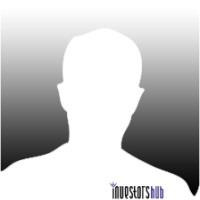
Monday, August 29, 2016 11:45:10 PM
LPPI DD: (OCKHAM'S RAZOR)
http://www.leepinc.com/
***LEEP Inc. completed condos using LEEP SIPS TECHNOLOGY. www.aptrentalsaz.com (JUST FYI - THESE WERE TAKEN DOWN DUE TO $31M LAWSUIT
LPPI & US GOV'T/ARMY:
http://militarywraps.com/additional-products/rhu/
*LEEP Inc. has worldwide patents, pretty much the same in Germany, Africa, France and Globally.
These specialized structures are very valuable in the effort to protect both U.S. and in-country national personnel from terrorist activity using the mail as a delivery mechanism.
The company disclosed that it has completed additional mail screening structures for the U.S. Government as part of a counter-terrorism initiative. Based upon the civil unrest in various parts of the world where the United States has a physical presence.
The company has now delivered and constructed these structures to approximately 50 countries around the world. The Company (LEEP) continues to build mail screening buildings for the Federal government. They recently delivered four new units for use at Embassies and Consulates in various parts of the world, including Africa and Ecuador, and currently have seven (7) more in production, some of which are for new Defense Contractor customers.
Leep, Inc. (OTCBB: LPPI) has established new standards of efficiency, effectiveness and value within the construction industry with its patented LeepCore structural building material. The Company operates a 40,000 square foot manufacturing, fabrication, and assembly facility in Kentucky. There is a big legal $31M issue happening now at LPPI, as a settlement is possible in the event avoiding court.
LEEP Inc. holds the domestic and international patents that utilizes LeepCoreTM Steel SIP technology which is a steel skin, polyurethane foam core, load-bearing structured insulated panel used to construct walls, roofs and floors for an Integrated Building System which is virtually indestructible.
LEEP has a contract with the State Department and has constructed 71 mail screening facilities installed and U.S. Embassies and Consulates across the world. The implications for this type of building are immense.
PATENTS:
LEEP has filed two additional U.S. patents that contain more than 50 claims. It also filed patents in 16 countries in order to cover 85% of the world's population & essentially 100% of worldwide industrialized population centers. It is patented in China & Europe, & received its patent in India in June 2009
United States protected patents, LEEP Inc. http://www.google.com.gh/patents/US6584740
https://www.patexia.com/us-patents/06418686/history
http://www.google.com/patents/US7107731
http://www.google.com/patents/WO2001029336A2?cl=en
https://search.rpxcorp.com/pat/US5927032A1
Pretty much the same. But, these are the UK patents:
https://www.google.co.uk/patents/EP1203125A2?cl=en&dq=inassignee:%22Leading+Edge+Earth+Products,+Inc.%22&hl=en&sa=X&ei=xeFGVK7VAcqSyAT32ILQDw&ved=0CCkQ6AEwAQ
https://www.google.co.uk/patents/US6418686?dq=inassignee:%22Leading+Edge+Earth+Products,+Inc.%22&hl=en&sa=X&ei=xeFGVK7VAcqSyAT32ILQDw&ved=0CCIQ6AEwAA
https://www.google.co.uk/patents/US6584740?dq=inassignee:%22Leading+Edge+Earth+Products,+Inc.%22&hl=en&sa=X&ei=xeFGVK7VAcqSyAT32ILQDw&ved=0CDAQ6AEwAg
WHY ARE THE DOMESTIC AND INTERNATIONAL PATENTS IMPORTANT?LEEP retained a consulting group that assisted with completing and implementing a design of a full-scale manufacturing plant. That work resuled in a set ofdrawings, specifications, and equipment vendor list. LEEP plans to usethis documentation package, permanently, to duplicate LEEP's first full-scaleproduction facility anywhere in the world.
LEEP is actively pursuing joint venture partners for the purpose of funding new manufacturing capability, and has recently had fruitful discussions with two interested and capable parties who would make a sizable capital investment in a panel manufacturing operation. The level of interest in our panel product continues to grow in a variety of markets, which justifies a new manufacturing initiative. expect to deliver those units shortly, and anticipate additional orders.
21st century construction demands technology which:
Conserves Energy: LeepCore is among the most energy efficient construction components available. A LeepCore building saves 40% or more on heating/cooling costs and the associated precious energy and fossil fuels.
