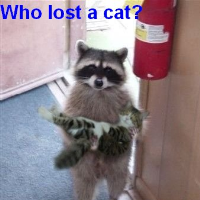
Friday, January 30, 2015 5:35:19 PM
PTOI signs contracts to sell up to 6 processors!!!
HighLights:
> marks the Company's first sale of Plastic2Oil(TM) processors
> minimum gross proceeds to Plastic2Oil will be $15 million,
> will receive a royalty of five percent of gross revenue from fuel sales
> so far PTOI has processed more than eight million pounds of waste and produced more than 700,000 gallons of fuel for sale to large industrial customers.
> engineering firm that Plastic2Oil has been working with for over a year employs more than 1000 engineers and has significant experience in permitting, installing, and operating plants.
http://finance.yahoo.com/news/plastic2oil-announces-contracts-sale-proprietary-140000020.html
===============================================================
CEO Letter to Shareholders:
NIAGARA FALLS, N.Y., Jan. 21, 2015 (GLOBE NEWSWIRE) -- To our valued Plastic2Oil (PTOI) stockholders:
Many of you have inquired about our recent press release and our recent 8-K filing with the SEC, regarding the sale of processors to EcoNavigation, LLC (EcoNavigation). More information will be released as it is appropriate, but I wanted to provide some clarity on the pilot and on the anticipated sale of processors.
First, as was indicated, a pilot production run would take place within a 120 day period for evaluation by EcoNavigation. That period began January 2, 2015 and will end May 1, 2015. The 120 day period includes pre-pilot production activities, the start-up, run, and required maintenance of the processor during the pilot. The Niagara Falls, New York processor #3 will be used in the pilot. In the past year that processor, and the rest of the Niagara Falls facility, has undergone extensive scrutiny and review by a national engineering firm. The facility requires minimal preparation to be ready for the pilot to begin. The beginning date will be determined by EcoNavigation.
Former Plastic2Oil Chief of Technology John Bordynuik, now acting as a consultant for PTOI will provide guidance as required. The national engineering firm will supervise the pilot for EcoNavigation. The current plan is for the pilot to be completed within the 120 period and EcoNavigation will be responsible for costs associated with the pilot. Plastic2Oil will bear none of the costs associated with the pilot. The tonnage to be processed during the pilot will be determined by and provided by EcoNavigation.
While EcoNavigation is a privately held start-up company, it has strong financial and business relationships. During our negotiations with EcoNavigation we have become familiar with their management team and have concluded EcoNavigation has access to both sufficient capital and plastic waste generators to complete the pilot. We are confident the pilot will reach a successful conclusion.
Upon the successful completion of the pilot, expected on or before May 1, 2015, we are equally confident EcoNavigation has the financial capability to complete the initial purchase of processors for sites to be located in the state of New York, or elsewhere. We currently have two processors in inventory that are 75% complete. Additional processors and other equipment will be fabricated by outside suppliers, selected by Plastic2Oil, as demand for processors by customers develops. Our contract with EcoNavigation is for a minimum of six processors over a three year period. We continue in negotiations with other purchasers.
Plastic2Oil is a lean company with few employees and nominal associated overhead costs. We believe our technology is our most valuable asset and the company will begin realizing that value upon the sale of our first processor. The strategy of our founder, John Bordynuik has been to bring the technology to market with minimum dilution to our loyal shareholders. That continues to be a core objective of our current management team. We will issue further updates on the pilot and the sale of processors as circumstances warrant.
=================================================================
ISIS Article:
The most successful and closest to commercial production to-date is a patent-pending process developed by the company Plastic2Oil based in Niagara Falls, New York, in the United States [2]. It turns unsorted, unwashed waste plastics into clean low sulphur fuel without the need for refinement. The latest plant, improved and scaled up in successive versions since 2009, processes 40 tons of waste plastics a day, converting 86 % of the waste into liquid fuel, powered predominantly by low-boiler gas produced in the process. The cost of operating the processor, including utilities, staff and depreciation works out to be $0.11 per gallon. This is highly competitive even as crude oil prices continue to drop below US $50 a barrel and wiping out thousands of jobs [3].
