, and said, ‘This is not just some passing fad. Additive [manufacturing] is a disruptive technology, and there’s no turning back now. We can’t build parts that we’re designing without this technology. We can’t go back to traditional casting.”
Of course, traditional casting and other processes won’t be replaced entirely, but for GE, it became obvious that AM was essential to the future of manufacturing. According to Kennedy, David Joyce is regularly quoted as saying of 3D printing, “Do you want to be on the outside of this technological revolution, or do you want to be on the inside of the revolution?”
In other words, did GE want to continue purchasing 3D printers from others, or did it want to place itself right in the center of the AM industry? By fall 2016, it became clear that GE planned to become a central player in 3D printing by purchasing controlling shares in two leading metal 3D printer manufacturers: Concept Laser and Arcam.
"To get a better idea for how the path led to the creation of GE Additive, ENGINEERING.com spoke with GE Aviation’s Rick Kennedy, Media Relations manager, and Greg Morris, Strategy Growth leader."
From Michael Molitch-Hou at engineering.com - GE's Greg Morris Discusses the Formation of GE Additive - March 06, 2017
An excerpt:
The Turboprop
Manufactured through CFM International, a joint venture between GE Aviation and Safran, the LEAP engine series has already received over 13,400 orders valued at $140 billion from customers that include Airbus, Boeing and Comac. GE went on to set up an AM facility dedicated to mass production of the fuel nozzle in Auburn, Alabama, and has already begun shipping the engines to customers.
After the success of the LEAP engine, the next step for GE Aviation was to take what it had learned from the development of the fuel nozzle and apply it to something even more substantial: an actual engine. Though not as large or complex as a turbofan jet engine traditionally found in civil aircraft, GE set about developing a turboprop engine for a propeller-driven plane.
Made in partnership with Textron Aviation over the course of three years, the Cessna Denali is designed to be a $4.8 million propeller plane that can fly from Los Angeles to Chicago or New York to Miami. As impressive as it was to consolidate 18 subcomponents for the LEAP fuel nozzle, the advanced turboprop engine for the Cessna Denali saw 855 parts reduced to just 12 with 3D printing.
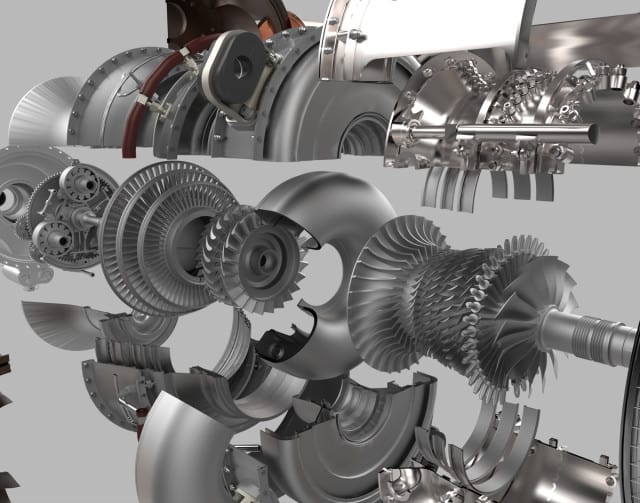
GE Aviation managed to consolidate hundreds of parts into a handful of components with 3D printing. (Image courtesy of GE Aviation.)
Morris relayed the story: “A couple of years ago, we formed a skunk works team internally to GE Aviation—about four or five guys that went off and took one of our small engines that was traditionally manufactured and said, ‘Let’s think about this differently.’”
To demonstrate the power of designing for AM, GE Aviation redesigned one of its legacy engines, the CT7, with 3D printing in mind. In the end, about 35 percent of the engine was made with AM, and these include large structural parts, such as the inlet frame and exhaust case, as well as intricate parts, like fuel nozzles, bearings and sumps and housing. 3D printing assemblies in one piece does away with the need for some fixtures and bolts while also enabling the creation of complex, weight-saving geometries.
With AM, GE Aviation was able to reduce the weight of the engine by 5 percent, thus cutting fuel consumption by 20 percent. At the same time, the CT7 is still capable of providing 1,650 shaft horsepower to the Cessna Denali, about 10 percent more power than other engines in the same class.
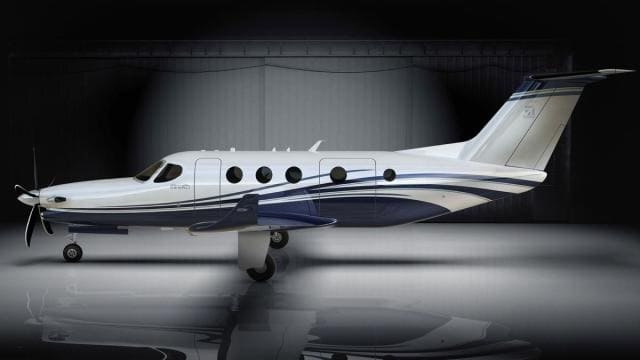
The Cessna Denali is a prop plane designed to fly like a private jet. (Image courtesy of Textron Aviation.)
Morris pointed out that, while the new turboprop engine is more efficient from a design standpoint, such a design also impacts the overall manufacturing workflow and supply chain. “On the advanced turboprop, we went from 855 distinct components down to 12,” Morris said. “That’s a very powerful capability. What we’ve in essence been able to do is combine multiple pieces into one. Instead of thinking at the part level, we think at the system level. All 855 pieces had a supply chain associated with them. You add tons of shipping logistics, multiple engineers, multiple prints, multiple CAD files.
“Now, you’ve got maybe a couple engineers working on that single part, not 855,” he continued. “You’ve cut your logistics down to building in one machine and in one location. You’ve cut your quality issues down by not having weld joints and brace joints. Then, one of the most important aspects is that you’ve gone from the digital to physical and you’ve maintained the digital thread throughout. I can take that digital file and inspect this complex part by using that digital file. I know exactly what I’ve been able to print and what I’m going to inspect for the life of the product. That is something that is going to play a more and more important role as we go forward.”
Though the Cessna Denali project was aimed at getting GE Aviation into the private jet and prop aircraft niche, the ability to 3D print one-third of an aircraft engine was proof to the company that AM was a disruptive technology.
The Formation of GE Additive
After the turboprop engine was designed, the president and CEO of GE Aviation toured Morris’s facility in Cincinnati. He was so impressed by the work that Morris’s team had done with the turboprop plane that he then brought in Jeff Immelt, CEO of GE, to see the work for himself.
Kennedy explained, “Our chairman Jeffrey Immelt was talking to the head of GE Aviation, David Joyce, and said, ‘This is not just some passing fad. Additive [manufacturing] is a disruptive technology, and there’s no turning back now. We can’t build parts that we’re designing without this technology. We can’t go back to traditional casting.”
Of course, traditional casting and other processes won’t be replaced entirely, but for GE, it became obvious that AM was essential to the future of manufacturing. According to Kennedy, David Joyce is regularly quoted as saying of 3D printing, “Do you want to be on the outside of this technological revolution, or do you want to be on the inside of the revolution?”
In other words, did GE want to continue purchasing 3D printers from others, or did it want to place itself right in the center of the AM industry? By fall 2016, it became clear that GE planned to become a central player in 3D printing by purchasing controlling shares in two leading metal 3D printer manufacturers: Concept Laser and Arcam.
Join the InvestorsHub Community
Register for free to join our community of investors and share your ideas. You will also get access to streaming quotes, interactive charts, trades, portfolio, live options flow and more tools.