Preserves the Environment: Reduced fuel consumption means fewer greenhouse gases. LeepCore uses no increasingly scarce lumber from shrinking forests. LeepCore contains no CFCs or formaldehyde, which could harm the atmosphere of your home and the planet.
Safeguards your Family: LeepCore buildings are resistant to earthquake and class 5 hurricanes, to fire, to water damage (rot, mold, and mildew), and to termites, rodents and other pests, keeping your family safer from the forces of Mother Nature and her creatures. LeepCore releases no compounds or allergens associated with “sick” buildings.
Is Affordable: LeepCore panels are price competitive with other building materials, but erect much faster, substantially reducing construction costs. The LeepCore components of a building can remain nearly maintenance free almost indefinitely, saving dramatically on upkeep over time. In addition, the reduced energy for heating/cooling means lower upfront costs on equipment, and most importantly, continued long-term savings on energy, which of late is becoming more and more critical.
The first LeepCore prototype building was constructed in Twin Falls, Idaho in 1998, demonstrating that LeepCore buildings could obtain building permits, liability insurance, building inspections, and all requirements for final inspection and use permits. Since that time, this operational commercial building has remained essentially maintenance free in the face of the subzero winters, 110°F summers, gusting winds and sandstorm conditions typical of the high-desert Snake River Canyon location.
Patented LeepCore high performance structural panels are formed from class 1polyurethane insulating foamsandwiched between structurally shaped steel sheets.
Each panel can withstand compression, tensile and shear forces hundreds of times its own weight. Optionally requiring no wood, steel or concrete frames, LeepCore buildings are a virtual thermos, maintaining indoor climates while keeping the elements and noise out.
*This is extremely important for developments near railroads, industrial areas,etc.
www.leepinc.com/product/tests
Mr. Nordstrom is Lppi's CEO - is familiar with SEC reporting requirements & regulations!
He has 25+ years continuous experience as President, CEO,& Director for various companies during his professional business career. He has been responsible for overall revenue growth, marketing, business development, profitability,financing, & strategic partner alliances, as well as management & oversight of day-to-day operational activities.
He has extensive hands-on experience in the construction & real estate development fields, & has been involved in the development, construction, management, & acquisition of more than 10 million square feet of commercial office, retail, industrial, & residential property, as well as development of more than 2,500 acres of raw land. As President & CEO of wholly owned
construction companies, he has been an active participant & decision maker in all aspects of site selection, land acquisition, as well as building construction from inception & design, through actual construction to completion. He has workeddirectly with architects, engineers, landplanners, & municipal governments, & is comfortable operating in each of those environments.
He is certified by the Federal Environmental Protection Agency as a Green Lights Ally, as part of the EPA Energy Star program, which has as its focus, energy efficient buildings & construction methods. As President & CEO of an energy service company, he was responsible for the conversion of hundreds of commercial buildings to energy efficient systems.
He has successfully negotiated & closed funding for many multi-million dollar projects during his career. He has actively participated in planning, preparation, presentation, & negotiation of financing from sources that include regional & national banking institutions,national insurance companies, & private funding sources, where he has secured more than $40million in financing.
He is a NASD Registered Principal, & founder & original owner of two securities companies that have publicly & privately syndicated real estate properties worth more than $175 million.
He has formed joint venture alliances to secure new capital for select projects, where deemed appropriate. He has served as President & Chief Executive of both private & publicly traded companies & is familiar with SEC reporting requirements & regulations. He has presided over public & private company board meetings, annual shareholder meetings, & dealt with the media as part of his responsibilities.
He has published articles in many financial magazines, has been quoted in publications such as Forbes, Fortune, Money, & U.S. News & World Report, & appeared as a featured guest on a number of television shows, including “Window on Wall street,” “Financial News Network,” & “Wall Street.”
He has served on the President’s Senatorial Committee & has met on numerous occasions with members of the U.S. Senate regarding environmental & economic issues.
He has been a member of the international Young Presidents Organization, the American Management Association, Executive Board of the Chamber of Commerce, Executive Board of the Boy Scouts of America, & the Executive Boards of various civic & charitable organizations.
Here is more info on the LPPI case (BACKGROUND)
Background in Layman’s terms- and why they are going after $31M+
Defendant, Outdoor Venture Corporation (OVC) appears to have supplied U.S. Military field tents to the General Services Administration for many years. It appears that the US Government now favors hard shell, energy efficient structures over older tent styles for some uses and longer deployment. Plaintiff’s product, LeepCore, (usable for Man-Camps), is alleged to have been successfully tested by the U.S. Army to replace cloth field tents. It is made of light steel with foam inside the panels and is hard shelled and energy efficient.