John Bordynuik on a pile of mixed unwashed plastic waste, from [5]
It began when John Bordynuik designed a laboratory desktop processor unit that uses a proprietary catalyst to turn mixtures of unwashed waste plastic into marketable fuel [4]. According to an extended interview in Niagara Magazine in 2010 [5], Bordynuik started life as a computer whizz kid who learned to programme at the age of 10, lived in Toronto for more than a decade where he served as Director of Research and Development for the Ontario Provincial Legislature, then moved back to Niagara and set up John Bordynuik Inc. (JBI), a company dedicated to technical fixes. One of the first fixes was to recover lost data for MIT’s Computer Science and Artificial Intelligence Laboratory, and then for NASA.
After his successes with MIT and NASA, Bordynuik began buying up abandoned data storage devices, especially old data tapes, eventually building up an engineering archive of 60 million documents, containing a lot of research data to be mined. Perhaps it was information from that archive that led him to the pyrolytic breakdown of plastic wastes into fuel oil as a way to fixing the world.
Bordynuik focussed on non-recyclable waste plastics [4], which according to the Environment Protection Agency (EPA) constituted over 92 % of waste plastic in 2010, and growing at 8 % a year. He saw a critical need for a viable and environmentally sound general purpose recycling process for hydrocarbon streams that fall outside accepted refinery standards, and would have been landfilled or melted into products of low value.
The 1-gallon desktop processor was soon scaled up to 3 000 gallons, and finally up scaled to the current 40 ton/day processor. At every stage, the process and products were assessed and validated and the design improved. It is instructive to follow his progress.
Bordynuik pointed out some of the challenges at the start [4]: “Waste plastics have some of the most undesirable properties of any substance when considered for thermal processing. Plastics have low-surface area, poor heat transfer, exceptional tensile strength and are considered an insulator. During the melting process, plastics absorb heat and will stick to anything cooler, resulting in exigent “glue” that will seize or bind some of the largest high-torque feed technologies.”
At the time, most processes were based on a batch method. The resultant product is typically a low flashpoint, unstable, unsaturated mix of random hydrocarbon chains, ranging from c5 to c80. Unsaturated alkenes are undesirable in fuels and highly reactive. This results in poor energetic value, high residue and high total hydrocarbon emissions (THCs) when burnt. Large refineries generally refuse such products due to their low value, impurities, acids, and possible damaging contaminants. The residue (coke) resulting from the batch method can also be a problem as it forms on the wall of the reactors or tubes, and must be scraped or drilled out. The emissions from batch-based processes are generally not desirable and usually need a thermal oxidizer to incinerate volatiles, organics and low boil gas created in the process.
Bordynuik decided on a list of ‘must haves’ for the process that included viability, accepting waste continuously with minimum requirements (no extrusion), accepting composite waste materials with metals, operating on the off-gas generated from cracking the hydrocarbon chains, anti-coking, and good seals.
More:
http://www.i-sis.org.uk/Waste_Plastics_into_Fuel_Oil.php
z
FEATURED Cannabix Technologies Launches New Compact Breath Logix Workplace Series and Prepares for Delivery to South Africa • May 7, 2024 8:51 AM
Moon Equity Holdings, Corp. Announces Acquisition of Wikolo, Inc. • MONI • May 7, 2024 9:48 AM
NanoViricides Reports that the Phase I NV-387 Clinical Trial is Completed Successfully and Data Lock is Expected Soon • NNVC • May 2, 2024 10:07 AM
ILUS Files Form 10-K and Provides Shareholder Update • ILUS • May 2, 2024 8:52 AM
Avant Technologies Names New CEO Following Acquisition of Healthcare Technology and Data Integration Firm • AVAI • May 2, 2024 8:00 AM
Bantec Engaged in a Letter of Intent to Acquire a Small New Jersey Based Manufacturing Company • BANT • May 1, 2024 10:00 AM