A LeepCore building for 8-20 soldiers can be delivered by helicopter or truck to front line warfare Command positions and assembled in normally 4-6 hours. The buildings can be disassembled and ready to be relocated normally in less than 4-6 hours.
The LEEP structure is adaptable for multiple military and government uses such as command centers and medical stations. The structure can have any combination of business offices, sleeping, washroom and eating areas, all with climate controlled temperatures.
During 2012 the Defendants and LEEP conducted an extensive discussion on a manufacturing JOINT VENTURE. Defendant, OVC, would manage a 50/50- owned Joint Venture and be given a license to manufacturer LeepCore panels exclusively for LEEP, Inc. LEEP, Inc. would then sell the finished product.
At that time Defendant signed a Nondisclosure and Non-circumvention Agreement. LEEP, Inc. exposed all of its Patent information and proprietary product information, sales forecasts, customer information and details of their credit relationships, including a Secured Note for $4,000,000.00 with a money lender in New York. Defendant has an affiliation with another company, Kentucky Highlands Investment Corporation (KHIC), which is a 501C-3 not for profit, operated by a Director of the Defendant.
The Defendant officially terminated all Joint Venture negotiations with LEEP. Subsequently, KHIC negotiated the purchase of the Secured Note for $4,000,000.00 from the note holder in New York for approximately $750,000.00 (19%).
Defendants then acted in a manner which harmed Plaintiff’s everyday business. Defendants, apparently under the assumption that they could now capture the assets of LEEP, Inc., claimed they were foreclosing on the Note and proceeded to seize all of LEEP, Inc.’s assets that they could. Allegedly, they paid the Landlord of Plaintiff in Pennsylvania to let them into the factory and they removed manufacturing equipment and finished inventory, including equipment and inventory belonging to third parties. Defendants then moved this equipment and materials across State lines. Defendants then hired away Plaintiff’s employees, which impeded Plaintiff’s ability to complete normal sales orders for LeepCore panels.
Some of the equipment confiscated by Defendants is owned by third parties. The two third party owners of that equipment have filed two separate actions against the Defendant in US Federal Court (Case #6:13-CV-00047-DLB and Case #14 00438 Lycoming County, PA).
In a 3rd law suit on this matter, the insurance company that is defending Defendant has now filed a lawsuit against their own client with a Motion for a Declaratory Judgment to be removed from the case as Defendant’s Counsel (Case #6:13-cv-222-DLB), and also for reimbursement of all legal fees and expenses.
Brief LeepCore Product Description
LeepCore panels are hurricane and fire rated, earthquake resistant, termite, insect, mold and mildew resistant. They are closed-cell polyurethane-filled, steel-skinned building panels. The panels only weigh approximately 3.2 pounds per square foot, so they are very easy to move and construct with. Each panel is 2 feet wide, 4 inches thick, and can be built up to 12 feet long (or high). They are assembled with an interlocking channel system that creates a solid surface that is highly resistant to weather and sound.
To view past success stories using LeepCore products and to view technical data on the product, please visit www.leepinc.com.
Benefits and Features of LeepCore
Benefits:
Permanent, Portable, Emergency Housing for new Oil or Mineral Discovery Sites
Fire Resistant- reduced insurance Premiums
Hurricane, Monsoon and Typhoon resistant
Insect resistant- no hollow space for bugs. vermin, snakes or spiders to hide
Mold resistant-no hollow space for moisture to accumulate
A human shelter against Earthquakes, Tsunami, Snow Avalanche or Forest Fire
Minimal Maintenance
Lower costs for air conditioning and/or heating
Residential and Vacation Homes, Garages, Storage Buildings, Office Buildings, Freezers…
Construction Costs are competitive with traditional methods
Completion Times usually much shorter than traditional methods
Approximate R-25+ insulation value
Could house millions in Under Developed countries
LeepCore Materials are projected to far outlast traditional stick building materials
Features:
All steel panels with foam inside
Roof and walls are interlocked for strength and bolted to a concrete pad
Can have low or high ceilings
If flooded, structures can be power washed and are mold and mildew resistant
Panels are tongue and groove with thermal-breaks for improved insulation
Minimal heat or air conditioning loss from conductivity
Longevity could be indefinite It happens
LeepCore™ Steel Structural Insulated Panel and Building System
Inventory: http://www.aptrentalsaz.com/leep.html
http://www.leepinc.com/
***LEEP Inc. completed condos using LEEP SIPS TECHNOLOGY. www.aptrentalsaz.com (JUST FYI - THESE WERE TAKEN DOWN DUE TO $31M LAWSUIT
LPPI & US GOV'T/ARMY:
http://militarywraps.com/additional-products/rhu/
*LEEP Inc. has worldwide patents, pretty much the same in Germany, Africa, France and Globally.
These specialized structures are very valuable in the effort to protect both U.S. and in-country national personnel from terrorist activity using the mail as a delivery mechanism.
The company disclosed that it has completed additional mail screening structures for the U.S. Government as part of a counter-terrorism initiative. Based upon the civil unrest in various parts of the world where the United States has a physical presence.
The company has now delivered and constructed these structures to approximately 50 countries around the world. The Company (LEEP) continues to build mail screening buildings for the Federal government. They recently delivered four new units for use at Embassies and Consulates in various parts of the world, including Africa and Ecuador, and currently have seven (7) more in production, some of which are for new Defense Contractor customers.
Leep, Inc. (OTCBB: LPPI) has established new standards of efficiency, effectiveness and value within the construction industry with its patented LeepCore structural building material. The Company operates a 40,000 square foot manufacturing, fabrication, and assembly facility in Kentucky. There is a big legal $31M issue happening now at LPPI, as a settlement is possible in the event avoiding court.
LEEP Inc. holds the domestic and international patents that utilizes LeepCoreTM Steel SIP technology which is a steel skin, polyurethane foam core, load-bearing structured insulated panel used to construct walls, roofs and floors for an Integrated Building System which is virtually indestructible.
LEEP has a contract with the State Department and has constructed 71 mail screening facilities installed and U.S. Embassies and Consulates across the world. The implications for this type of building are immense.
PATENTS:
LEEP has filed two additional U.S. patents that contain more than 50 claims. It also filed patents in 16 countries in order to cover 85% of the world's population & essentially 100% of worldwide industrialized population centers. It is patented in China & Europe, & received its patent in India in June 2009
United States protected patents, LEEP Inc. http://www.google.com.gh/patents/US6584740
https://www.patexia.com/us-patents/06418686/history
http://www.google.com/patents/US7107731
http://www.google.com/patents/WO2001029336A2?cl=en
https://search.rpxcorp.com/pat/US5927032A1
Pretty much the same. But, these are the UK patents:
https://www.google.co.uk/patents/EP1203125A2?cl=en&dq=inassignee:%22Leading+Edge+Earth+Products,+Inc.%22&hl=en&sa=X&ei=xeFGVK7VAcqSyAT32ILQDw&ved=0CCkQ6AEwAQ
https://www.google.co.uk/patents/US6418686?dq=inassignee:%22Leading+Edge+Earth+Products,+Inc.%22&hl=en&sa=X&ei=xeFGVK7VAcqSyAT32ILQDw&ved=0CCIQ6AEwAA
https://www.google.co.uk/patents/US6584740?dq=inassignee:%22Leading+Edge+Earth+Products,+Inc.%22&hl=en&sa=X&ei=xeFGVK7VAcqSyAT32ILQDw&ved=0CDAQ6AEwAg
WHY ARE THE DOMESTIC AND INTERNATIONAL PATENTS IMPORTANT?LEEP retained a consulting group that assisted with completing and implementing a design of a full-scale manufacturing plant. That work resuled in a set ofdrawings, specifications, and equipment vendor list. LEEP plans to usethis documentation package, permanently, to duplicate LEEP's first full-scaleproduction facility anywhere in the world.
LEEP is actively pursuing joint venture partners for the purpose of funding new manufacturing capability, and has recently had fruitful discussions with two interested and capable parties who would make a sizable capital investment in a panel manufacturing operation. The level of interest in our panel product continues to grow in a variety of markets, which justifies a new manufacturing initiative. expect to deliver those units shortly, and anticipate additional orders.
21st century construction demands technology which:
Conserves Energy: LeepCore is among the most energy efficient construction components available. A LeepCore building saves 40% or more on heating/cooling costs and the associated precious energy and fossil fuels.
Preserves the Environment: Reduced fuel consumption means fewer greenhouse gases. LeepCore uses no increasingly scarce lumber from shrinking forests. LeepCore contains no CFCs or formaldehyde, which could harm the atmosphere of your home and the planet.
Safeguards your Family: LeepCore buildings are resistant to earthquake and class 5 hurricanes, to fire, to water damage (rot, mold, and mildew), and to termites, rodents and other pests, keeping your family safer from the forces of Mother Nature and her creatures. LeepCore releases no compounds or allergens associated with “sick” buildings.
Is Affordable: LeepCore panels are price competitive with other building materials, but erect much faster, substantially reducing construction costs. The LeepCore components of a building can remain nearly maintenance free almost indefinitely, saving dramatically on upkeep over time. In addition, the reduced energy for heating/cooling means lower upfront costs on equipment, and most importantly, continued long-term savings on energy, which of late is becoming more and more critical.
The first LeepCore prototype building was constructed in Twin Falls, Idaho in 1998, demonstrating that LeepCore buildings could obtain building permits, liability insurance, building inspections, and all requirements for final inspection and use permits. Since that time, this operational commercial building has remained essentially maintenance free in the face of the subzero winters, 110°F summers, gusting winds and sandstorm conditions typical of the high-desert Snake River Canyon location.
Patented LeepCore high performance structural panels are formed from class 1polyurethane insulating foamsandwiched between structurally shaped steel sheets.
Each panel can withstand compression, tensile and shear forces hundreds of times its own weight. Optionally requiring no wood, steel or concrete frames, LeepCore buildings are a virtual thermos, maintaining indoor climates while keeping the elements and noise out.
*This is extremely important for developments near railroads, industrial areas,etc.
www.leepinc.com/product/tests
Mr. Nordstrom is Lppi's CEO - is familiar with SEC reporting requirements & regulations!
He has 25+ years continuous experience as President, CEO,& Director for various companies during his professional business career. He has been responsible for overall revenue growth, marketing, business development, profitability,financing, & strategic partner alliances, as well as management & oversight of day-to-day operational activities.
He has extensive hands-on experience in the construction & real estate development fields, & has been involved in the development, construction, management, & acquisition of more than 10 million square feet of commercial office, retail, industrial, & residential property, as well as development of more than 2,500 acres of raw land. As President & CEO of wholly owned
construction companies, he has been an active participant & decision maker in all aspects of site selection, land acquisition, as well as building construction from inception & design, through actual construction to completion. He has workeddirectly with architects, engineers, landplanners, & municipal governments, & is comfortable operating in each of those environments.
He is certified by the Federal Environmental Protection Agency as a Green Lights Ally, as part of the EPA Energy Star program, which has as its focus, energy efficient buildings & construction methods. As President & CEO of an energy service company, he was responsible for the conversion of hundreds of commercial buildings to energy efficient systems.
He has successfully negotiated & closed funding for many multi-million dollar projects during his career. He has actively participated in planning, preparation, presentation, & negotiation of financing from sources that include regional & national banking institutions,national insurance companies, & private funding sources, where he has secured more than $40million in financing.
He is a NASD Registered Principal, & founder & original owner of two securities companies that have publicly & privately syndicated real estate properties worth more than $175 million.
He has formed joint venture alliances to secure new capital for select projects, where deemed appropriate. He has served as President & Chief Executive of both private & publicly traded companies & is familiar with SEC reporting requirements & regulations. He has presided over public & private company board meetings, annual shareholder meetings, & dealt with the media as part of his responsibilities.
He has published articles in many financial magazines, has been quoted in publications such as Forbes, Fortune, Money, & U.S. News & World Report, & appeared as a featured guest on a number of television shows, including “Window on Wall street,” “Financial News Network,” & “Wall Street.”
He has served on the President’s Senatorial Committee & has met on numerous occasions with members of the U.S. Senate regarding environmental & economic issues.
He has been a member of the international Young Presidents Organization, the American Management Association, Executive Board of the Chamber of Commerce, Executive Board of the Boy Scouts of America, & the Executive Boards of various civic & charitable organizations.
Here is more info on the LPPI case (BACKGROUND)
Background in Layman’s terms- and why they are going after $31M+
Defendant, Outdoor Venture Corporation (OVC) appears to have supplied U.S. Military field tents to the General Services Administration for many years. It appears that the US Government now favors hard shell, energy efficient structures over older tent styles for some uses and longer deployment. Plaintiff’s product, LeepCore, (usable for Man-Camps), is alleged to have been successfully tested by the U.S. Army to replace cloth field tents. It is made of light steel with foam inside the panels and is hard shelled and energy efficient.
A LeepCore building for 8-20 soldiers can be delivered by helicopter or truck to front line warfare Command positions and assembled in normally 4-6 hours. The buildings can be disassembled and ready to be relocated normally in less than 4-6 hours.
The LEEP structure is adaptable for multiple military and government uses such as command centers and medical stations. The structure can have any combination of business offices, sleeping, washroom and eating areas, all with climate controlled temperatures.
During 2012 the Defendants and LEEP conducted an extensive discussion on a manufacturing JOINT VENTURE. Defendant, OVC, would manage a 50/50- owned Joint Venture and be given a license to manufacturer LeepCore panels exclusively for LEEP, Inc. LEEP, Inc. would then sell the finished product.
At that time Defendant signed a Nondisclosure and Non-circumvention Agreement. LEEP, Inc. exposed all of its Patent information and proprietary product information, sales forecasts, customer information and details of their credit relationships, including a Secured Note for $4,000,000.00 with a money lender in New York. Defendant has an affiliation with another company, Kentucky Highlands Investment Corporation (KHIC), which is a 501C-3 not for profit, operated by a Director of the Defendant.
The Defendant officially terminated all Joint Venture negotiations with LEEP. Subsequently, KHIC negotiated the purchase of the Secured Note for $4,000,000.00 from the note holder in New York for approximately $750,000.00 (19%).
Defendants then acted in a manner which harmed Plaintiff’s everyday business. Defendants, apparently under the assumption that they could now capture the assets of LEEP, Inc., claimed they were foreclosing on the Note and proceeded to seize all of LEEP, Inc.’s assets that they could. Allegedly, they paid the Landlord of Plaintiff in Pennsylvania to let them into the factory and they removed manufacturing equipment and finished inventory, including equipment and inventory belonging to third parties. Defendants then moved this equipment and materials across State lines. Defendants then hired away Plaintiff’s employees, which impeded Plaintiff’s ability to complete normal sales orders for LeepCore panels.
Some of the equipment confiscated by Defendants is owned by third parties. The two third party owners of that equipment have filed two separate actions against the Defendant in US Federal Court (Case #6:13-CV-00047-DLB and Case #14 00438 Lycoming County, PA).
In a 3rd law suit on this matter, the insurance company that is defending Defendant has now filed a lawsuit against their own client with a Motion for a Declaratory Judgment to be removed from the case as Defendant’s Counsel (Case #6:13-cv-222-DLB), and also for reimbursement of all legal fees and expenses.
Brief LeepCore Product Description
LeepCore panels are hurricane and fire rated, earthquake resistant, termite, insect, mold and mildew resistant. They are closed-cell polyurethane-filled, steel-skinned building panels. The panels only weigh approximately 3.2 pounds per square foot, so they are very easy to move and construct with. Each panel is 2 feet wide, 4 inches thick, and can be built up to 12 feet long (or high). They are assembled with an interlocking channel system that creates a solid surface that is highly resistant to weather and sound.
To view past success stories using LeepCore products and to view technical data on the product, please visit www.leepinc.com.
Benefits and Features of LeepCore
Benefits:
Permanent, Portable, Emergency Housing for new Oil or Mineral Discovery Sites
Fire Resistant- reduced insurance Premiums
Hurricane, Monsoon and Typhoon resistant
Insect resistant- no hollow space for bugs. vermin, snakes or spiders to hide
Mold resistant-no hollow space for moisture to accumulate
A human shelter against Earthquakes, Tsunami, Snow Avalanche or Forest Fire
Minimal Maintenance
Lower costs for air conditioning and/or heating
Residential and Vacation Homes, Garages, Storage Buildings, Office Buildings, Freezers…
Construction Costs are competitive with traditional methods
Completion Times usually much shorter than traditional methods
Approximate R-25+ insulation value
Could house millions in Under Developed countries
LeepCore Materials are projected to far outlast traditional stick building materials
Features:
All steel panels with foam inside
Roof and walls are interlocked for strength and bolted to a concrete pad
Can have low or high ceilings
If flooded, structures can be power washed and are mold and mildew resistant
Panels are tongue and groove with thermal-breaks for improved insulation
Minimal heat or air conditioning loss from conductivity
Longevity could be indefinite It happens
LeepCore™ Steel Structural Insulated Panel and Building System
Inventory: http://www.aptrentalsaz.com/leep.html
Join the InvestorsHub Community
Register for free to join our community of investors and share your ideas. You will also get access to streaming quotes, interactive charts, trades, portfolio, live options flow and more tools.